This summer, Boskalis Marine Services was involved for the third consecutive year on installation work for the construction of the longest suspension bridge in the world: the Çanakkale 1915 bridge. A total of sixteen bridge segments were lifted and installed. The 5,000-ton sheerleg crane Asian Hercules III completed the final major lifting operation in early August. Project manager Jasper Joosse and operations manager Hans Hilverda look back on a successful project: “We will certainly drive across the bridge ourselves one day!”
On both banks, there are two pylons rising 318 meters above the waterline that support the bridge construction. There are heavy cables attached to the top of the four pylons that span the entire length of the bridge. They carry the vertical cables that bear the weight of the road surface and keep it horizontal. There will be three lanes in either direction on the 36-meter-wide bridge deck. Boskalis Marine Services had already played a leading role in the construction in previous years, for example in lifting segments of the pylons with its floating sheerleg crane Taklift 4 and in towing and positioning the caissons supporting the pylons.
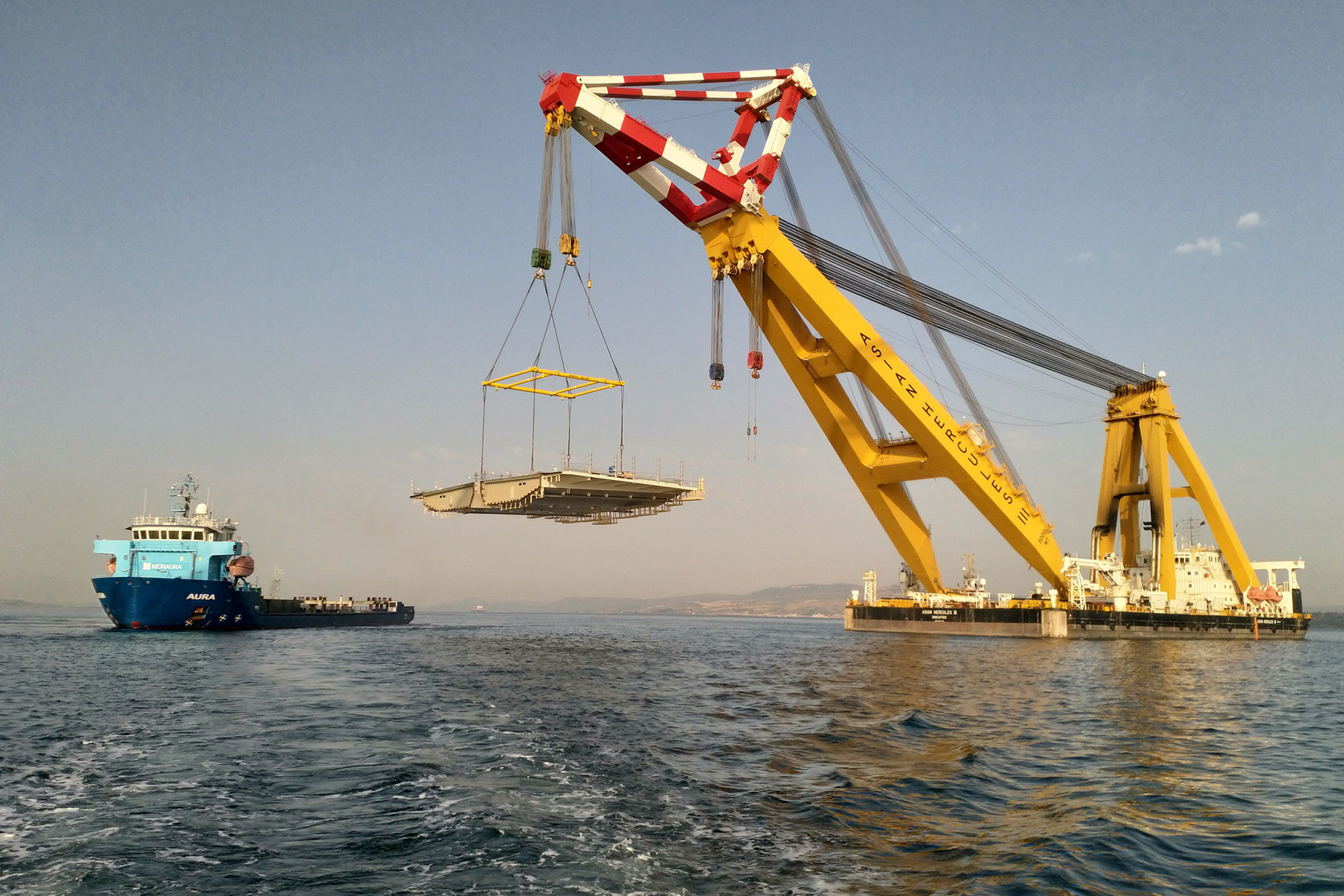
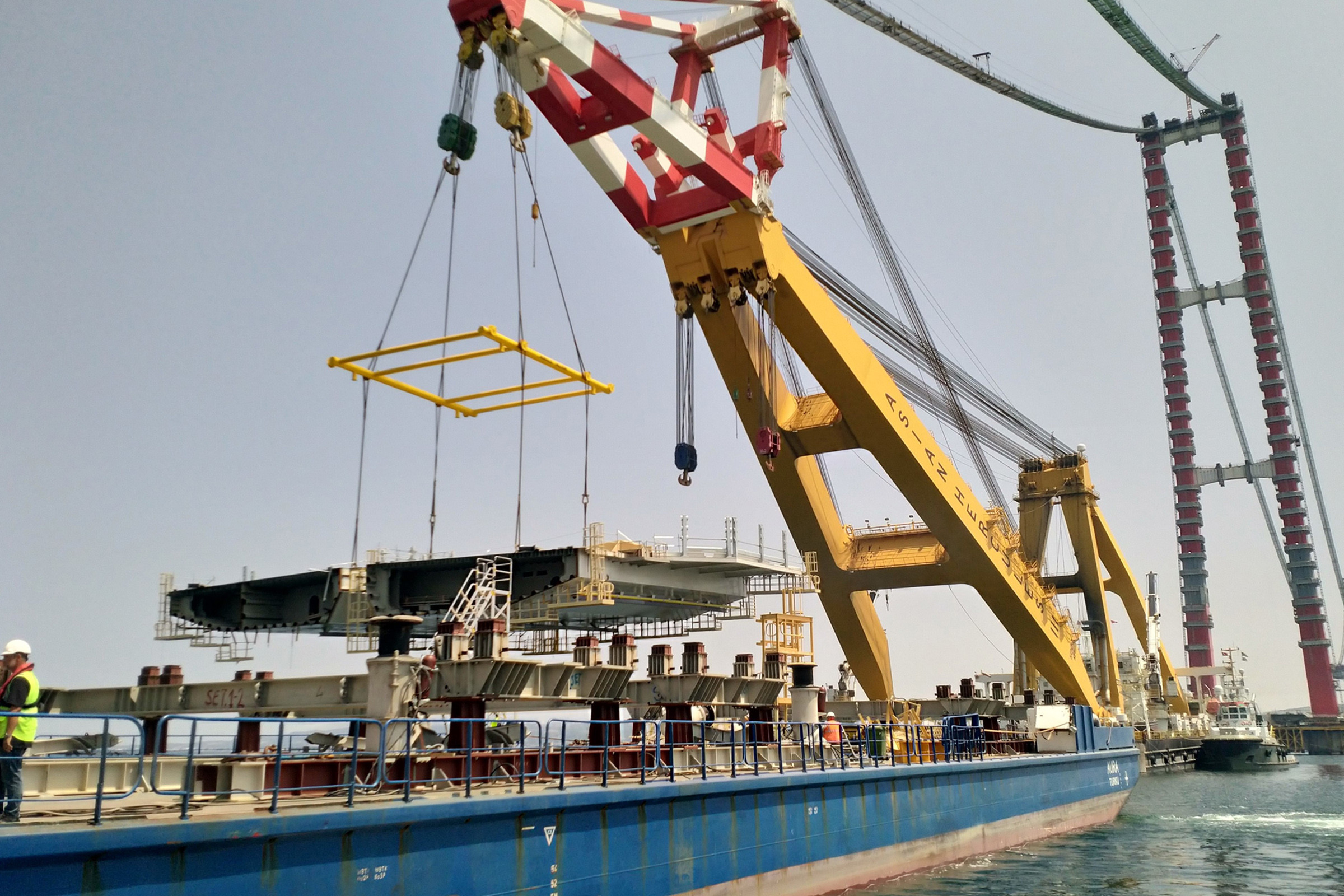
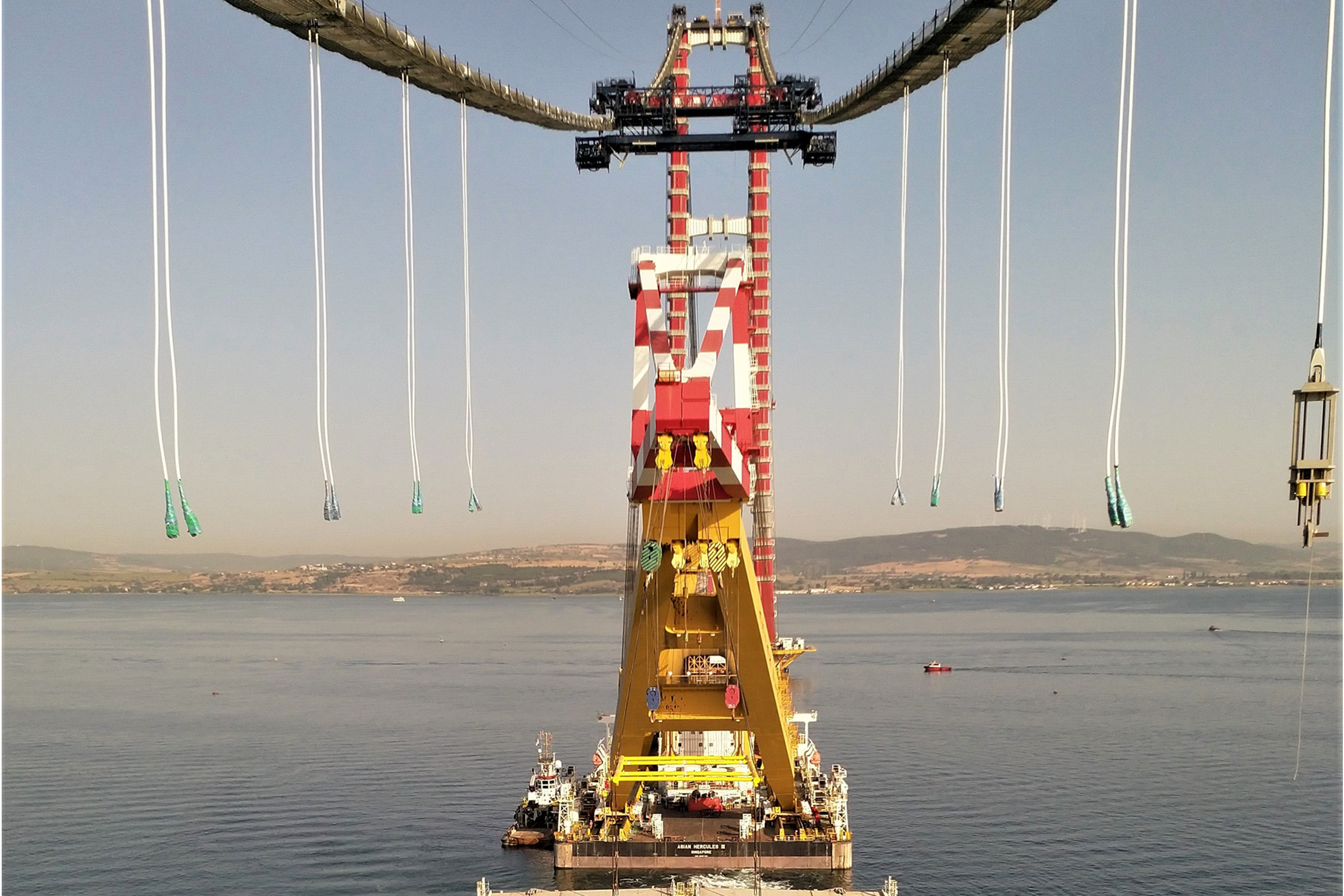
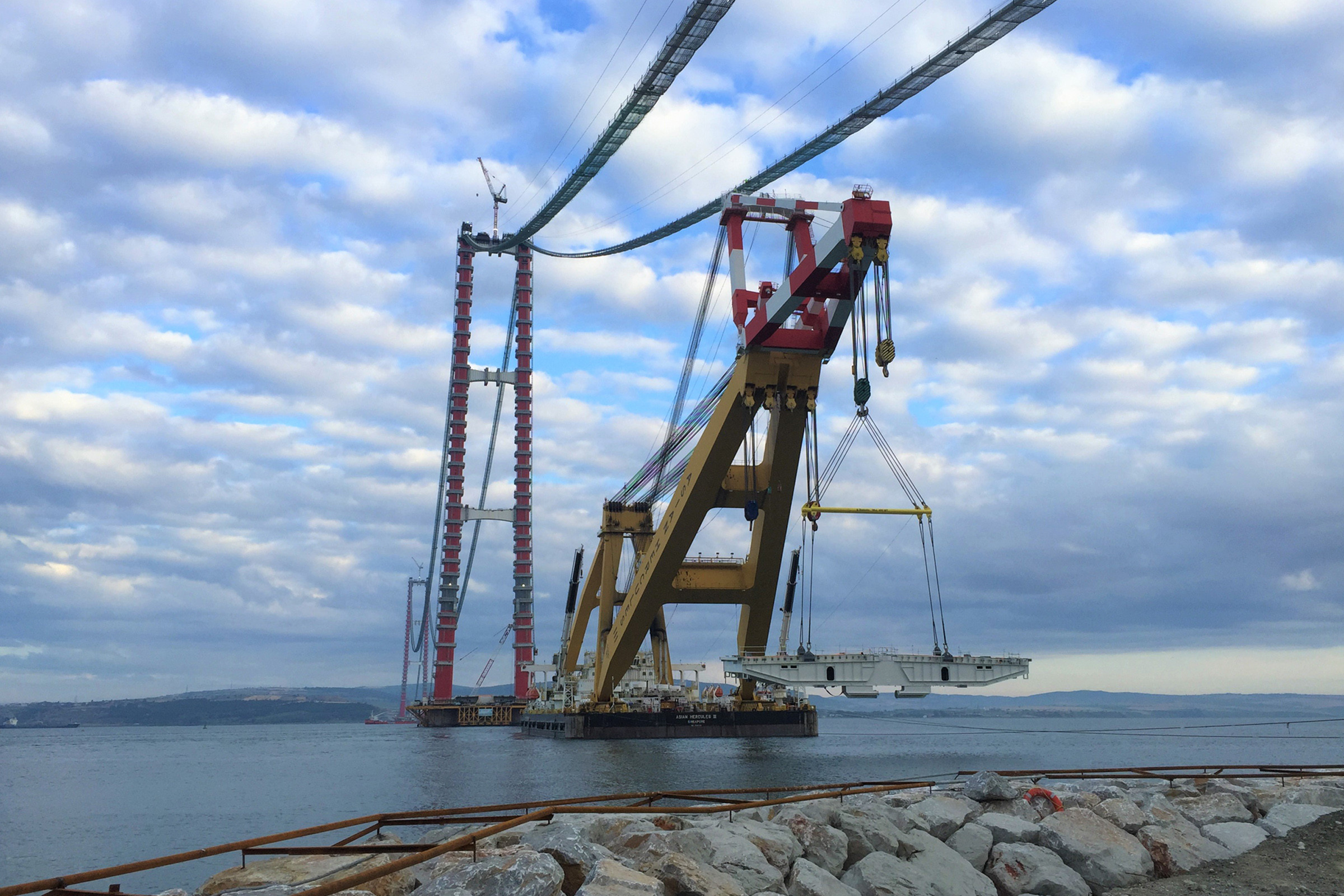
Confidence
“One of our strengths is that we are used to working in multinational teams with people from different cultural backgrounds. And that was sometimes useful on this project,” says Hilverda. “Once again, we were working for our client DLSY, a consortium consisting of the Turkish companies Limak and Yapı Merkezi and the South Korean companies Daelim and SK E&C. The challenge for our predominantly Dutch colleagues is to establish good relationships with those different corporate cultures and a range of safety philosophies. Guided by our NINA (No Injuries No Accidents) safety approach we managed to get the work done safely together with all people involved. When we acquired the contract, we agreed to work with the colleagues who had worked here before. The fact that we have been asked back for the third time is a vote of confidence, and we have justified that confidence this time again.”
Range and height
The road surface structure consists of approximately ninety bridge sections. Most of them are being installed by the client itself, but sixteen bridge sections had to be installed in hard-to-reach locations around the towers and pylons on both banks. “We were called in to help with that work,” Joosse says. “With the Asian Hercules III (AH3) sheerleg crane of our heavy lift joint venture Asian Lift, one of the largest sheerlegs of its kind, we had enough reach to install these sections at the required height. The heaviest bridge section weighed about 450 tons. A piece of cake for the AH3, which has a lifting capacity of 5,000 tons.” Hilverda explains: ‘The Çanakkale bridge’s road surface is approximately seventy to ninety meters above the waterline so that even high transport vessels can continue to use this important maritime route. The AH3 is one of the few floating sheerleg cranes in the world that can install the bridge sections at this height.”
Lifting frames
Several factors, including COVID-19, meant that the starting date for the physical lifting operation was postponed from late April to early June. “From that point on, we were able to stick more or less to schedule,” says Joosse. “But the preparatory work started back in September 2020 with the engineering and preparations for the entire operation: writing procedures, purchasing materials and applying for permits.” An important part of the preparations included the development and production of the steel lifting frames measuring 16x16 meters and 20x8 meters. They were designed specifically for this project. “The frames were needed to distribute the load evenly across all the lifting points of the segments,” says Hilverda. “They were built in Turkey on the basis of our design and tested by a local classification company.”
Daylight
Including the crews, about fifty Boskalis specialists were involved in the project, which was managed from a project office in Gelibolu. “You need daylight for this kind of work. So we worked twelve hours a day, seven days a week,” says Joosse. “In that way, we could adapt our work to match the rate at which the client could deliver the bridge sections.” Before each lifting operation, an extensive procedure was drawn up with a meticulous step-by-step plan. In the days before a lifting operation, all the steps were run through and numerous safety checks were carried out. “The AH3 was fixed into place with six anchors before each operation, so designing and testing a reliable anchor spread was a time-consuming part of the preparations,” says Joosse. “The colleagues on our anchor handling tug Sapphire did the anchoring work. Before each lifting operation, one half of the Dardanelles was closed to shipping by the authorities, so that any traffic was kept a few hundred meters away. A speed restriction of eight knots was also introduced for passing vessels.’
We provided the client with the best possible service
Pride
After the last lifting operation, the self-propelled AH3 returned to Singapore. “We provided the client with the best possible service by working in a solution-oriented way and getting involved with discussions about how to improve the operations,” says Hilverda. “Projects of this kind demonstrate that we are a highly versatile company and that Boskalis, as a one-stop shop, has almost every discipline at its disposal to execute projects like this in an integrated way, now and in the future.” Joosse agrees: “It’s a job we can be proud of. For Boskalis Marine Services, the project involved a whole range of interesting factors and we learned a lot. Hans and I will certainly drive across the bridge ourselves one day!”