Pioneering Pile Reconditioning Cofferdam System invented by Boskalis manager receives top industry award for innovation.
Manager of the Ports and Downstream Department of Boskalis Subsea Services, Max Schellenbach, is a serial innovator. Here he talks about his recent invention, the Pile Reconditioning Cofferdam System (PRCS), which has already won the Dow Chemical Innovation Award.
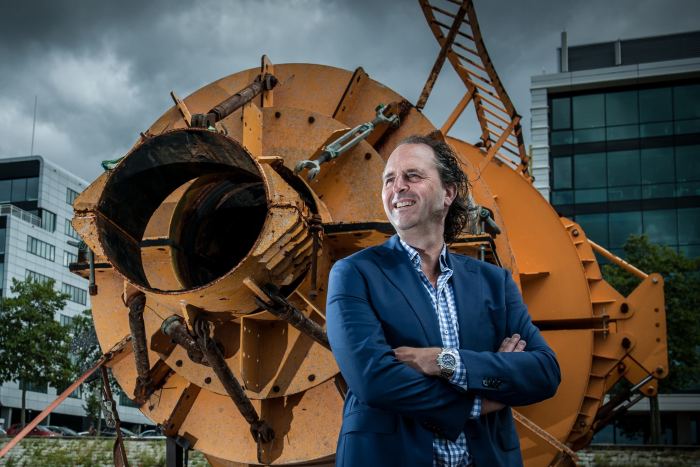
Max Schellenbach — Manager Ports and Downstream
Having been a professional diver Max, you appreciate the challenges and potential dangers of maintenance work on subsea structures. Did your work inspire you to create the PRCS?
“One of the great things about Boskalis is that innovative thinking really is encouraged here and my work is certainly one of my inspirations. The foundations of offshore installations, jetty structures and bridges usually consist of large steel piles that are mostly located below the waterline and, until now, divers have done the maintenance work required to tackle corrosion. This is a labor-intensive process and it isn’t always that safe or environmentally friendly. Therefore an alternative was needed.”
the robot removes rust and old layers of coating from the pile using hydro-jetting techniques involving pressures of up to 3,000 bars.
Inspection and maintenance work at a Dow Chemical site led to the initial idea, is that right?
“The direct reason for the development of the PRCS was to perform inspection and maintenance work on the foundations of a Dow Chemical installation in Terneuzen in the Netherlands. Our divers usually deployed high-pressure jets that deliver more than 250 bars to remove the layer — which can be more than 30 centimeters thick — of oysters, algae and vegetation, before inspecting the piles and doing any repair work. But given the health and safety risks, Dow Chemical refused to allow the work to be done in this way. I am a member of I-Tanks, a think-tank with representatives from the petrochemical and offshore industry. Following the situation at Dow Chemical we all got together to devise a totally new approach to maintenance, which resulted in the PRCS.”
The PRCS essentially consists of a range of ‘smart components’?
“We started by developing a remotely operated pile cleaning robot. This is a magnetic system that is installed in a ring around the pile. The robot is linked to an extensive, integrated control and monitoring system. It turns 360 degrees around the pile and first removes the accumulated shells and algae with hydro-jetting using a pressure of about 300 bars. In the next phase, the robot removes rust and old layers of coating from the pile using hydro-jetting techniques involving pressures of up to 3,000 bars. The robot can be moved up and down on piles with diameters of more than 150 centimeters and it can be used both above and below the waterline. In addition, it can be fitted out with an additional module: the Ultrasonic Mapping Scan Unit, which we developed in-house and which can measure the wall thickness of the pile and identify external damage. At that point, we can make any necessary repairs and apply new layers of paint and/or coating.”
It is vital that the operating method is not only fast, safe and efficient, but it is also sustainable.
Why is it actually called the Pile Reconditioning Cofferdam System?
“The fact that all this work can be done underwater is thanks to the invention that gave the system its name: the cofferdam. In simple terms, this is a seven-meter-tall cylinder that is installed around the pile in two parts like a floating sleeve before being sealed shut hydraulically. When the water is pumped out, you get a safe, watertight cylinder where people can work in dry conditions, whatever the weather.”
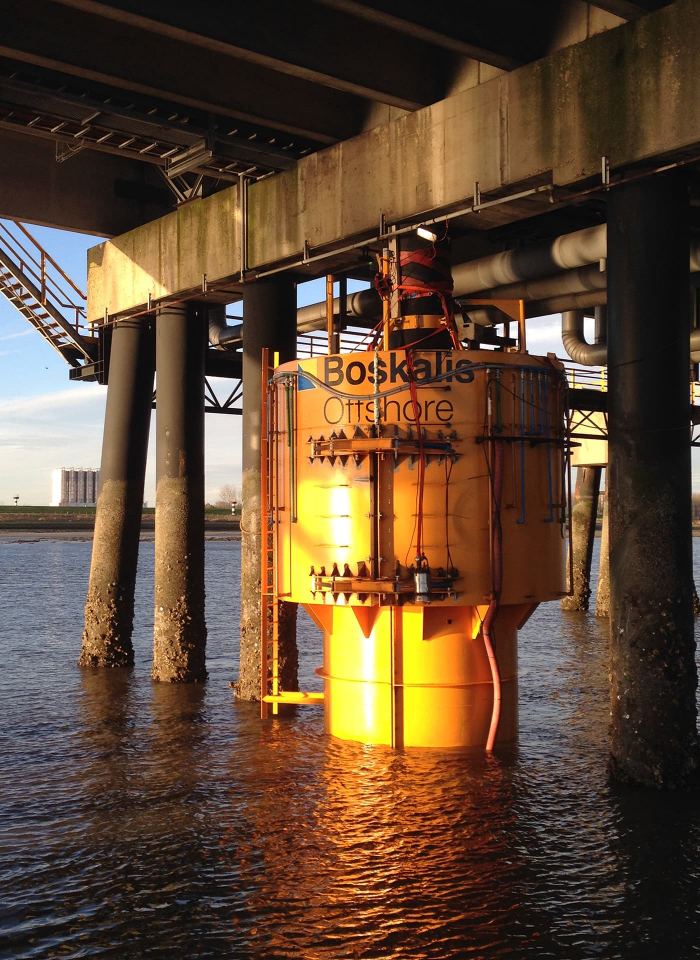
Pile Reconditioning Cofferdam System
But not everything can be carried out by the robot?
“No, although it is a very versatile system the robot can’t carry out the entire inspection and maintenance process. The inside has been fitted out with lifts so that two inspectors can operate safely and at the required height at the same time, doing the work that the robot can’t manage, such as repairs.”
As well as being safe and efficient it is important that the PCRS is also sustainable?
“It is vital that the operating method is not only fast, safe and efficient, but it is also sustainable. Dirty water and waste products such as paint and other chemicals are carefully collected in special reservoirs and taken to recycling stations.
What about cost savings?
“The savings are enormous. Depending on the size of the structure, a complete service for one pile can take two or three days. However, the work extends the useful life of a pile by dozens of years. This makes the system extremely interesting for our clients, and even more so because the PRCS doesn’t interfere with the regular work on jetties or offshore installations, such as loading and unloading operations.”
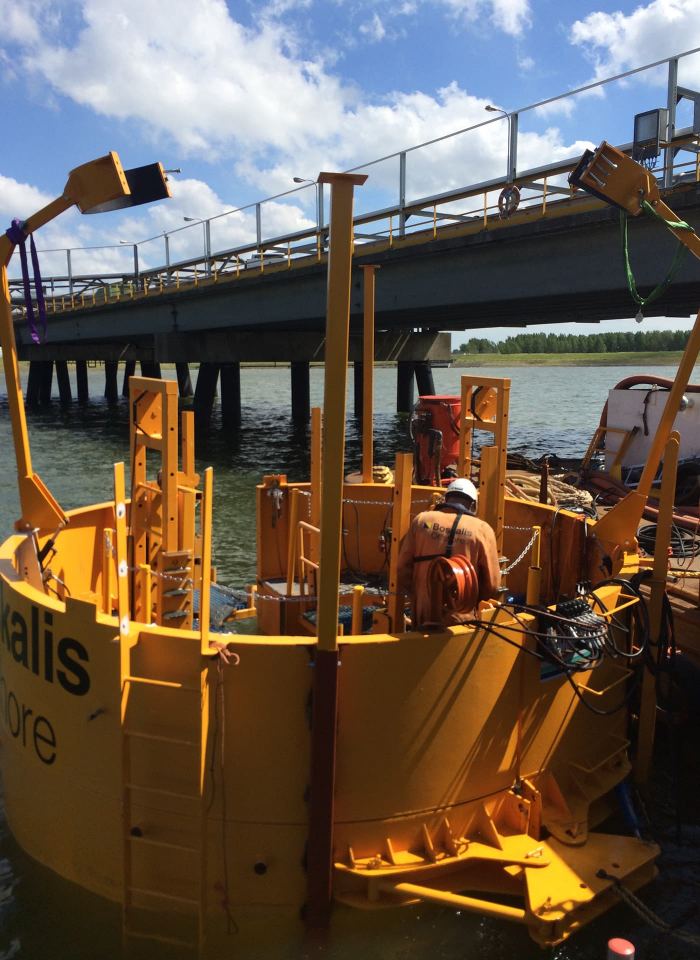
Pile Reconditioning Cofferdam System
What has been the market reaction to this innovation?
“There has been interest from throughout the world. I believe it has a big future and I am convinced that innovations like this help us to strengthen our leading position.”