As the historic COP21 deal is signed at the UN Paris Climate Summit, the world’s eyes are even more focused on the potential of wind energy.
There are currently some 130 offshore wind farms in operation around the world and a lot of offshore wind projects are planned in the next few years. Most of these new wind farms will be constructed in Northern Europe, yet other countries such as Japan, China and the United States are beginning to enter the stage.
Generally, offshore wind farms have entered the next phase of development by becoming larger with higher capacity turbines – with the mighty 10MW turbine not so far away.
Bart Pröpper, Boskalis Business Unit Director Offshore Renewables comments: “The upscaling of wind farms means that they can be constructed more efficiently. Boskalis is already one of the five major construction players in the offshore wind market. We have made our mark with successful projects like West of Duddon Sands, SylWin1 and DolWin2 and we are currently constructing the Wikinger and Veja Mate offshore wind farms.” “In July, we were awarded the Offshore Balance of Plant contract by Vattenfall for the construction of the Aberdeen Offshore Wind Farm. The use of suction bucket jacket foundations in conjunction with the large wind turbines and the use of high capacity 66kV power cables makes this project unique.”
“We offer a broad and complex range of services. In addition to the transport, delivery, installation and protection of the foundations, we can also deliver those services for substations, turbines and we can supply and lay cables. We are also taking on a larger share of the construction, procurement and engineering work on projects – areas where logistics and risk management play an increasingly important role.”
Wikinger logistics and underwater noise mitigation challenges successfully overcome in just 90 days.
With 70 jacket foundations and 286 piles, between 29 and 51 meters long, having to be installed in just 90 days, the 350MW Wikinger Offshore Wind Farm project (Wikinger) represented one of the largest logistical challenges Boskalis has ever faced in the offshore wind sector. Some 20 vessels and 600 people worked on this fascinating project. In addition, stringent environmental requirements resulted in very tough underwater noise mitigation measures.
Boskalis was awarded the Wikinger project from Iberdrola Renewables Offshore Deutschland GmbH for the partial construction of the wind farm in December 2014. Wikinger is located in the German section of the Baltic Sea, 34 kilometers north-east of the island of Rügen. Rob van Gemert, Boskalis Project Director for the Wikinger project explains: “We had been working on the pre-engineering agreement since July 2014 to assist the client in obtaining its final permits, and acquiring the equipment we needed with long lead times.”
Ideal for pin piling
This included the 137 x 36 meters crane barge Giant 7, originally designed as a semisubmersible barge like its sister vessels Giant 5 and 6. Because of Wikinger Boskalis made the decision to convert it into a construction barge with an integrated pedestal for a permanent crane. The Giant 7 is equipped with a huge 1,000-ton Liebherr crane, an accommodation unit for around 70 people and an 8-point mooring system for flexible utilization. “She is ideal for construction works in Baltic Sea conditions and especially, pin piling installation.”
Other early preparations to customize the fleet for this project included the design and construction of the pre-piling template, which is deployed from the Giant 7. “For this project the Giant 7 and the template are a perfect pair!” Preparations started in the first quarter of 2015 and the template and lifting tools were ready just before sail out in April 2016.
Logistical challenges
When considering logistics, Wikinger is undoubtedly the most challenging offshore wind project Rob has been involved in. “Nearly all of the vessels that we deployed are our own, it was really an intensive mobilization period and a big logistical challenge. Plus we had five consecutive trains of transport, pin pile installation, pile dredging, jacket installation and finally grouting with different vessels and different progress rates.”
“We transported the materials from four different locations in Spain and Denmark to Sassnitz-Mukran in Germany, where they were stored in port on either barges or vessels.” The jackets were transported by two Dockwise vessels (Swan and Tern), which made seven journeys from Spain to Germany each, as well as various Boskalis anchor handling tugs and barges. Offshore four sets of piles were transferred onto the Giant 7 using barges.
Installation
The actual installation work encompassed pre-piling (the installation of the four steel piles for each jacket with the Giant 7), dredging and cleaning in and around the piles, installing the jackets with the Taklift 4 sheerleg crane and bonding the piles and jackets with high strength grout. Four towers on the template were used to position the pin piles to the client’s specifications – precisely to 0.5 degrees. The template is lifted overboard and positioned onto the seabed where it is leveled using cylinders. One after the other, the piles are upended then lifted over the side of the vessel and guided into the template. “Then hammering the piles into the seabed took place but only after the underwater noise mitigation measures were in place!”
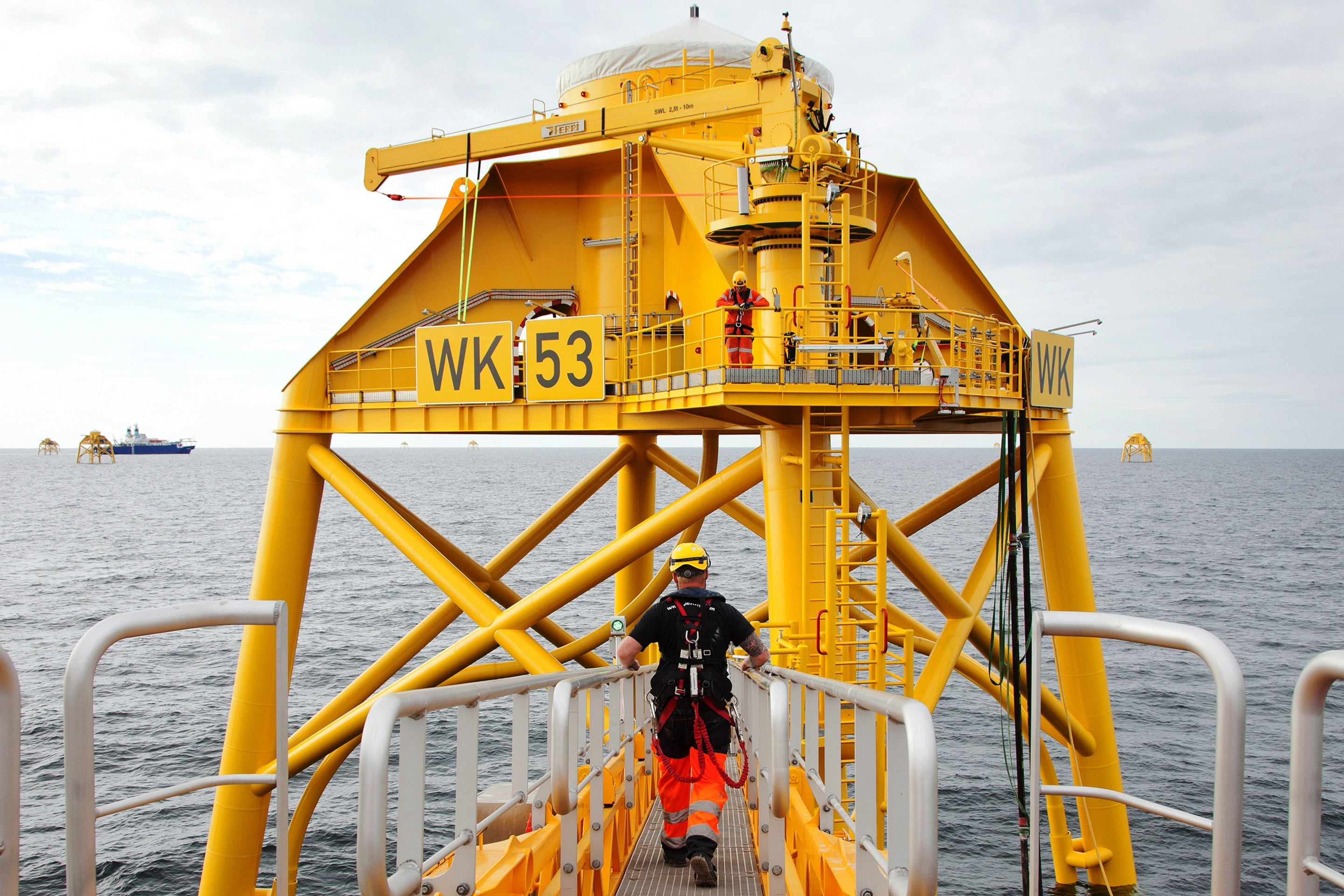
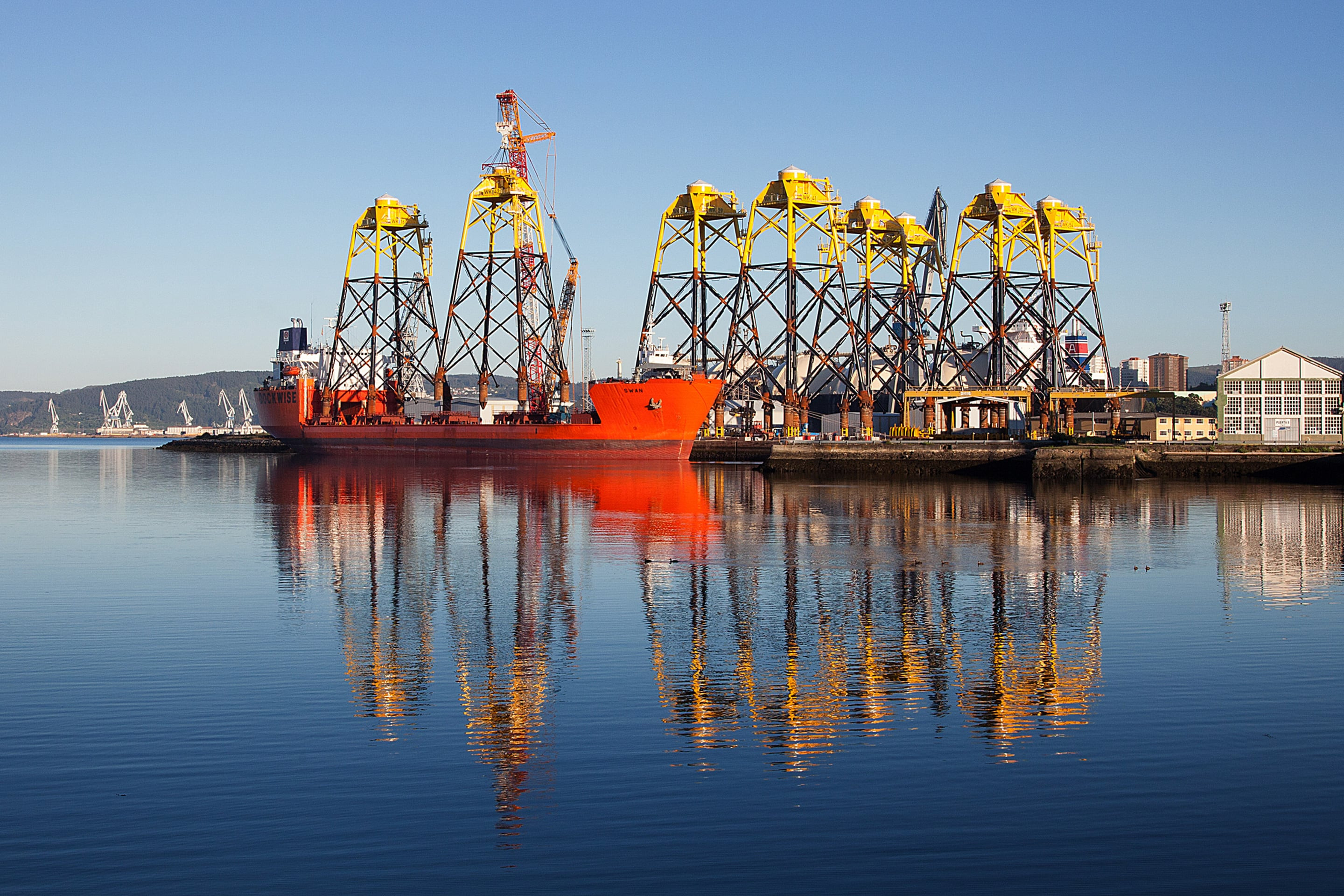
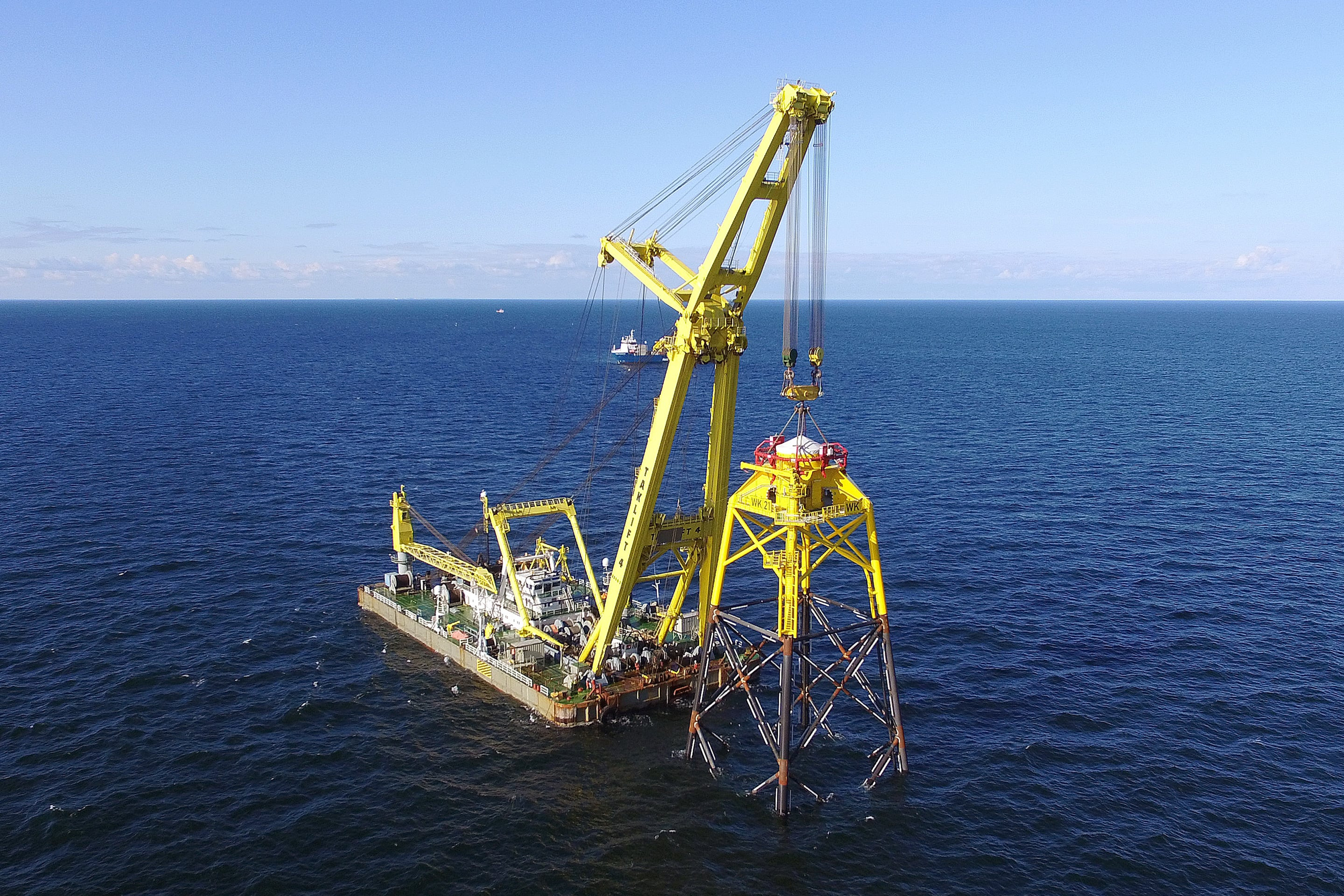
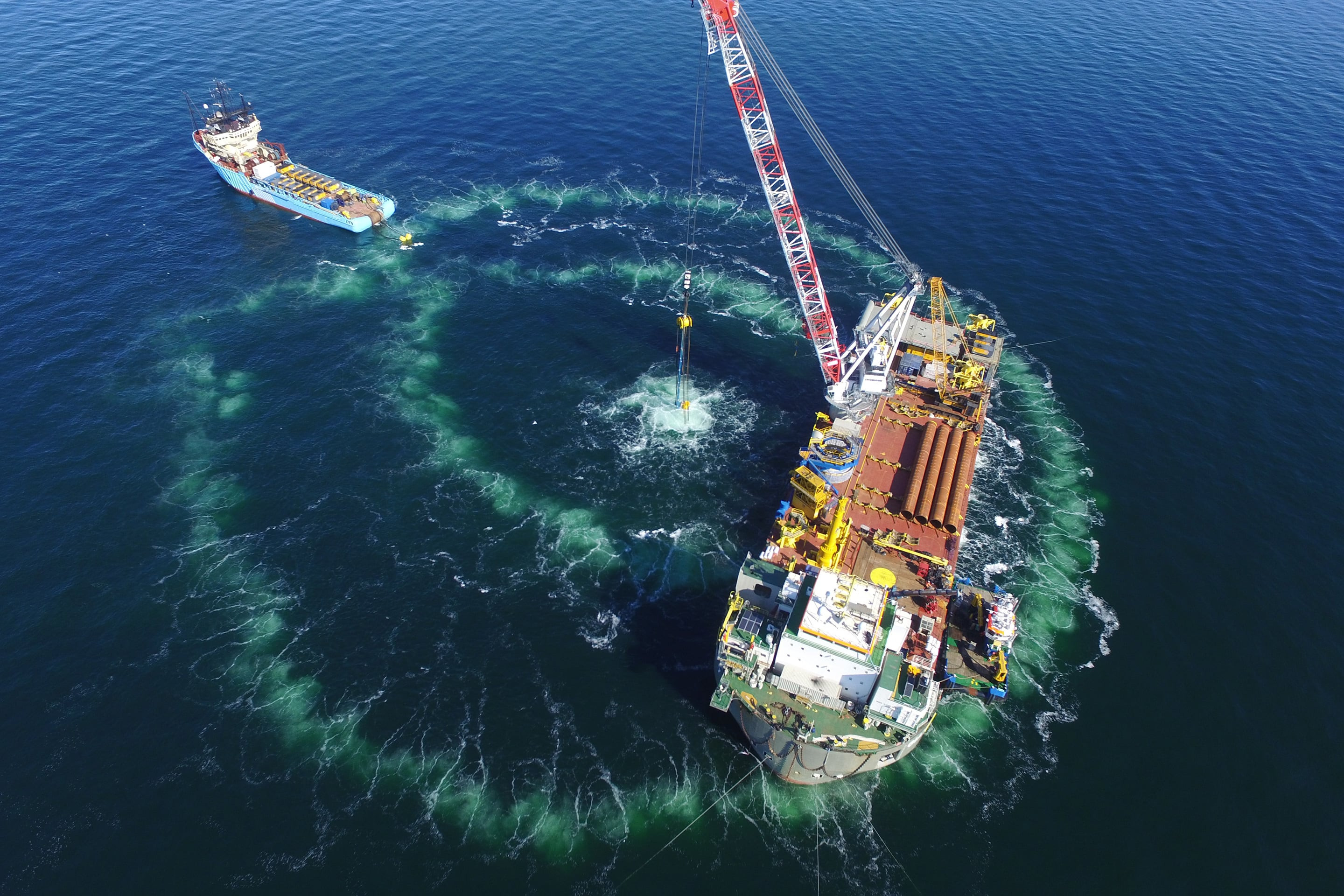
Stringent noise mitigation requirements
Alongside logistics, underwater noise mitigation was the other major challenge of this project. Protective measures were necessary to avoid harming rare species such as the harbor porpoise. Noise levels were capped at 160 decibels at 750 meters from the actual location where the piling took place. Rob outlines the many steps that Boskalis had put into place. “Firstly, we deployed a double Big Bubble Curtain from a platform supplier, which was fully loaded with compressors that blew air into submerged tubes.”
“However, this was not enough and we therefore took three additional measures. Apart from deploying acoustic deterrent devices, the barge was equipped with a hydro sound damper. In addition, a double layer of hoses expelling air was installed around the towers. With these measures we performed the project well within the noise limits.”
Record-breaking Veja Mate an extraordinary project in every sense
“The Veja Mate offshore wind farm was a massive project in every sense and one which has entered the record books,” says Taco Terpstra, Senior Project Manager at Boskalis, who was the project’s deputy director. Located in the German section of the North Sea, 130 kilometers north of Eemshaven, Veja Mate will have a capacity of 400MW. Work scope included the design, procurement, manufacture, transport and installation (including scour protection) of the foundations – consisting of enormous monopiles and transition pieces – for 67 wind turbines.
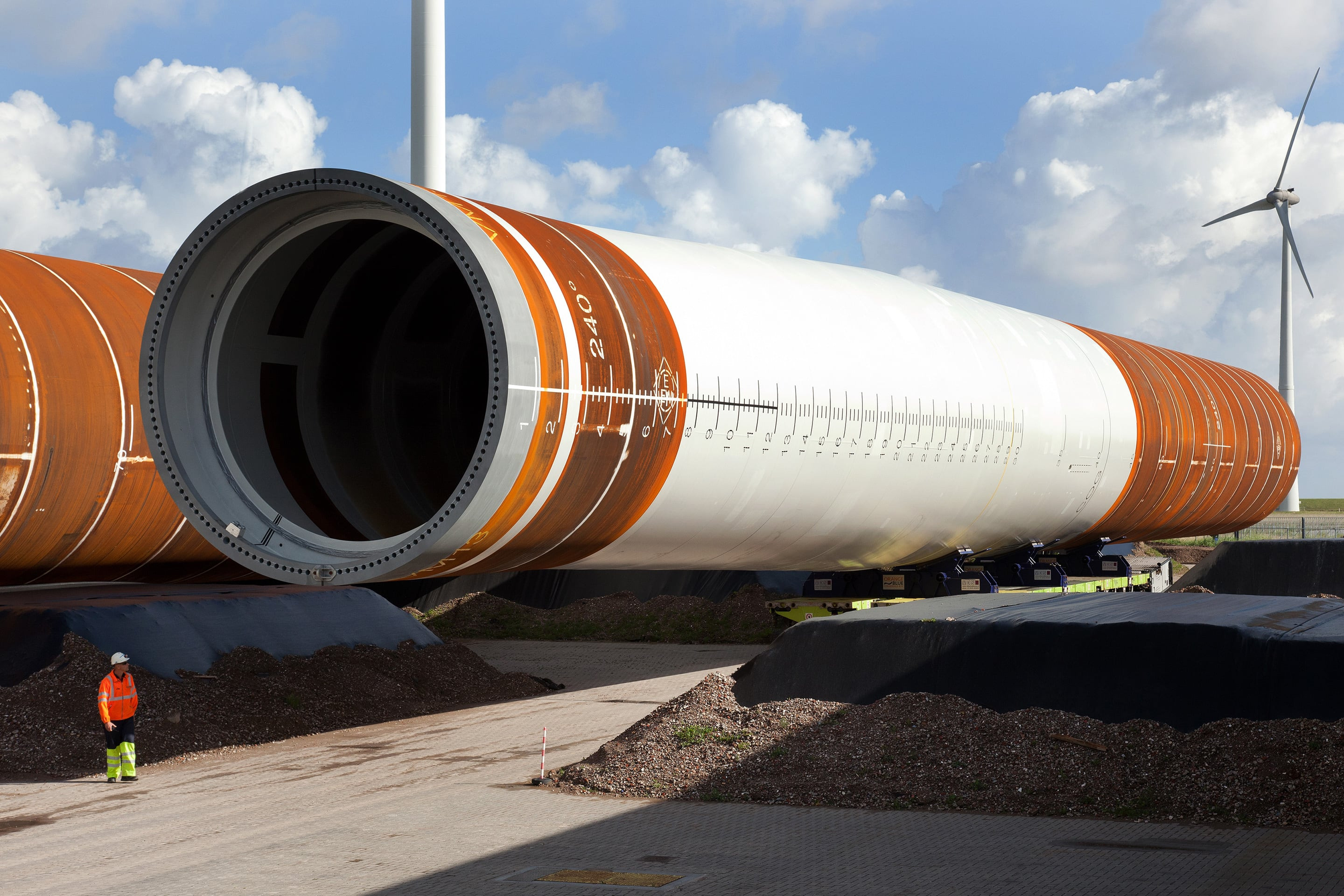
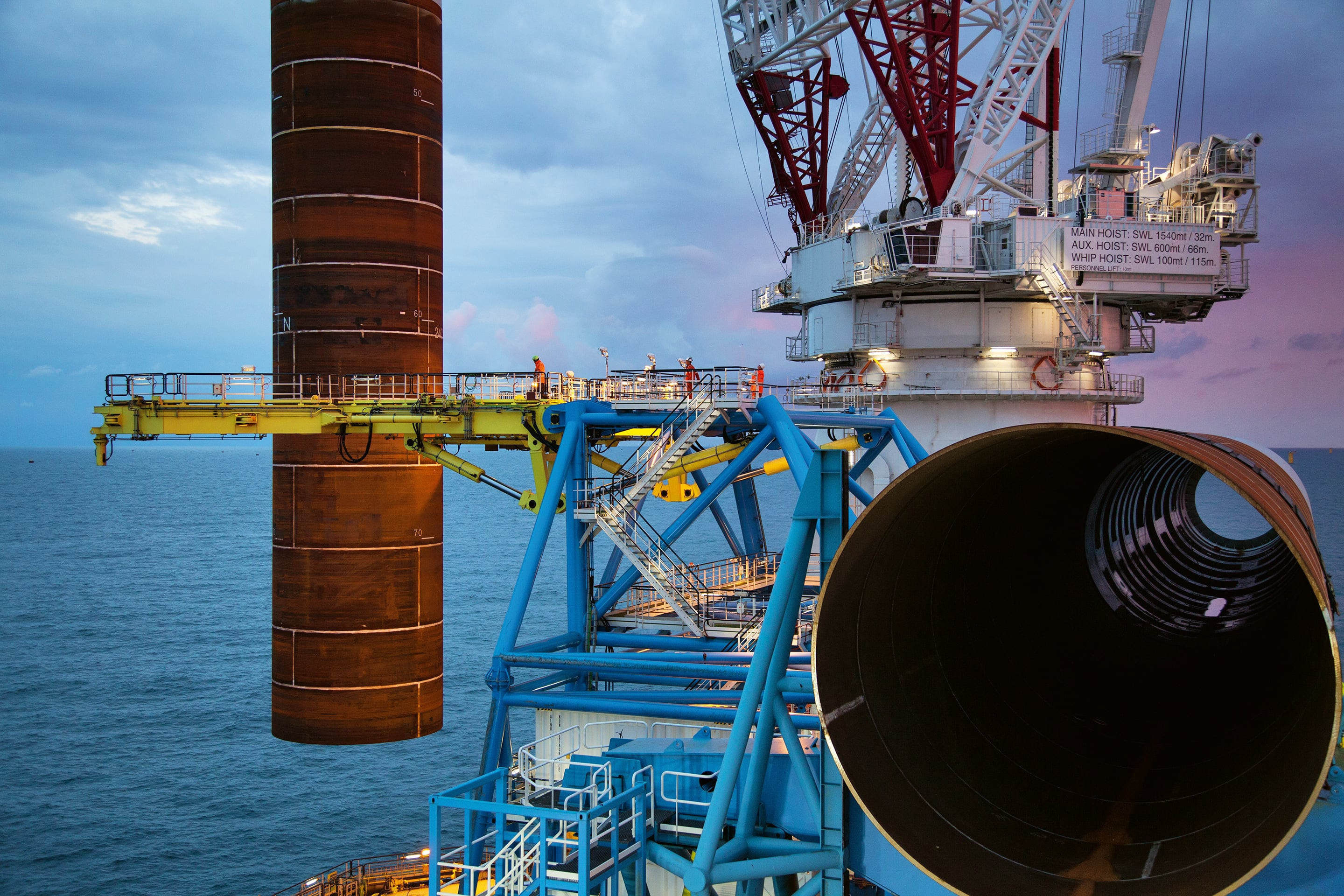
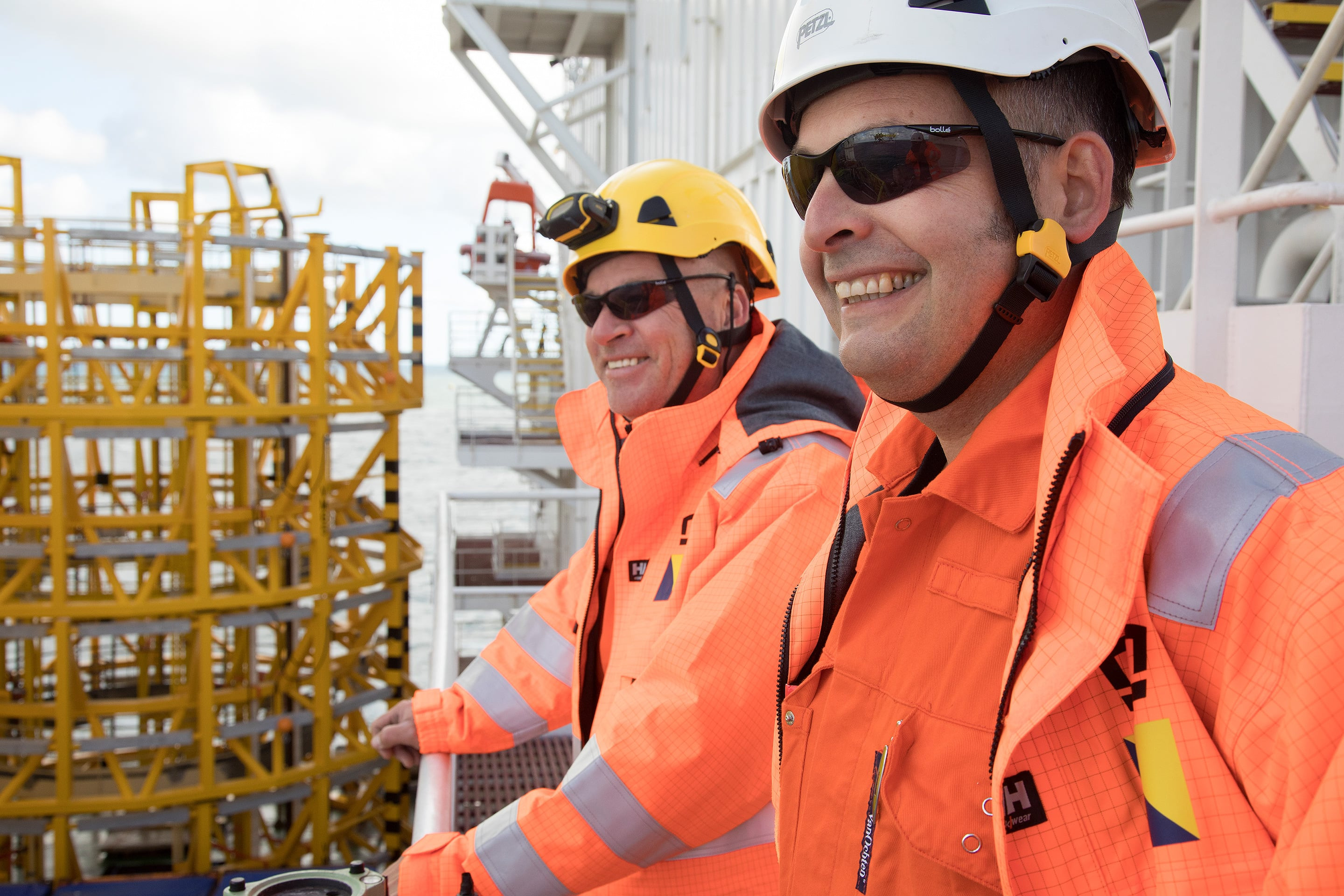
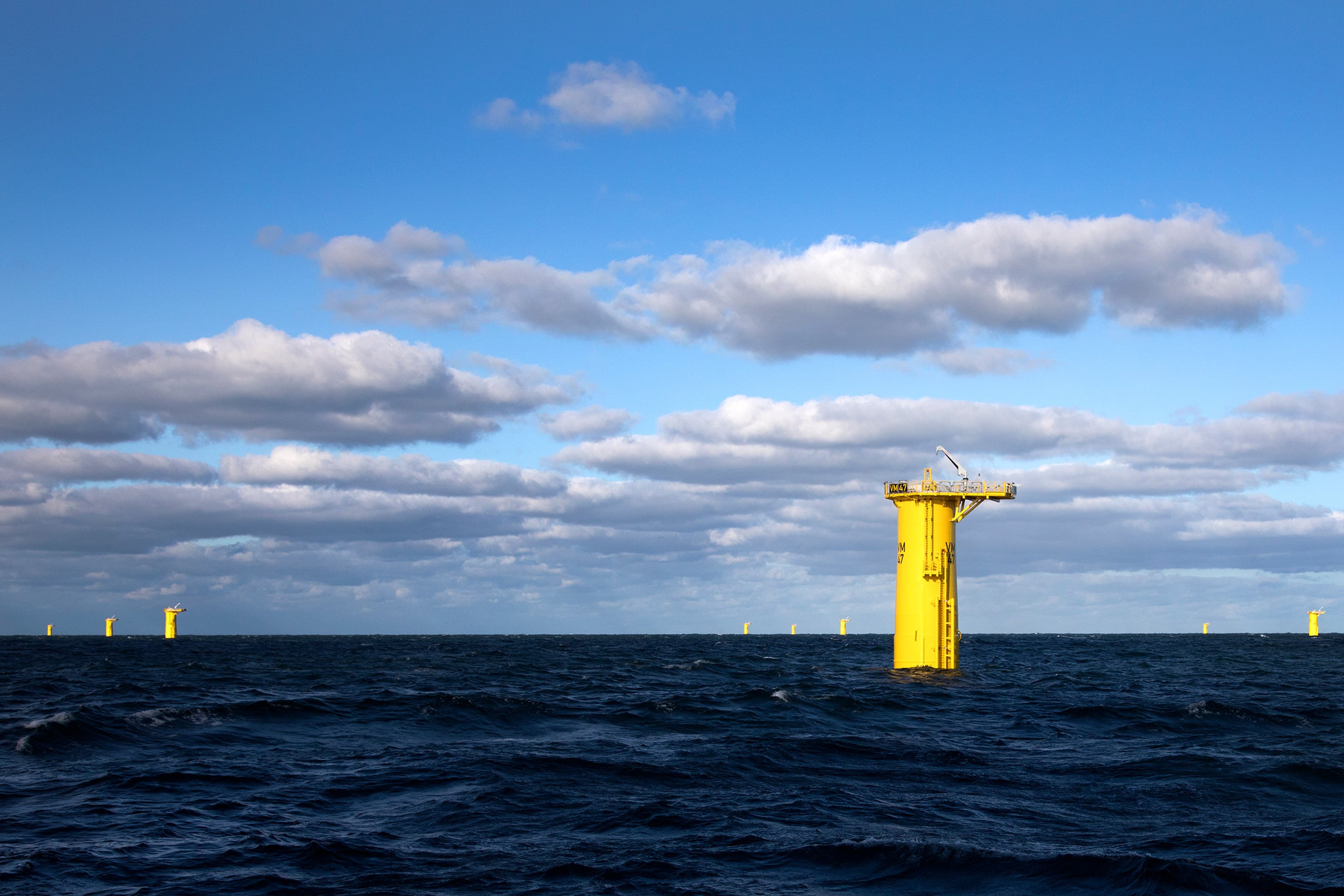
Taco enthuses: “We broke all sorts of records with this project which was executed on the basis of an Engineering, Procurement, Construction and Installation (EPCI) contract. For example, we used the largest-ever hydrohammer and the world’s largest jack-up vessel, which was fitted with a 1,500-ton crane. We also built and installed the largest monopiles in history, for which 110,000 tons of steel had to be produced within a year.”
The monopiles on the Veja Mate project are exceptional – they have a diameter of almost eight meters, are up to 85 meters in length and weigh 1,300 tons.
XXL 1,300-ton monopiles
The XXL monopiles are exceptional – they have a diameter of almost eight meters, are up to 85 meters in length and weigh 1,300 tons. They were built in Rostock in Germany and then transported to Eemshaven. Approximately ten monopiles were produced a month, with the last ones delivered in June. Installation began in April. “For this operation, we chartered the new jack-up vessel Scylla fitted with a Boskalis pile gripper frame – a structure that was designed specifically for this project. The heavy crane on board the vessel used the pile gripper frame, which was attached to the side of the Scylla and was fitted with two large ring structures, to lift the monopile. The two rings close around the pile. Then the guides on the inside of the rings maneuver the monopile into the correct position and allow it to sink slowly to the seabed.” “The next step is to secure the pile in the seabed, which takes just a few blows of the enormous hydrohammer. The rings around the frame are then opened and the monopile is driven around 40 meters into the seabed.” It takes roughly two days to install a monopile. And just like the Wikinger project, every effort was made to minimize the sound of piling, which was limited to 160 decibels.
Seamless coordination
“But for sure one of the biggest challenges we faced was arranging the seamless coordination of the various production and transport processes.” The transition pieces have been built in Aalborg, Denmark, and installation with the jack-up vessel Zaratan started in June. The Scylla and the Zaratan were operating simultaneously, along with numerous other vessels that were required to transport the materials from Rostock, Aalborg and Eemshaven. “There were 55 colleagues working full-time on the project at HQ and at the production sites. But during the peak summer period, several hundred people were working on this very special project!”
The client will be installing the tower sections with the turbine blades at the beginning of 2017 and the wind farm is expected to start generating electricity in the fall of 2017.
Boskalis specialists ensure wind farms are free of unexploded ordnance
Increasingly energy companies want to make sure there are no munitions where they are building wind farms. Boskalis Hirdes EOD Services provides advanced offshore solutions for finding and disposing of unexploded bombs and other ammunition. Frank Seubring, Operations Manager, outlines this specialist, and highly dangerous work.
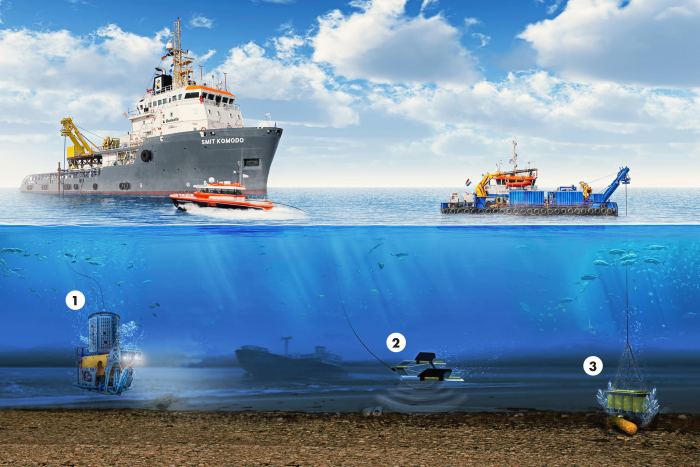
1 Heavy-Duty Work Class Remotely Operated Vehicle for locating and salvaging ammunition, 2 Tow-fish with gradiometer for locating ammunition, 3 Electromagnet for salvaging ammunition
Boskalis Hirdes, in addition to its dredging and civil engineering activities, has specialized in Explosive Ordnance Disposal (EOD) for more than 40 years. Although the company sometimes gets involved in disposing chemical weapons, its core business is finding and disposing of unexploded munitions, which are generally referred to as UXO: unexploded ordnance. Headquartered in Hamburg, the team is currently involved in projects in Indonesia, Denmark, United Kingdom, The Netherlands and Germany.
1.3 million tons of dumped munitions
Frank explains: “After the Second World War, large amounts of munitions were dumped at sea. In general, those munitions were not primed, so they were not as dangerous as duds – unexploded ordnance with all the safeties off. More than 1.3 million tons of conventional munitions were dumped in the North Sea. In addition, enormous numbers of English and German mines were laid in both the North Sea and the Baltic Sea. Munitions also end up on the seabed during military exercises.”
“When these munitions get dumped at sea, people think ‘tomorrow is another day’. But of course, the effect of seawater over the course of decades is unpredictable. That makes our work complex, but it is also precisely why our role is so vital. We sometimes find shells that can explode as soon as they come into contact with air. This means lives really are at risk.”
Detective work
The EOD work can be summed up as the detection, identification, and disposal of ordnance. “A lot of the detective work starts in international archives, which is often where we find information about where the explosives are located.” While Frank admits that EOD work has an element of ‘boy’s own’ about it, being adventurous, exciting work he stresses that everyone is fully aware of just how dangerous it is and the responsibility involved.
Detecting and disposing of munitions at sea means using high-tech equipment, some of which was developed in-house by Boskalis. This is so accurate it can easily detect a bottle top very deep on the seabed. In many cases, the seabed is mapped out using magnetometers installed on small ships working in shallow waters. The magnetometers can also be used in combination with Remotely Operated Vehicles (ROVs). “This is a reliable, but expensive, approach because it requires vessels with dynamic positioning. Additionally, in water down to depths of 100 meters, we often deploy Remotely Operated Towed Vehicles — ROVs that are towed over the seabed behind a ship.” And in shallower waters, the company also uses gradiometers: precise measuring instruments in an arrow-shaped structure that are towed by survey boats. “One of our latest detection methods uses the Autonomous Underwater Vehicle: a sort of robot fish that scans the seabed autonomously using sonar technology. Anything it finds is literally mapped out using special software.”
10,000 hits
“In any given area, we may have 10,000 hits, but we can’t always see the difference between a gas bottle and a bomb dropped by a plane. So the next phase involves identifying the finds. That work used to be done by divers but ROVs are much safer and quicker and can be used in waterdepths ranging from 3,000 to only 4 meters. Frequently, we are able to identify bombs in zero-visibility conditions using acoustic camera systems.”
Safe disposal
Once identified, the next question is: can the ordnance be moved safely? “Duds mustn’t be moved; they have to be rendered harmless on location. We detonate them using a method we developed in part ourselves.” A Cobra-type explosive is put into place immediately alongside the dud using an ROV. The Cobra attaches itself to the dud using a built-in nail pistol. The Boskalis experts then set off the Cobra from a safe distance, rendering the dud harmless.
Relative non-hazardous ordnance is picked up using specially developed electromagnets or robotic arms (manipulators) on an ROV that can bring bombs weighing up to 300 kilograms to the surface. Subsea cranes are used for heavier ordnance. The munitions that are found are initially stored in a specially designed subsea basket that can easily be found again on the seabed using a transponder. In that way, the munitions can be brought on board at the last moment. This is one of the many procedures to ensure the safety of the crew. The munitions are then passed on to the relevant authorities for safe disposal.