As a main contractor, Boskalis subsidiary Dockwise executed six heavy transports for BP earlier this year. Dockwise engineers spent more than four years making preparations for these transports. Project manager Aart van den Hoonaard explains the many aspects of this major project.
BP is expanding its operations in the Clair oil field by installing two new platforms, which were built by Hyundai Heavy Industries (HHI) in Ulsan in South Korea. The site of the project, Clair Ridge, is in the Atlantic Ocean to the west of the Shetland Islands, an area where the weather conditions are challenging.
Dockwise deployed six vessels to transport the two topsides and various platform modules. “The first platform, the quarters and utilities, consisted of three modules that we transported in 2015. The operation involved the transport of one large module, an integrated deck, on the Black Marlin, as well as two smaller modules, the living quarters and the generator, on the Mighty Servant 3,” Aart explains. “In the spring of 2016 we transported the second topside, the drilling and production platform, comprising the derrick and a number of smaller modules, on four vessels: the Talisman, the Triumph, the Transshelf and the Mighty Servant 1. The vessels sailed around the Cape of Good Hope and took an average of 55 days to complete the journey.”
The operations were all completed without a hitch.
“Our engineers spent more than four years making preparations for these transports,” Aart continues. “What makes this contract so special is that we were working directly for BP, whereas we are usually involved as a sub-contractor in these types of projects. The teams of specialists from Dockwise started the preparations for loading the modules onto the vessels in South Korea in February. Thanks to the thorough preparations, all of the modules were loaded onto the four vessels within four weeks in March. In quick succession, the Talisman and the Triumph, followed by the Transshelf and Mighty Servant 1, set off for Scotland.”
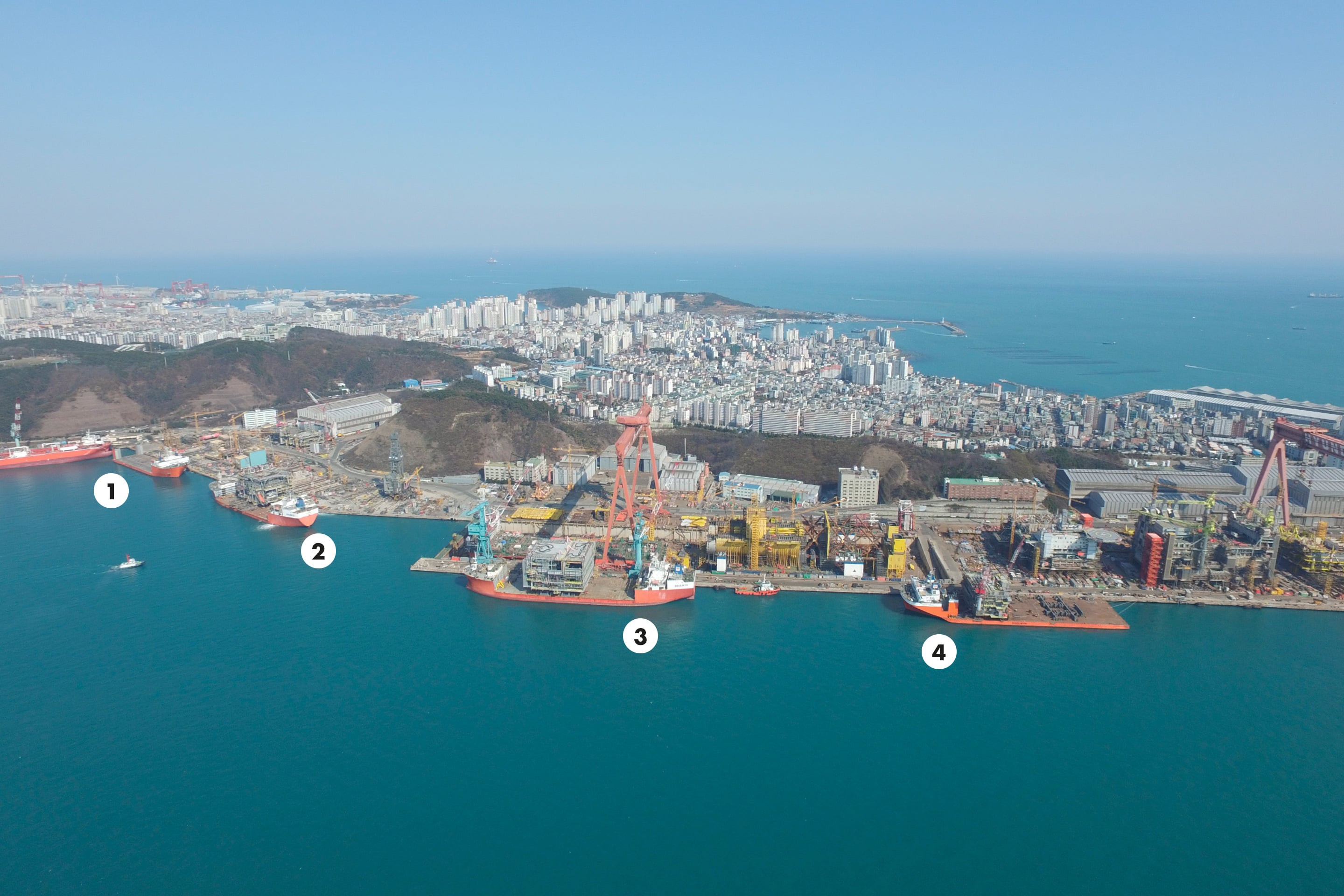
1 — 4,558 ton compression module and bridge on board Transshelf
2 — 9,092 ton drilling production module on board Triumph
3 — 8,630 ton drilling production module on board Talisman
4 — 3,296 ton derrick equipment and 4,225 ton drilling support module on board Mighty Servant I
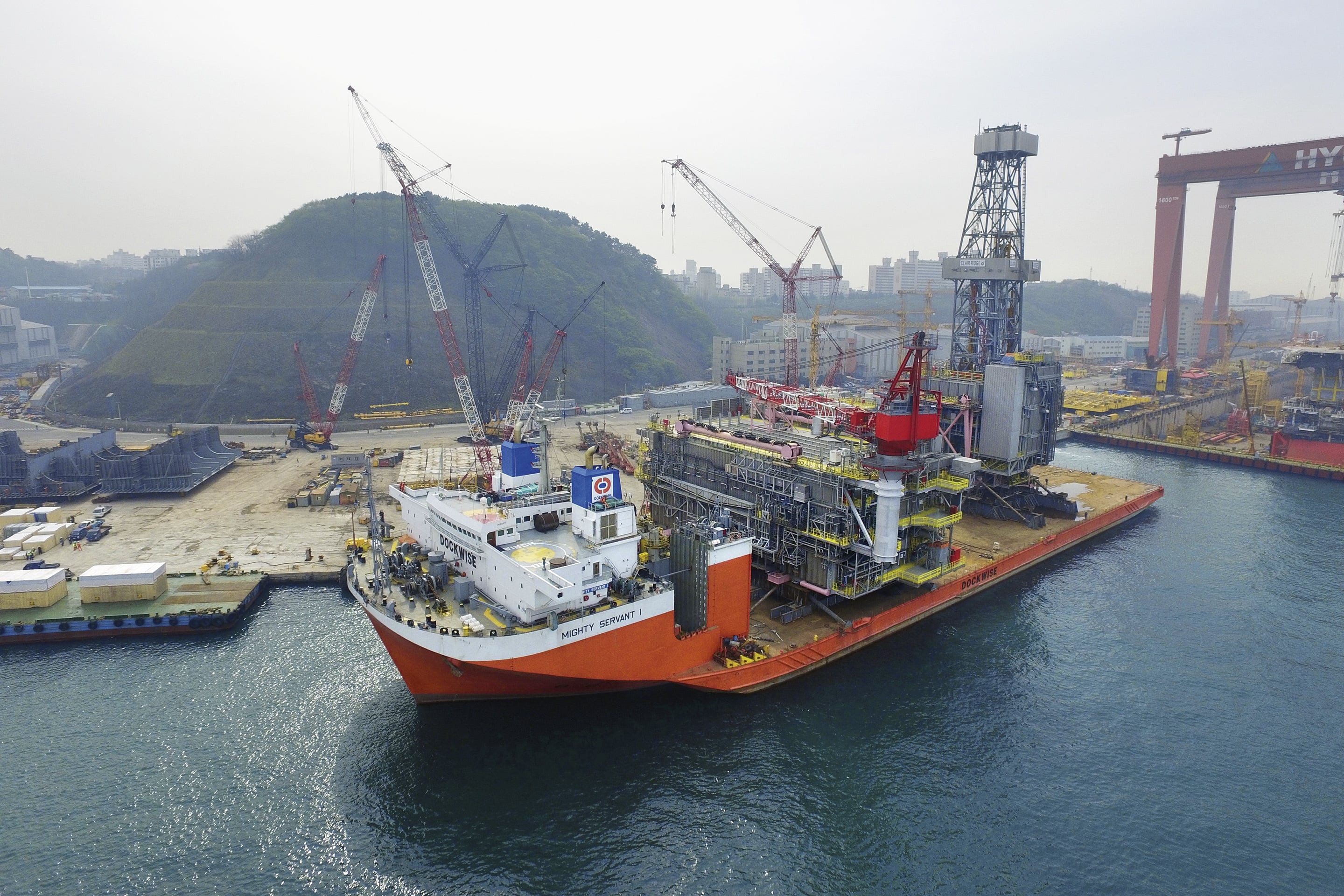
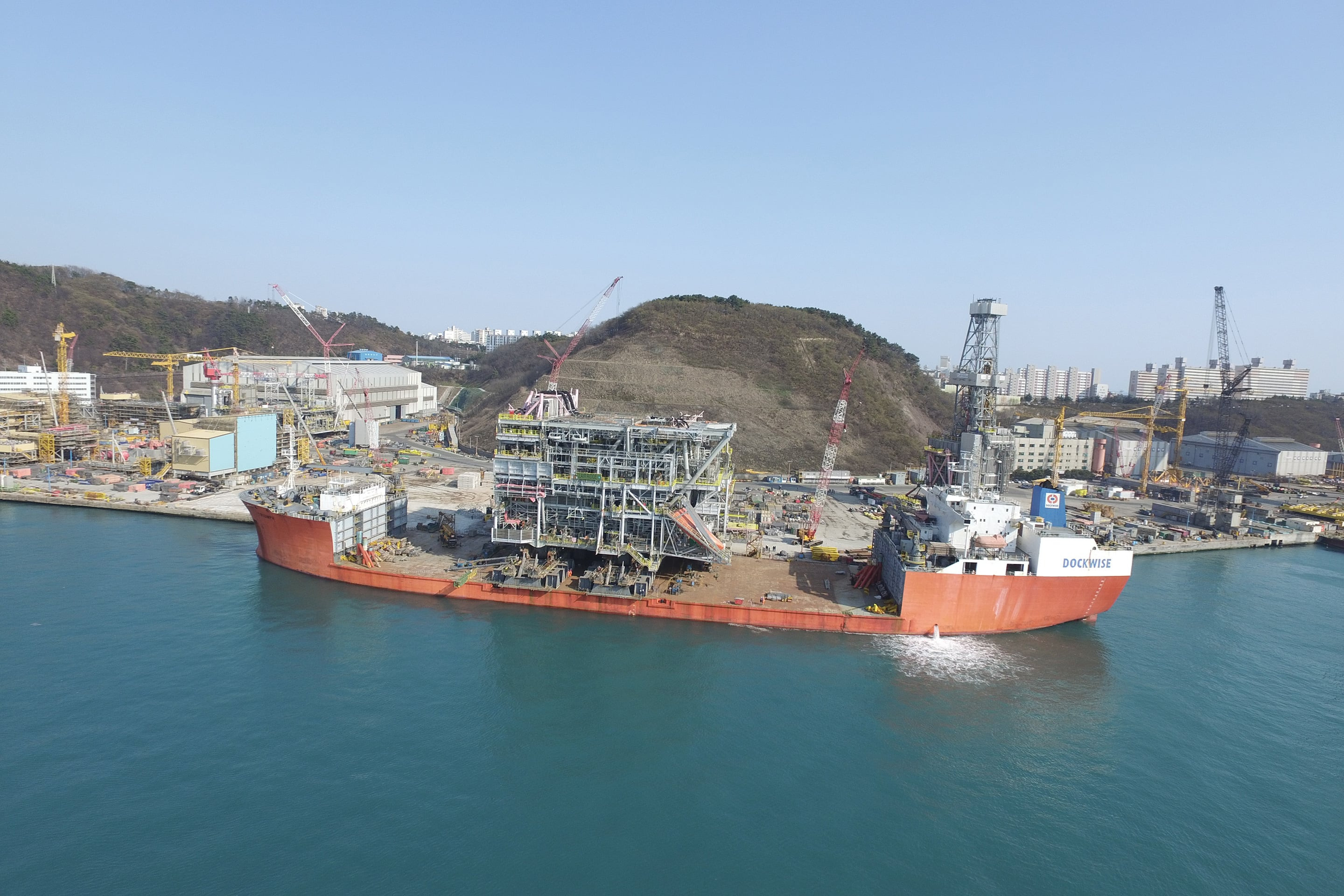
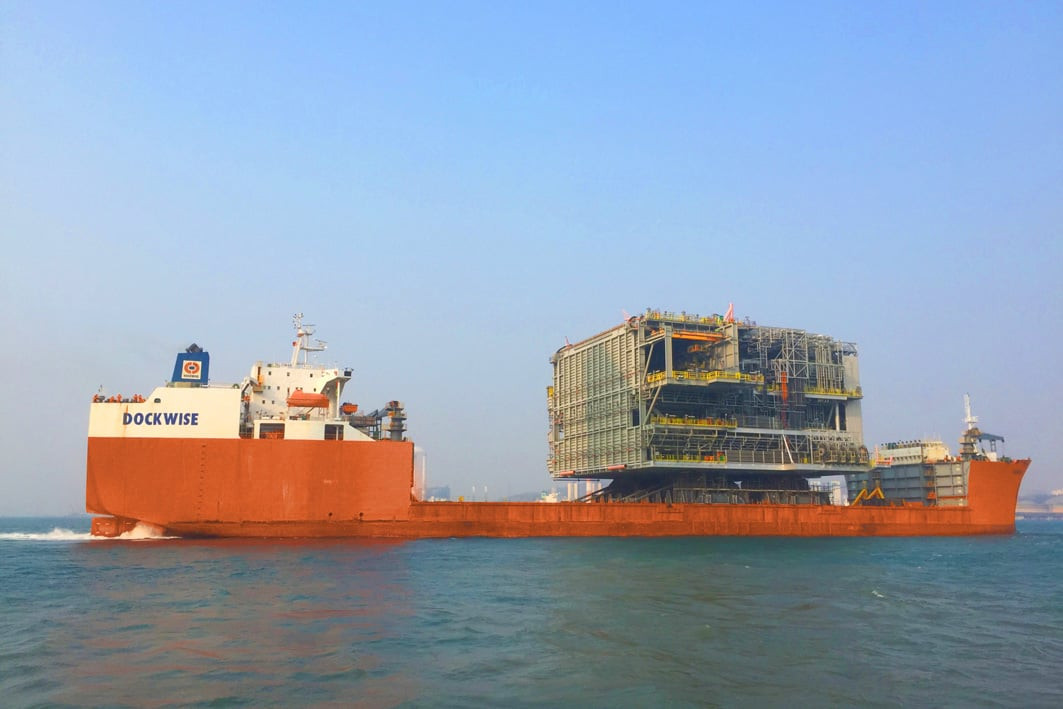
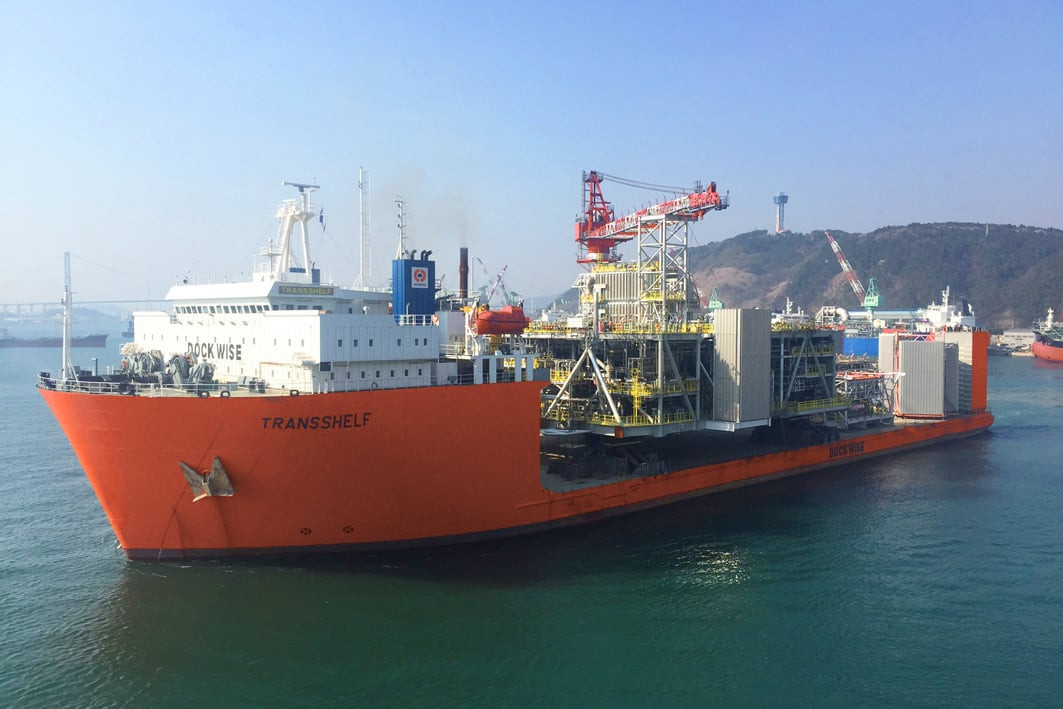
“The smaller modules were driven onto our vessels on trailers, but we had to load the heaviest modules using skidding operations,” says Aart. This procedure involves moving the vessels side-on to the quay and positioning them at precisely the right height through ballasting. The colossal installations are then pushed on board very slowly, centimeter by centimeter. “These operations take six to eight hours on average but they require a lot of preliminary engineering work. And they are generally very hectic operations,” he continues. “Despite the strict planning, the client or its subcontractors will still be working on the installation at the last moment. There is often some cleaning or painting to be done even when the installation has already been loaded onto our vessel. Properly coordinating all these last-minute activities, and above all guaranteeing safety, is a major task, but the operations were all completed without a hitch.”