In a major technical achievement, Boskalis completed the East Hub Block 15/06 project in Angola. This challenging job involved the preparation and execution of the anchoring and hook-up of the mighty FPSO Armada Olombendo, as well as assisting during the installation of the umbilicals, risers and flowlines.
The Armada Olombendo is a 382-meters-long and 58-meters-wide floating production, storage and offloading (FPSO) vessel that is able to produce 80,000 barrels of oil per day. “Given our leading role and the wide-ranging involvement of multiple Boskalis disciplines, this was a landmark project,” says Project Manager Aart van den Hoonaard.
This complex project was characterized by an intense collaboration between the various Boskalis disciplines. Aart stresses: “This was a large integrated project, with Boskalis behind the wheel. Not only were we responsible for the complex technical designs and the management of four of the five phases, we also had to manage the entire procurement process, the logistics and the operational side.”
Colleagues from the Installation & Intervention team of the Boskalis Offshore Energy division teamed up with colleagues from Subsea Services for the underwater work with divers. In addition, the Survey department played a key role, as did the colleagues from the Procurement, Transport and Logistics departments. Boskalis deployed a large number of its own vessels and at peak periods, the project team represented about 100 people, including the crews on the vessels.
Preparations and Phase 1
During the first phase of the project, Boskalis was responsible for the design and installation of an ‘ingenious anchor pattern’ on the seabed to keep the FPSO in exactly the right position, explains Aart.
The hoses, cables and chains for keeping the FPSO in place were pulled and guided through the turret (the ‘tower’ at the bow of the ship that can rotate 360 degrees) onto the FPSO. “We spent more than six months working on the engineering for the installation of the anchor pattern before starting with the actual operation. We laid a complex woven pattern of chains on the seabed.”
To get the job done, he stresses, Boskalis had to prepare a chartered Construction Support Vessel (CSV), which it then deployed to install a total of nine suction piles: enormous steel buckets weighing 90 tons that are 11.5 meters high and have a diameter of 6.5 meters.
Stephanie de Decker, the Marine Operations Manager for Phase 1, explains: “You position them on the seabed with the open side pointing down and then pump out the water. The suction piles stay in place due to a combination of seabed friction and lower pressure inside the piles.” A heavy, 800 meter long chain is attached to each suction pile. This ground chain is connected to a spiral strand wire (a 530 meter long steel cable with a plastic casing). The last section of the anchoring system is the fairlead chain connecting the anchoring to the FPSO through the turret.
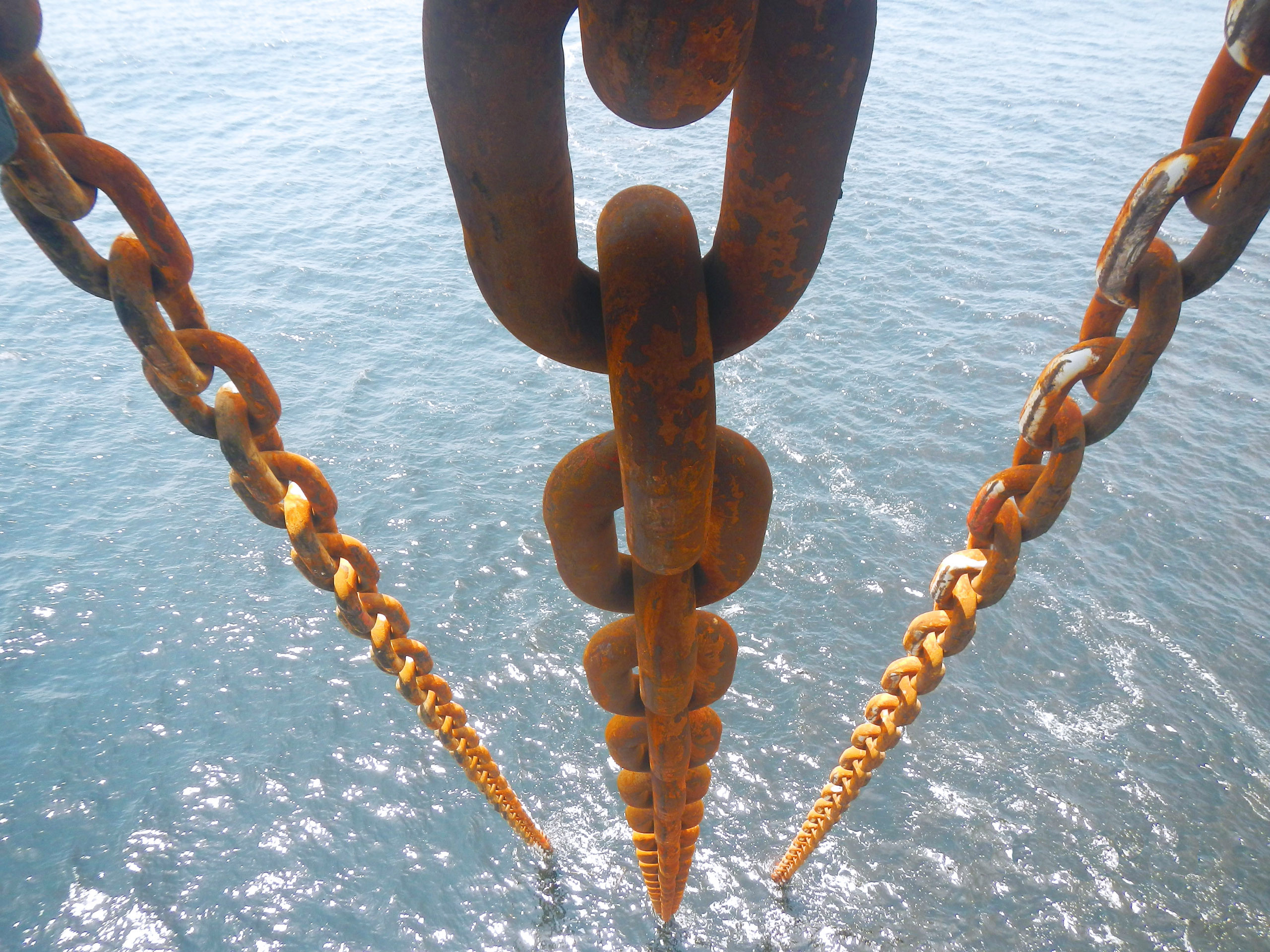
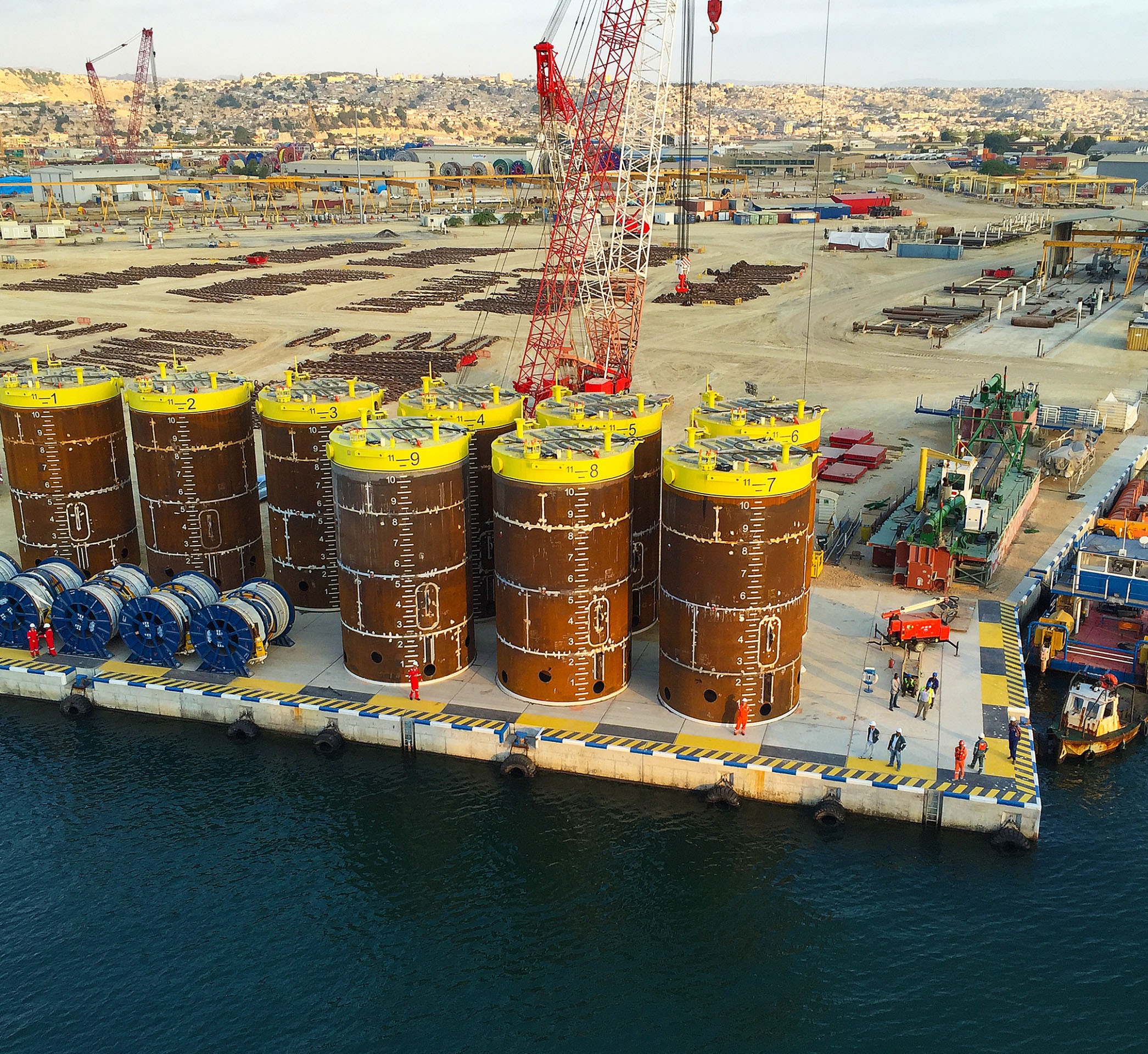
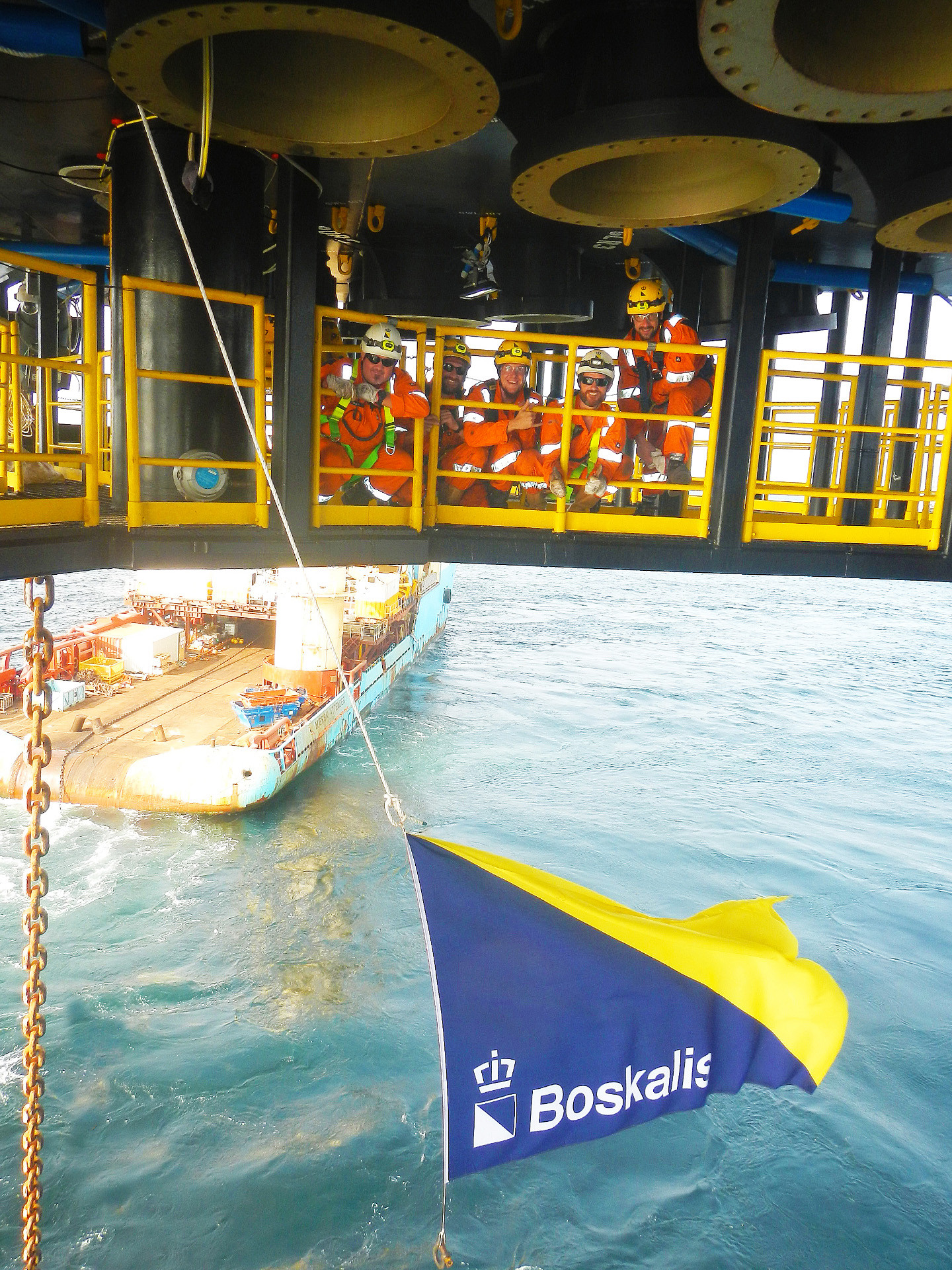
Phases 2 to 5
The second phase that followed involved the mooring hook-up: linking up the enormous chains and pulling them in through the turret. Naval Architect and Lead Engineer Jeroen Jacobs, who was responsible for areas that included drafting the operational concepts and the perfect coordination of the different activities, outlines this phase: “We moved the FPSO to exactly the right location using a range of Boskalis Anchor Handling Tugs: Union Manta, Union Princess, Union Sovereign, Union Lynx and Union Bear. The next step involved literally fishing the chains off the seabed, connecting them to the cable on a winch in the turret and then pulling them onto the bows of the FPSO. The chains were then pulled on board in turn and tensioned.”
Once the FPSO was fixed into position, Phase 3 started. This involved installing the seawater suction lift hose that is used to pump seawater to the vessel.
“Phase 4 involved helping with the installation of the complex umbilical systems for pumping up the oil and controlling the underwater equipment from the FPSO,” continues Jeroen. “This is the so-called ‘SURF’ hook-up which is an abbreviation for subsea umbilicals, risers and flowlines. During this phase we were busy helping a third-party connect a range of oil lines. During the final phase of the project, we assembled a floating flexible line on land for removing the oil, the offloading hose, before taking it out with the Union Lynx and installing it on the FPSO.”
We spent more than six months working on the engineering for the installation of the anchor pattern
Unique conditions
Captain Kevin Tate, the Marine Operations Manager for Phases 2 to 5 describes the local conditions: “An unusual feature of this project was the strong current from the Congo River. Even though we were working 130 kilometers offshore, you could still feel the force of the water flowing from the hinterland through the Congo River into the sea. The direction of the current sometimes switched 90° within 30 seconds. The dynamic positioning system of our CSV found it difficult to cope sometimes and we even had to shut down on occasion,” he recalls. “Technically, of course, there are always overlaps between our projects. But the conditions on each project are unique. There are always puzzles to solve and that’s what keeps our job so fascinating!”