When Boskalis successfully completed a unique, dual vessel float-over operation of the Aasta Hansteen topside owned by Statoil, several engineering records were accomplished.
Boskalis, through its subsidiary Dockwise, was responsible for both the transportation of the Aasta Hansteen SPAR substructure and topside from South Korea to Norway and the topside installation. In this remarkable project the company has transported the heaviest SPAR-FPSO ever, carried out the largest catamaran barge construction and topside float-over, and worked more than 100,000 hours without a single lost time injury.
Two of the world’s largest heavy-lift carriers, the Dockwise Vanguard (SPAR) and Dockwise White Marlin (topside) performed the transports. Both the scale and installation method make Aasta Hansteen a truly exceptional project.
Project Director Bas Polkamp outlines the challenges and each stage of this special project, which he stresses, was all about teamwork!
Bas, could you outline the various key phases of the project?
“To provide some background first. The Aasta Hansteen SPAR-FPSO is a gas production and storage platform, which will be operated at the Aasta Hansteen field, approximately 300 kilometers off the coast of Norway, above the Arctic Circle in depths of more than 1,300 meters. The SPAR consists of the hull/substructure and a topside.”
“Hyundai Heavy Industries (HHI) contracted Dockwise to carry out the transport of the SPAR hull from the fabrication yard in Ulsan, South Korea, to a fjord near Stavanger in Norway. As such, a ‘relatively straightforward’ part of the operation, even though it is a huge structure. Just the hull alone is an enormous cylindrical buoy with a diameter of 50 meters, length of 198 meters and weight of 46,000 tons. The hull was transported horizontally on our semi-submersible heavy transport vessel Dockwise Vanguard via the Cape of Good Hope in 59 days, arriving in Norway at the end of June.”
“Subsequently, we transported the 24,300-ton topside from Ulsan. This operation was carried out with the White Marlin, the newest and second largest vessel in the Dockwise fleet. With the design and detailed engineering carried out at the company’s offices in Shanghai, Houston and at our headquarters in the Netherlands, a project site team was then based at a Chinese outfitting yard supervising the construction and installation of four big skid tracks on the White Marlin. In the meantime, the topside was placed on skid tracks on the quayside. Once all the preparations were finalized the topside was pulled onto the vessel using dozens of strong wires.”
“In addition to transporting the two main platform components to Norway we were also tasked with the installation of the topside on the substructure. Following its arrival in Norway the SPAR was offloaded from the Vanguard and moved into an upright position and submerged at a safe and sheltered position in the fjord by a third party. Here the substructure was waiting for the installation of the topside.”
Can you explain how this topside installation was carried out?
“Once the White Marlin arrived in Norway, the topside was transferred onto two S-class vessels, the smallest in the Dockwise fleet. After accurately positioning these two vessels on either side of the White Marlin, they started de-ballasting whilst the White Marlin ballasted down and maneuvered out from underneath. The result was a ‘catamaran barge structure’ with the topside linking the two hulls.”
“Then the catamaran barge configuration had to go to the ‘mating location’ where the topside is installed on the substructure. At this stage there were four tugs alongside and one deployed for contingency purposes. With this marine spread, we travelled to the mating location 16 nautical miles away. This was all taking place inshore, within the fjord. The catamaran barge with the topside was safely towed out to the vertical SPAR hull. The float-over process started with the ‘entry operation’, where the topside was positioned above the substructure. We used the tugs followed by using mooring-mating wires for further fine-tuning the positioning. Once the topside was in the right position the mating operation commenced: the substructure was de-ballasted and the catamaran barge was ballasted down. In other words, another load transfer, yet this time from the catamaran barge to the substructure.”
Being prepared is key?
“Preparing for this final operation alone represents more than two years of detailed engineering. In the last four weeks of the project, we established an office on-site with more than 50 people based there, including representatives from the owner Statoil and our client HHI. We mobilized the core team on 22 November and successfully completed the dual float-over on 14 December – in just three weeks!”
Given the nature of this extraordinary project, what would you say was the biggest challenge?
“Undoubtedly the weather! Executing this operation in the Norwegian wintertime was for sure the biggest challenge. The project was extremely weather sensitive, with very strict limits on the maximum current and wind speed that could be handled. And at this time of the year, there was a low pressure front coming every few days. We had to have many go/no-go meetings to decide whether it was safe to carry out the operations in the next time window.”
“There are big storms at that time of the year, with gusts of up to 40 knots. In fact, we had to wait four days on one occasion for a suitable weather window. We employed a dedicated meteorologist who was providing a presentation to the team every four hours and outlining whether we could proceed to the next stage. The probability of three days of good weather was actually once every 50 days, so we were very lucky.”
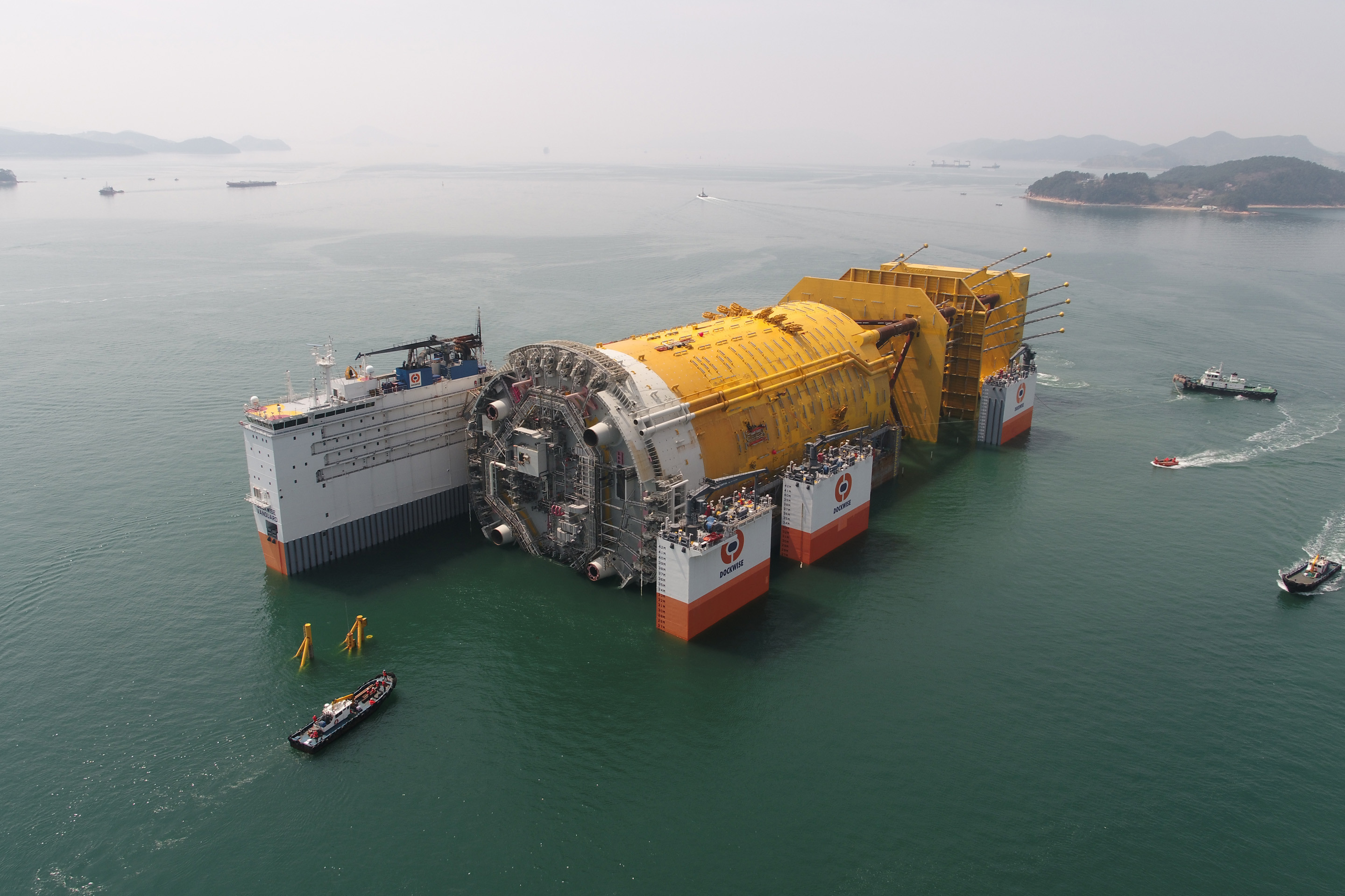
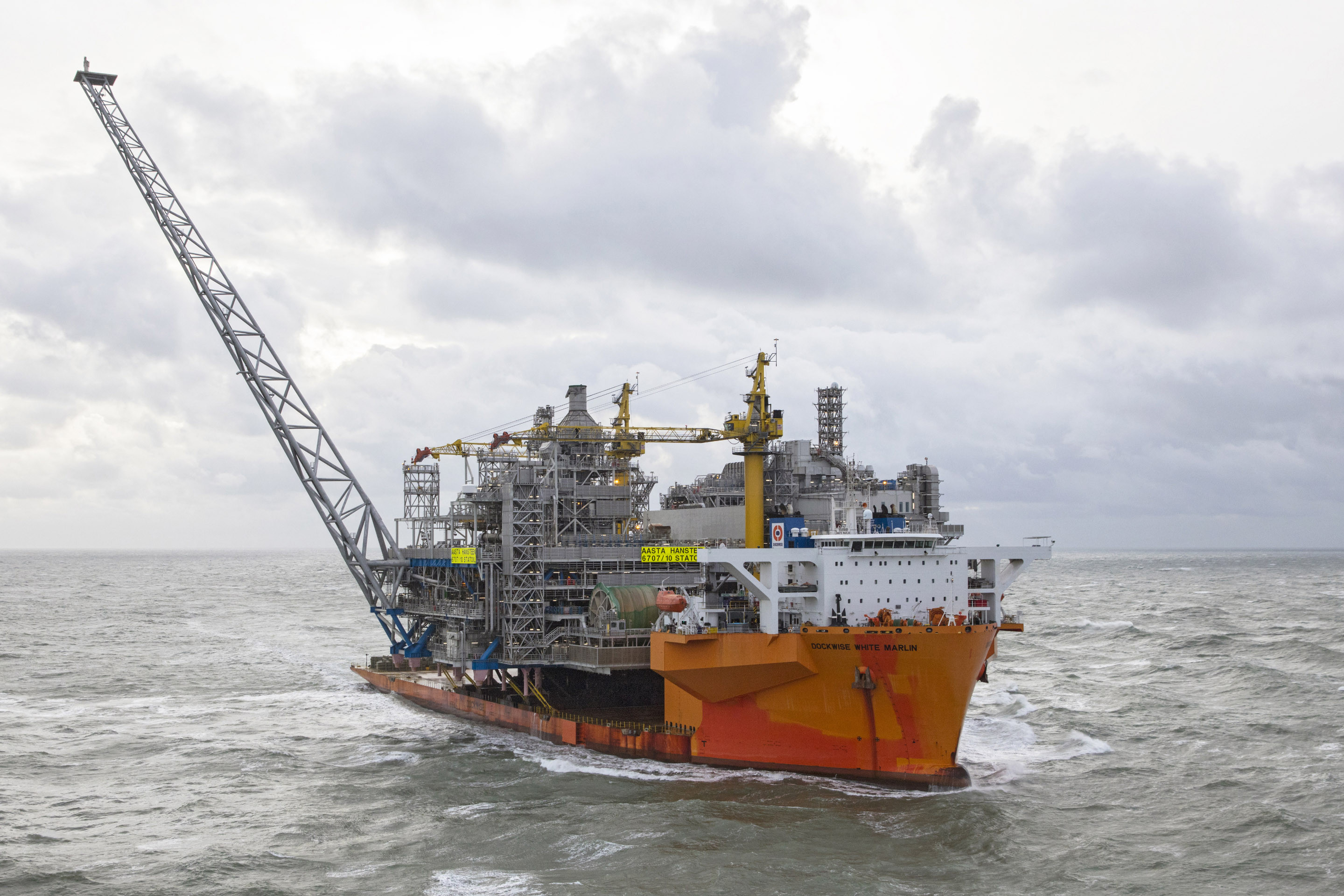
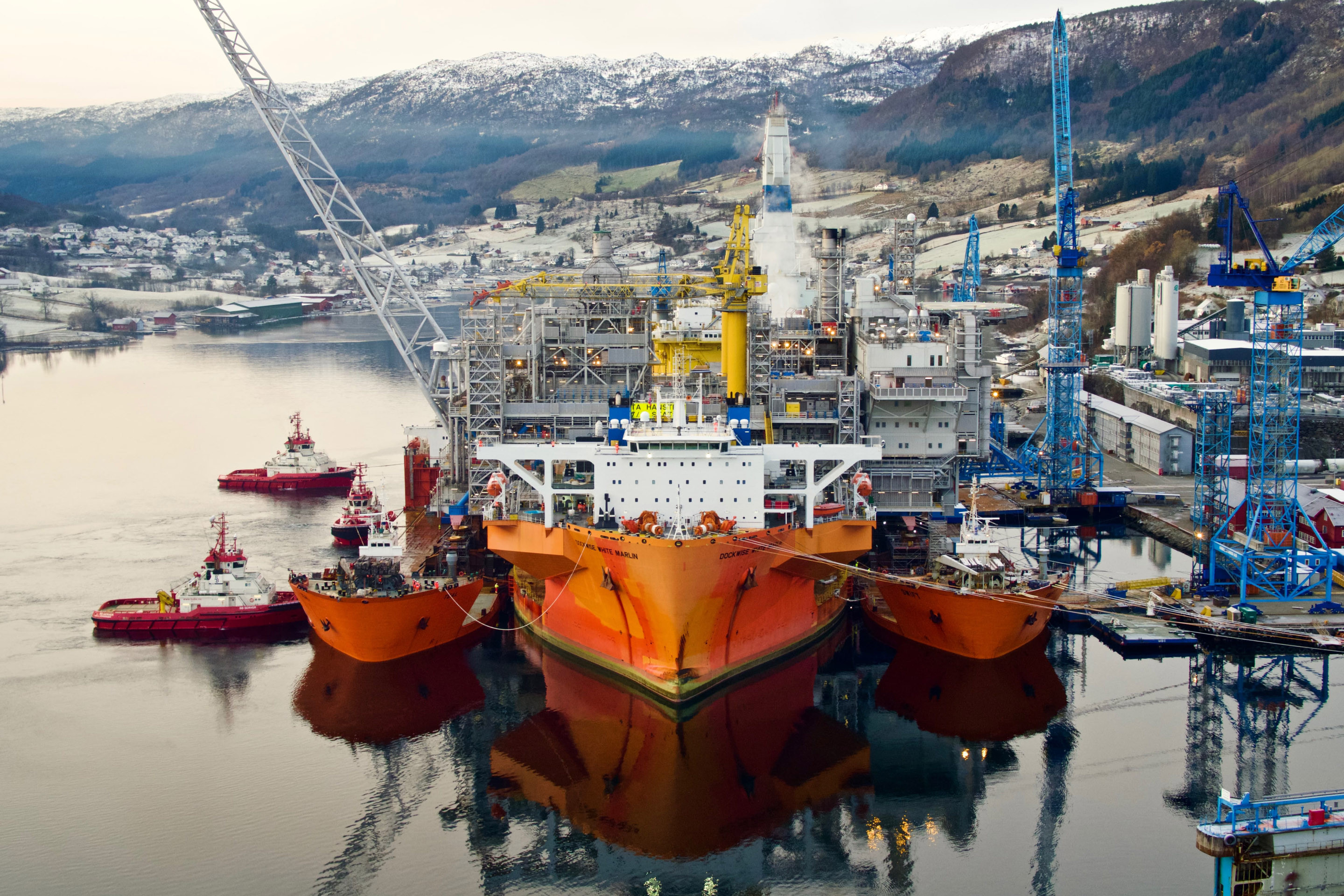
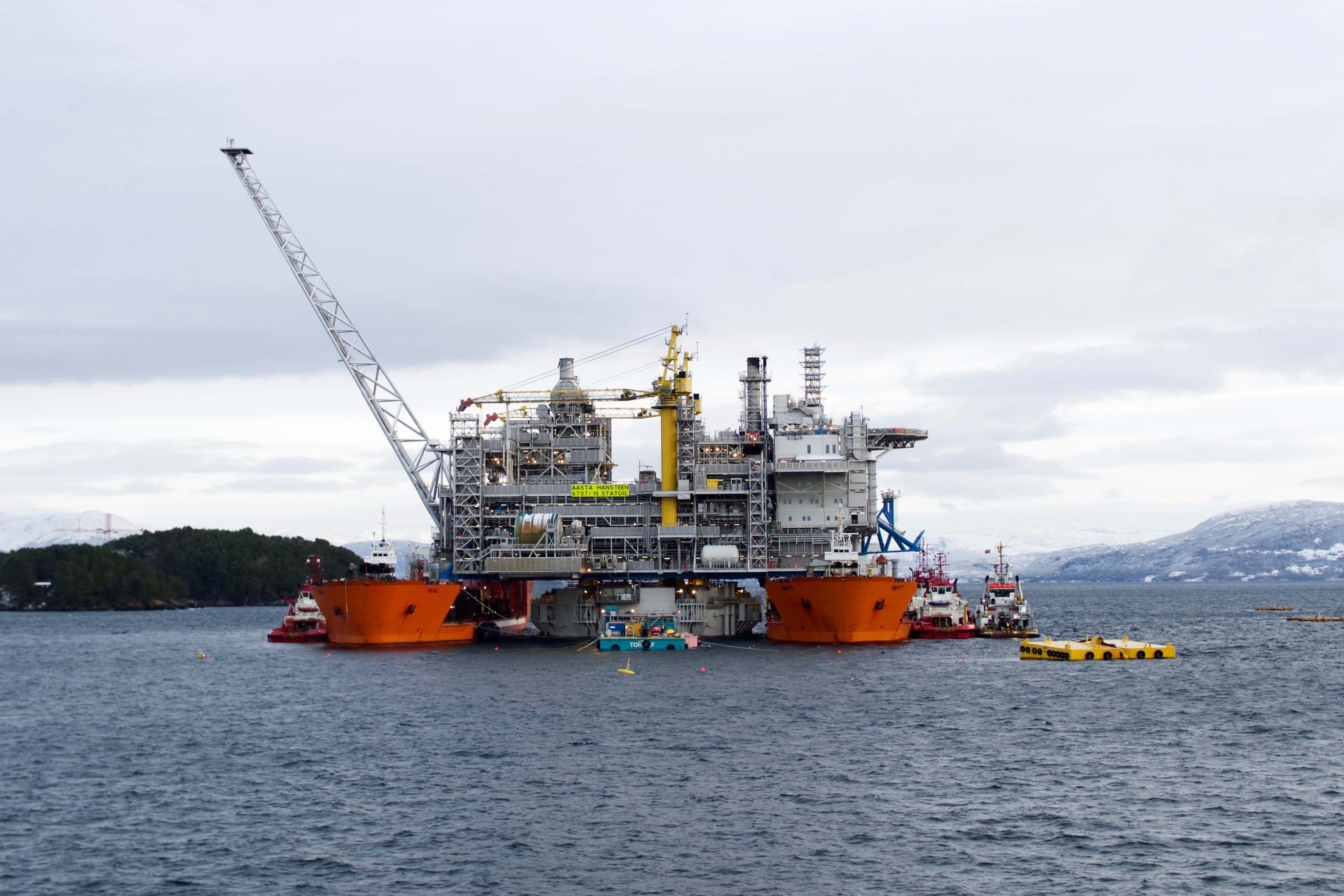
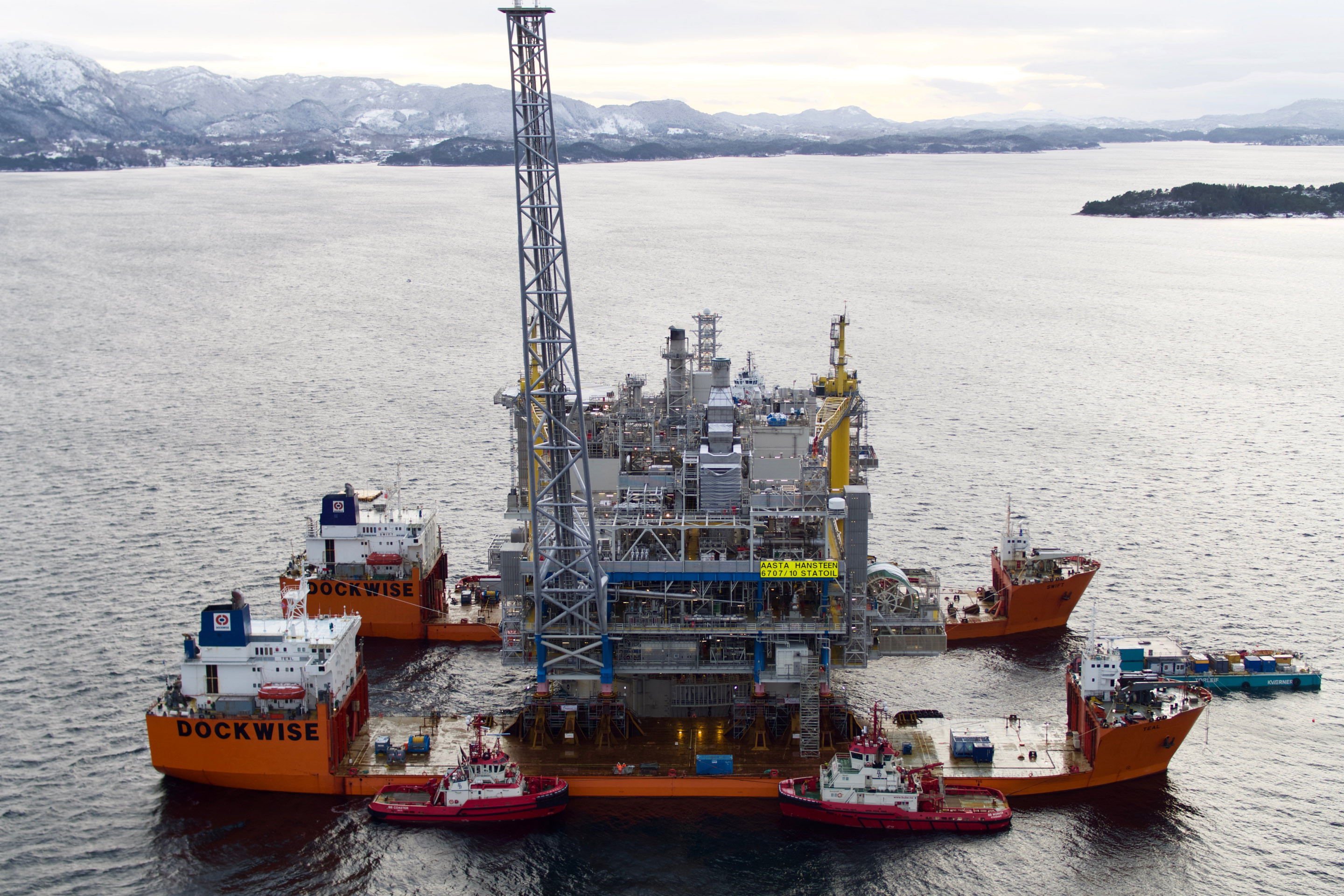
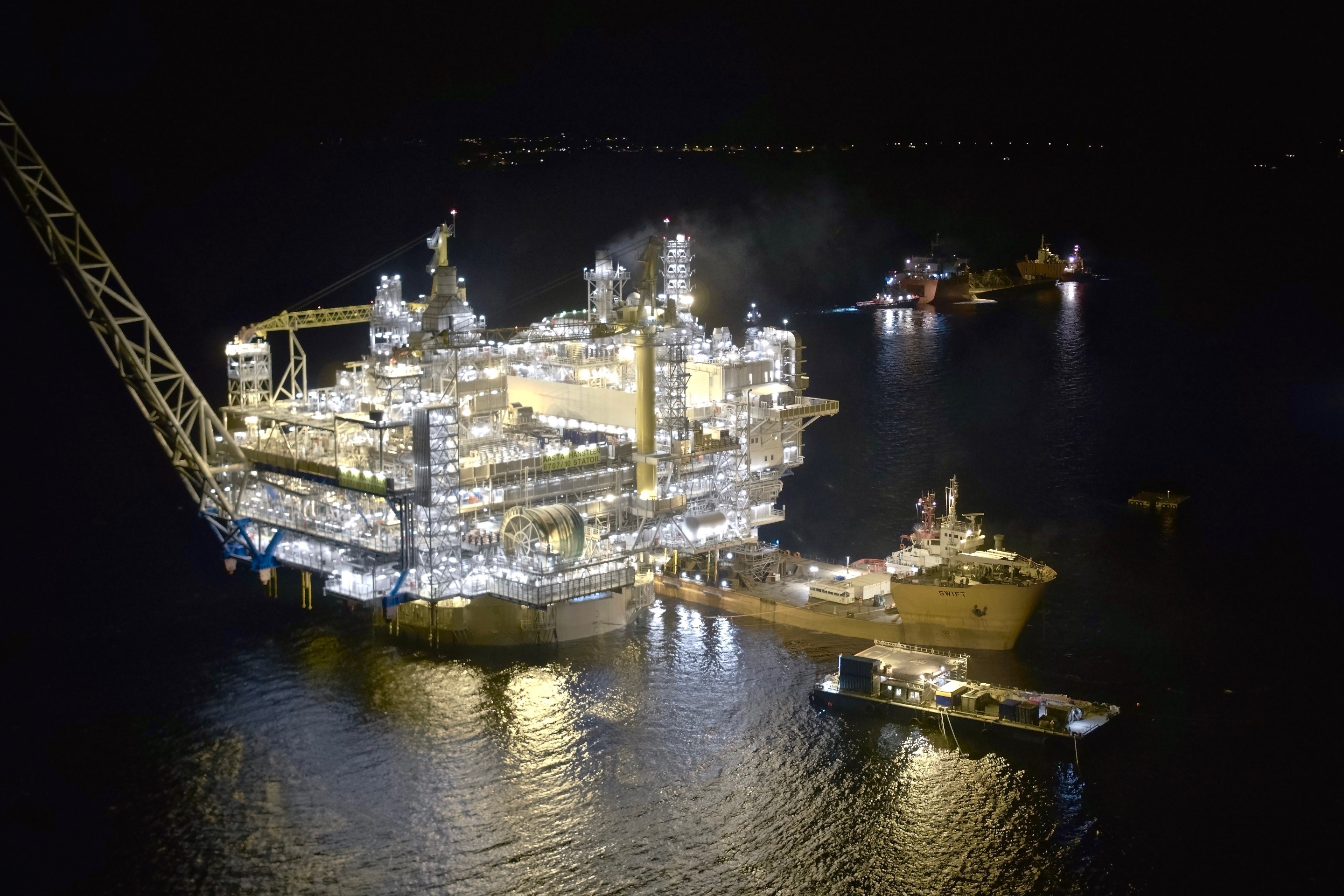
And the many weeks of simulation exercises proved their worth?
“Yes when it was time for the float-over operation — which was executed absolutely flawlessly — the tow master was instructing all of the tugs and the captains were all responding promptly. We really saw how the simulator exercises carried out at the Maritime Research Institute Netherlands (MARIN) proved to be invaluable. The tow master actually said that this was not the ‘first time’ he had performed the operation because he had carried it out many, many times on the simulators. The maneuvering with the tugs, de-ballasting the SPAR substructure and ballasting the two vessels had all been simulated extremely realistically — as it happened in the field. The whole operation took 26 hours to pump all the water out and de-ballast the vessels so we could release the two S-class vessels.”
“Communication was absolutely crucial. The team had all worked together in the simulation exercises, and this showed as it worked perfectly well. It was vital to have the same team and great, dedicated operational people. Of course we have the right assets – the White Marlin, the Vanguard, the tugs, but the most important thing is the people! It is all about teamwork! They know exactly what’s going on and are totally committed. Everyone is working together and communicating properly to make it happen. All the dry runs and teambuilding was a really rewarding side of this project.”
Safety is always top priority — this project has a fairly impressive record of 100,000 hours without lost time injuries?
“Our on-site HSE manager actually stressed on the completion of the project that we had carried out 100,000 hours, with not so much as a single plaster!”
“A very important focal point throughout the float-over operation was the danger of fatigue. The guys are so proud to be working on such a unique project that they want to be involved all the time, especially when the key parts of the operation are taking place, but we limited shifts to 12 hours only. We made sure we had enough people for back-to-back shifts. At the peak there were probably 150 people involved including the crew.”
“Another very important element for safety was the team working together and communicating efficiently. We brought the captains in at a very early stage; this was particularly vital for the two captains who had to work in tandem in the catamaran configuration. Additionally, we deployed a special operations manager to oversee the float-over installation. Everyone was introduced to each other early on in the process so each member of the team understood the complexity of the operation and how best to work together. We did many dry runs just focusing on teambuilding and communications.”
Going forward, would you say this is effectively a blueprint for this type of project?
“Yes I think it is fair to say this can be considered a blueprint for these type of very sizable topside installation projects. Of course there are always things to fine-tune and take forward as lessons learnt.”
“This was first of all the world’s largest spar platform ever transported and this dual barge technique with the two S-class vessels and catamaran barge configuration was also a world first. Both the mega-scale and installation method are truly exceptional.”
“The engineering challenges were immense. We had to consider how to transfer these enormous loads from one vessel to another, using huge shock absorbers and support structures. Although we have decades of experience, we couldn’t just rely on past experience, we had to make it happen from scratch, as it had simply never been done before! And crucially, Statoil was delighted, we even completed the coupling of the topside with the substructure much faster than Statoil had expected. Looking back the whole team are immensely proud to have been involved in the Aasta Hansteen project.“