A decade has passed since the Boskalis safety policy took shape as NINA: No Injuries, No Accidents. Our projects worldwide are now unthinkable without NINA on board. In this article we look back at the past ten years with colleagues who were present at NINA’s birth. “NINA has not only improved our safety awareness enormously, it has also had a positive impact on our corporate culture,” says Lodewijk Wijngaard, HR director of the Dredging & Inland Infra division.
Own standard
Was that the main reason for setting up a Safety working group?
Pim van der Knaap, group director of the Dredging division: “Our job was to standardize the safety policy. At the time, we had a range of clients who expected us to adapt to their safety programs. We worked on all sorts of projects around the world and so we were always dealing with multiple safety demands and challenges. As a result, our safety policy consisted of an enormous number of rules designed to meet those demands and challenges.”
As few rules as possible
How was the safety program established at the time?
Wijngaard: “We approached the subject of safety from the different perspectives of the individual business disciplines. The program was a result of extensive company-wide consultations: we talked to a lot of colleagues at the office and on the fleet, and we even consulted former colleagues. Ultimately, all those discussions led to the production of a bulky document about forty pages long. When we presented it to the colleagues, the fleet in particular said: Even more rules? But we’ve already got so many rules and regulations! So then we tried to boil that information down to a couple of pages. The outcome was the formulation of the Values & Rules.”
Bart Pröpper, project director at the Dredging division: “We quickly arrived at the conclusion that it was impossible to come up with the right rule for every specific situation. So we basically turned things around by emphasizing the values and basing them on as few rules as possible. That was an important component of the NINA approach and one that was very much appreciated throughout the organization.”
Van der Knaap: “We formulated five values in combination with just a handful of rules. We have had far-reaching discussions about this as senior management. It was important for the entire management to demonstrate their full commitment. So we recorded personal safety statements and put them online.”
‘NINA says no!’
How did the concept of ‘No Injuries, No Accidents’ originate?
Wijngaard: “We were convinced that some form of branding was needed to introduce the program successfully. Looking back, it was certainly a good idea from a psychological point of view to opt for the slogan ‘No Injuries, No Accidents’, with the letters forming a name. The fact that NINA was introduced as a female cartoon character helped to get it accepted. It wasn’t long before colleagues were making jokes about NINA says NO.”
Cultural transformation
What impact has NINA had on Boskalis?
Van der Knaap: “The program transformed the culture by making safety cool. That is an important change in our mentality as a company thanks to NINA.” Wijngaard: “You actually build up respect when you dare to discuss safety and show you are committed to the safety of your colleagues.” Van der Knaap: “The rapid drop in the number of incidents and accidents is not the only improvement to result from the program. Open discussions about safety have made the entire corporate culture a lot more open, which is a nice side-effect.” Pröpper: “You can see that safety awareness is an established value on the projects and the vessels. Our levels of safety have risen enormously thanks to NINA. We comply with client requirements but on the basis of our own system.”
Marinka Verhage, HR director of the Offshore Energy division: “NINA has also been a great success with colleagues from companies who joined us later such as SMIT and Dockwise. I think the “NINA moment” at the start of every work meeting played a major role here. It gives colleagues the opportunity to talk about not only safety aspects but also other topics. That openness has led to an enormous improvement in the team spirit on the fleet and at the office.” Wijngaard: “NINA has been a recurring theme in the various acquisitions in recent years. The discussions about it formed the basis for talking about how to align corporate cultures.”
Van der Knaap: “Following on from NINA, we now have toolboxes for tackling the risks during berthing vessels or the danger of tripping and falling. Thanks to NINA, everyone is aware of their own responsibility.”
Pröpper: “NINA has also improved the links between the office and the fleet. The lines have become shorter and people now understand each other’s situation much better. During NINA sessions, the crews of our vessels sometimes come up with initiatives or insights that are not expected by the office colleagues. NINA sessions mean that our employees get to know each other better and lower the different thresholds. Project managers also have more opportunities to explain why a certain approach has been chosen, for example because a client simply has certain requirements. When crews hear this, they understand more why a particular approach has been chosen and that motivates them.”
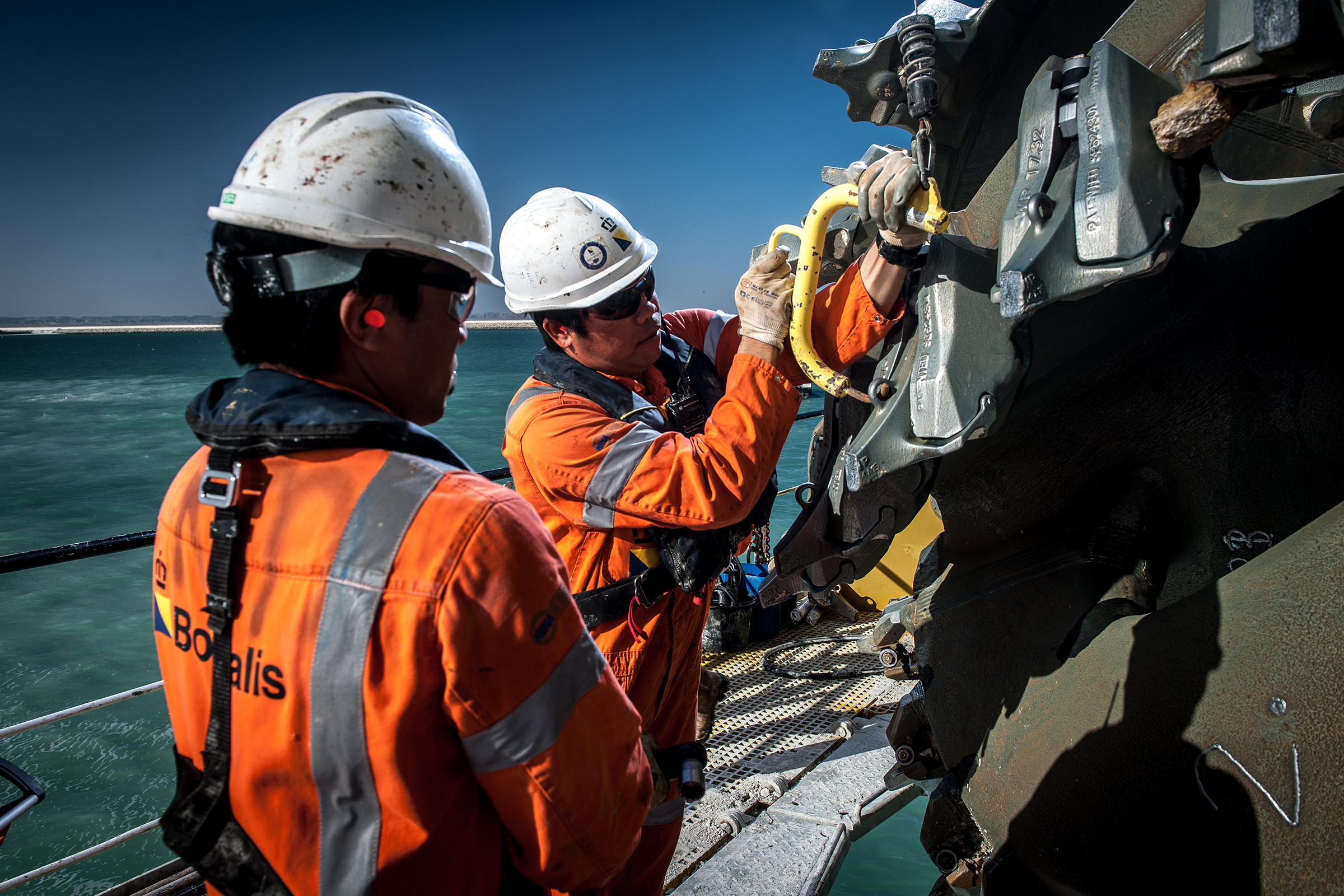
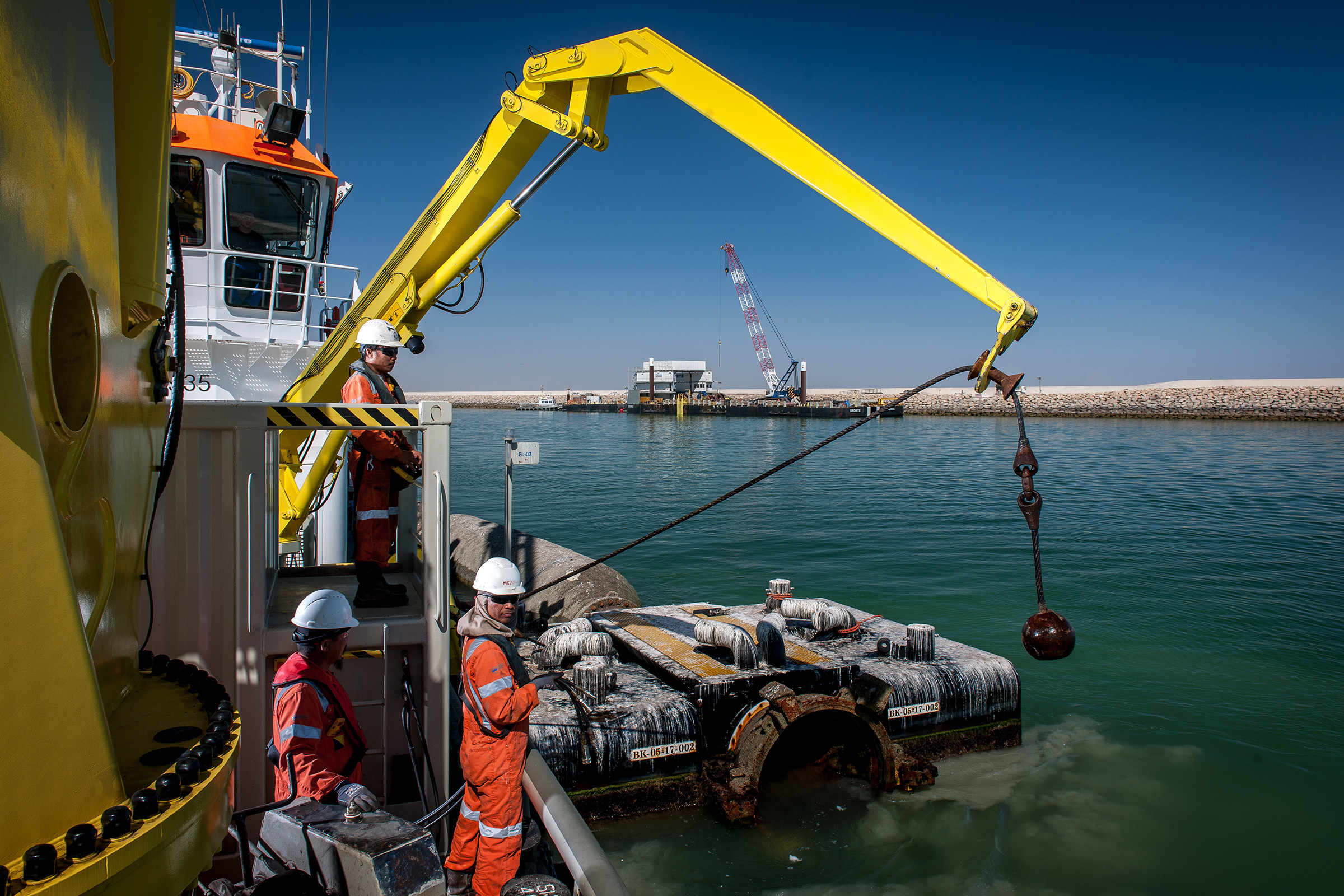
Shutting down work
Under NINA, any colleague can ask for a project, or a part of a project, to be suspended if he or she feels that a job is becoming too dangerous. Does that ever happen?
Pröpper: “It certainly does. Recently, we shut down a project for a while in response to the initiative of one of our crews. Of course, a decision like that has a significant impact, both financially and in terms of operational planning, but we always take safety seriously. These decisions are usually taken in consultation with the client; ultimately, it is also in the client’s interest for the work to be done safely.”
Passing on enthusiasm
How do you see the future for NINA?
Pröpper: “Safety awareness remains crucial on all our projects. I think it’s important to maintain our focus so that NINA continues to be a self-evident component of our corporate culture. In the future too, we will also be working on large numbers of projects with temporary employees who are not familiar with our safety culture; we have to tell them that safety is not negotiable.” Van der Knaap: “Thanks to NINA, our safety record has improved but highs can also be followed by lows. It’s vital to keep on looking for new inspiration to maintain the success of NINA and to continue passing on the enthusiasm we felt ten years ago.”
Standing still is not an option
As NINA Program Manager, Annette Panajoti is the point of contact for the whole of Boskalis. Talking about ‘Ten years of NINA’, she says: “NINA’s strength is that it is moving all the time with the organization. New business units embrace NINA as a safety philosophy and we, as Boskalis, have a single shared identity in the field of safety. In addition, it’s crucial to keep responding to the needs of colleagues on the projects and vessels, and to the trends in the accident rates. We do this, for example, by developing training courses and tools, such as the interactive Lifting & Hoisting Workbox and the in-depth Safety Leadership course. Due to the pandemic we are now hosting a lot of our training courses online, and the results are better than we could have hoped for. We have also rolled out a new e-learning method for subcontractors recently. This approach enables us to actively include our suppliers and subcontractors in our safety philosophy. We always look for ways to keep our approach effective and dynamic. Standing still is not an option.”