Açu Port in Rio de Janeiro is the largest port-industry complex in Latin America. In close cooperation with the client, Boskalis faced technical and managerial challenges as a result of continuous design variations, the economic crisis and a very tight schedule.
Since 2011, Boskalis has been involved in the construction of the Açu Port, with terminals that will handle goods such as bauxite, ore, oil, general cargo and vehicles. Being on the doorstep of the Campos Basin, one of the most important oil and gas fields in Brazil, the port will also be a strategically important base for manufacturers and logistics operators involved in the offshore industry. As the project was completed in 2015 Boskalis Project Director, Louw Dekker and Regional Manager Brazil, Jord Veldman look back at the last few years.
What was the scope of the contract awarded by Prumo Logística S.A.?
Louw: “The dredging work included the construction of two huge access channels, a turning basin, an inner channel and mooring berths.” Jord: “Boskalis was also responsible for a range of activities in the contracted scope of works, such as project management, the organization and clearance of working sites, the construction of more than 13 kilometers of access roads, excavation, dredging and hydraulic reclamation, slope maintenance and the construction of the revetments for the breakwater.”
As soon as Boskalis started the project, there was a major challenge straightaway, is that right?
Jord: “We had to mobilize very fast, with work starting within a month. We were contracted at the end of July 2011 for the inner port. For the channel we had to dredge inwards by breaking in through the beach, and get the cutter suction dredger beyond the waterline before the start of the turtle egg-laying season on 1 October. The turtles had to be completely undisturbed until 1 April. This only gave us two months but coupled with this, the equipment was still abroad. The cutter suction dredger, Cyrus II, was undergoing repairs in Cadiz, Spain, which meant there was not enough time to sail to Brazil and to import the Cyrus II. Generally, it can take weeks to get a ship through the import procedures. So we came up with a solution of getting a Brazilian inspector to conduct the ‘pre-inspect’ of the Cyrus II in Cadiz, which saved an enormous amount of time as the vessel was ready for the Navy inspection upon arrival.”
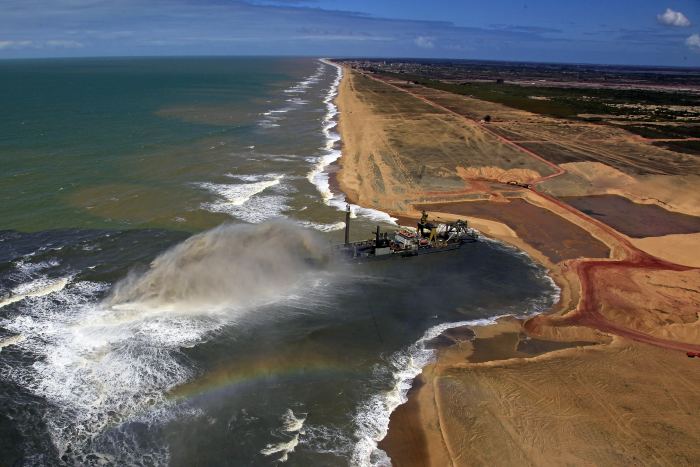
The break-in by cutter suction dredger Cyrus II on 27 September 2011
Did you manage to complete this initial stage on time?
Jord: “Despite the challenges, we actually broke through on 27 September. When we opened the channel on schedule it was a very special moment. This breakthrough was crucial to the project and was only possible because we had a very committed team, both at the onsite office in Açu, in Rio de Janeiro and at HQ in the Netherlands.”
The ongoing interaction with the client resulted in more efficiency and finding the best technical and cost-effective solutions.
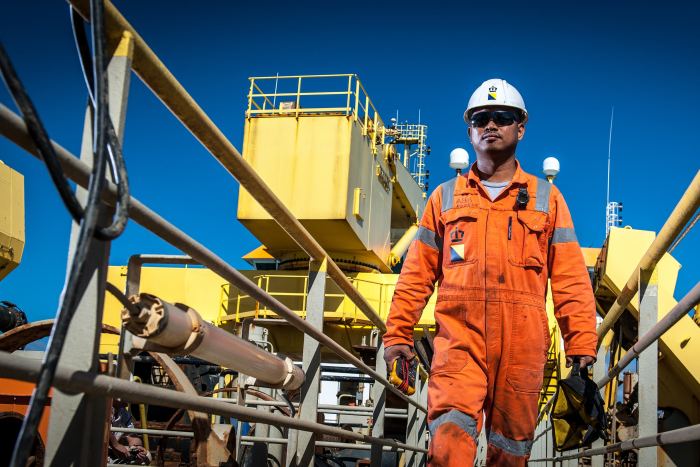
How did the project evolve after the initial stage?
Jord: “The nature and dimensions of the work, as well as the various technical details of this project, the client requirements, the range of stakeholders and the future concessionaires of the Port of Açu have resulted in several variations to the initial project design. The end-design was not really concluded until 2013. Boskalis was heavily involved in the process, helping our client as much as we could with the various changes. The initial contracted scope included a minimum volume of 43 million m3 of dredged material. This was already exceeded midway through the contract and Boskalis ultimately dredged a total of 49 million m3.”
Louw, what would you consider to have been the major challenges of this project?
Louw: “The very tight schedule was a major challenge, especially in light of the many design changes. The continuous variations sometimes affected the progress of the works but also represented an interesting technical and managerial challenge in a major hydraulic engineering project. The economy has also sometimes impacted the project and this led to the postponement of some phases. The ongoing interaction with the client resulted in more efficiency and finding the best technical and cost-effective solutions so that all stakeholders were satisfied.”
“Another challenge was communication and this had two aspects. Our base is 55 kilometers from the nearest town, so there are no fixed telephone lines and mobile phones often don’t work very well. Coupled with this, we had a large, multicultural team on site. I think there were 20 different nationalities and 450 people at the peak periods, working on 15 vessels. This meant that clear communication was critical, particularly when it came to explaining the Boskalis NINA safety standards, which many of the team were not used to working to. Safety is always at the top of our agenda and we had to be on extra alert and invested a lot of time in training. We are proud to say we have completed 3.5 million working hours without a single Lost Time Injury. This would not have been possible without the commitment of all personnel on site.”
The continuous variations represented an interesting technical and managerial challenge.
Special measures were also taken to protect the marine life?
Jord “Yes, as well as the initial special arrangements for the break-in procedure when we weren’t allowed to work outside, our vessels had turtle deflectors and ‘turtle watchers’ on board. They would keep an eye out for any turtles and we would stop work and move to other locations if they were spotted. I am pleased to say there weren’t any incidents over the course of the project.”
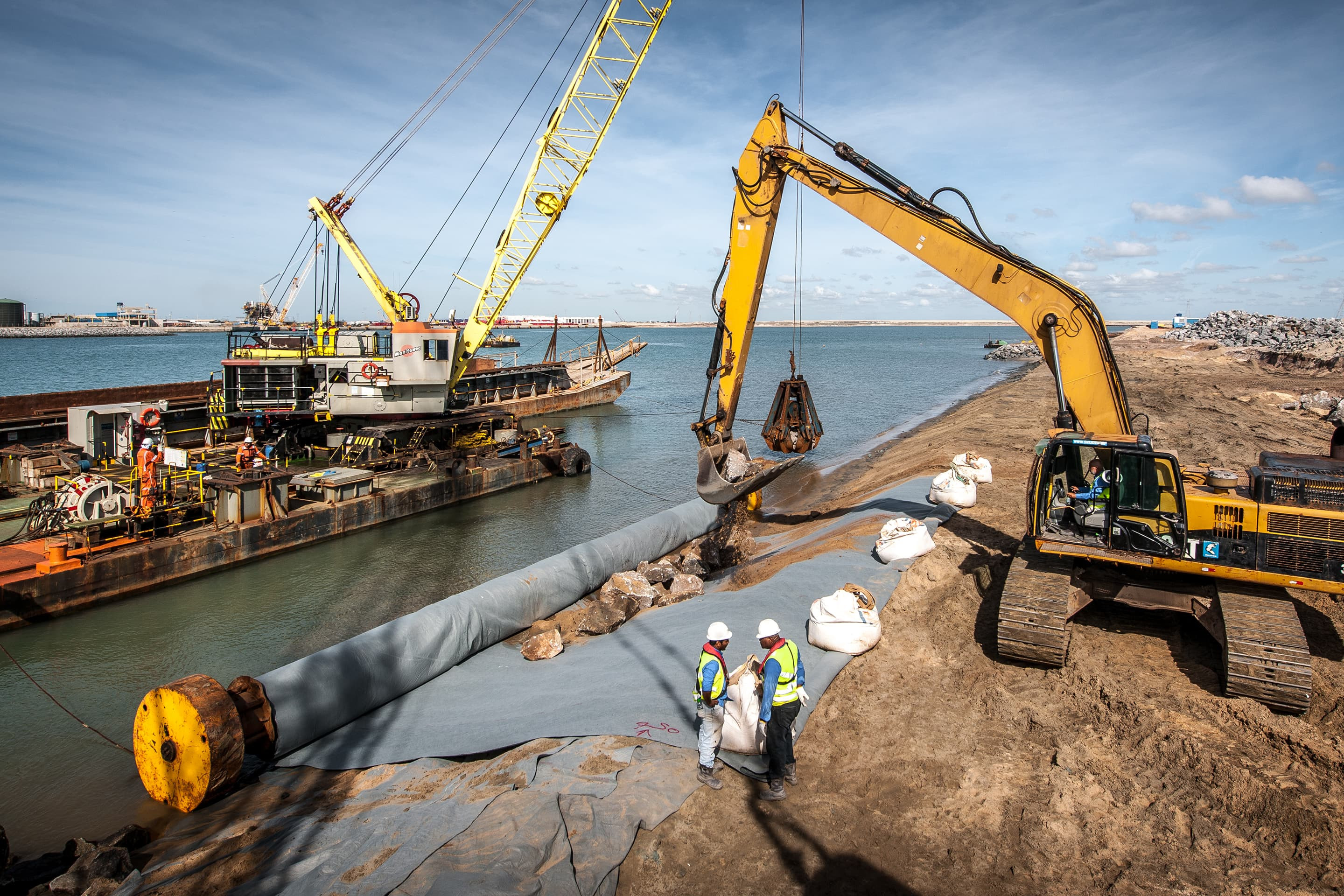
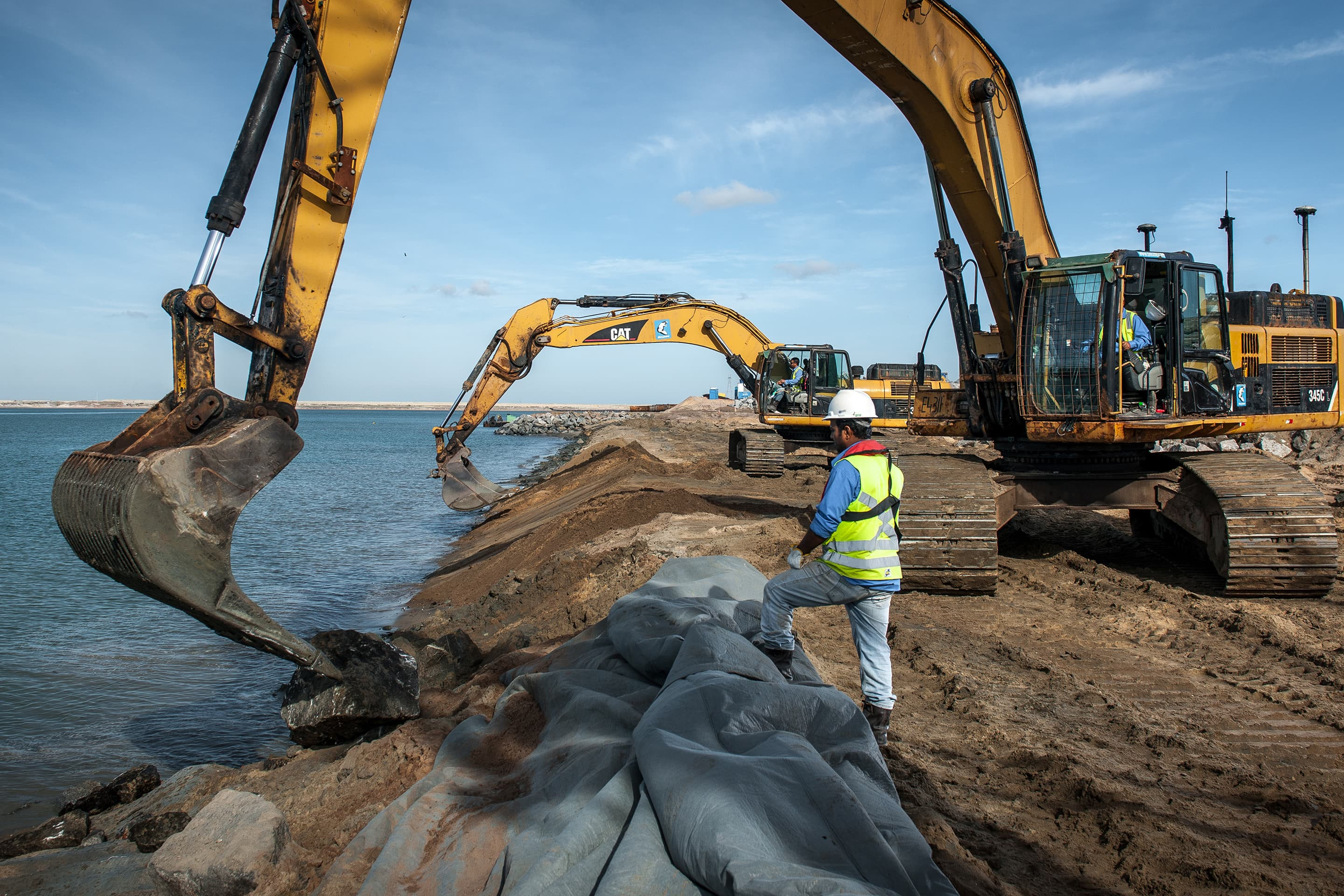
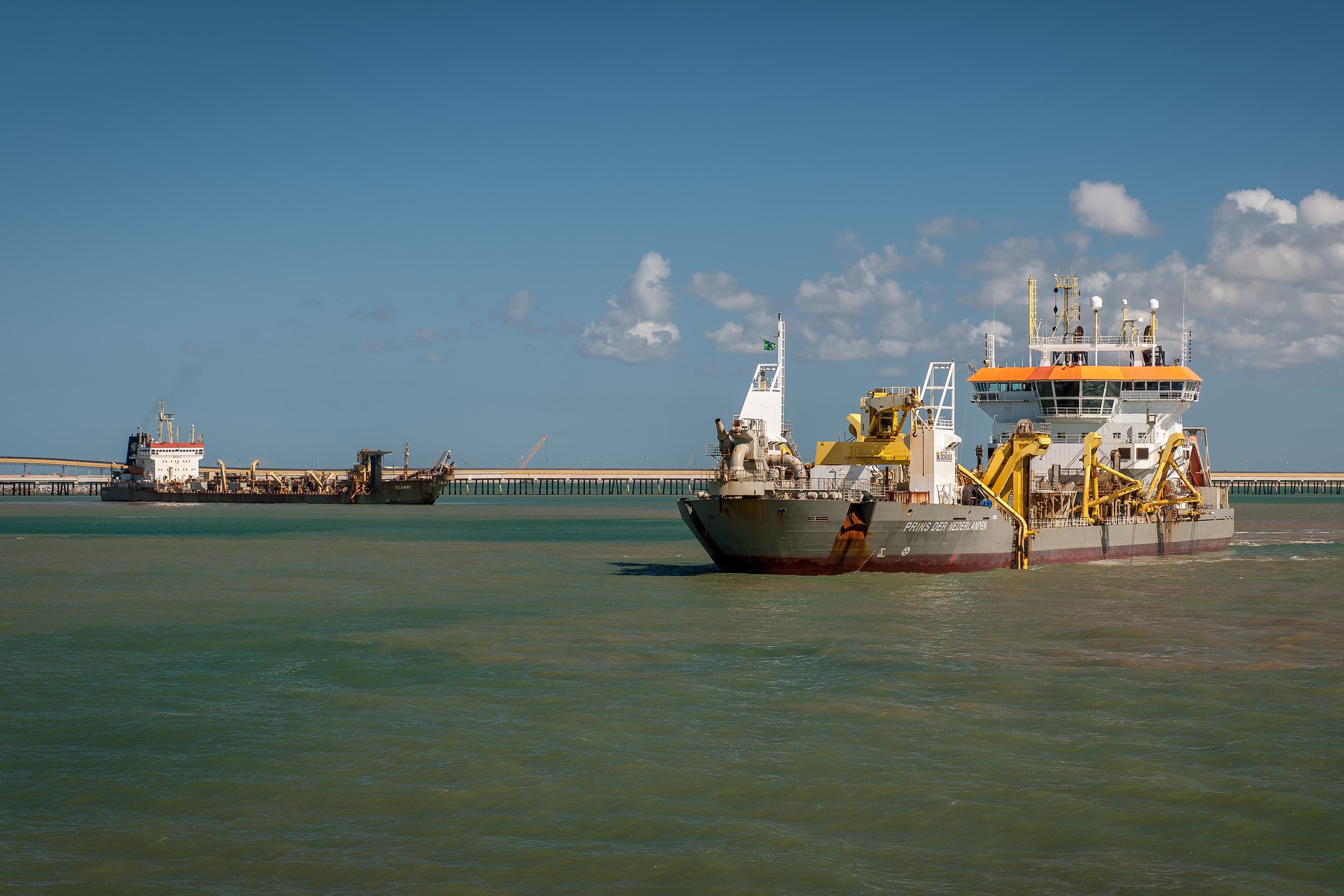
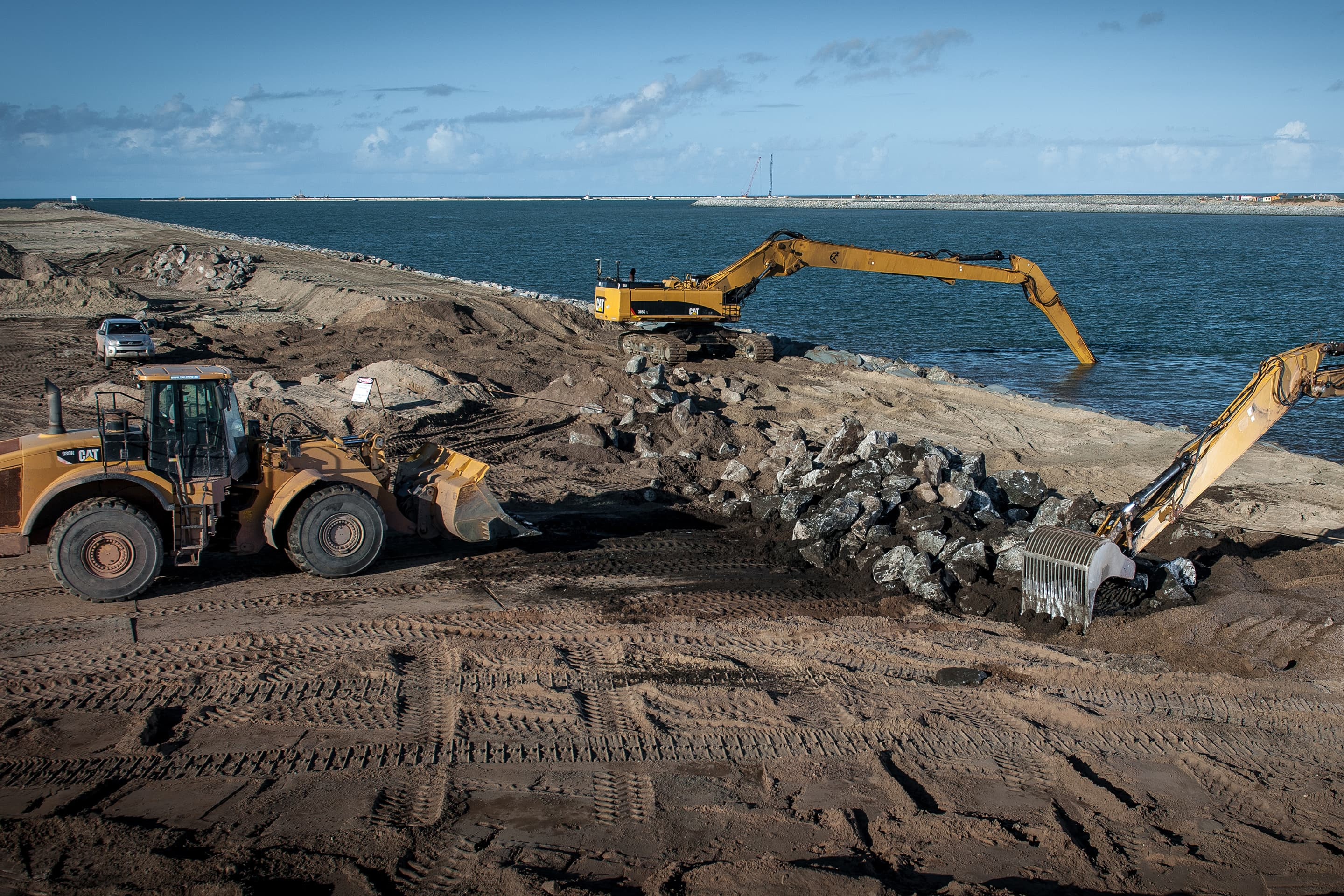
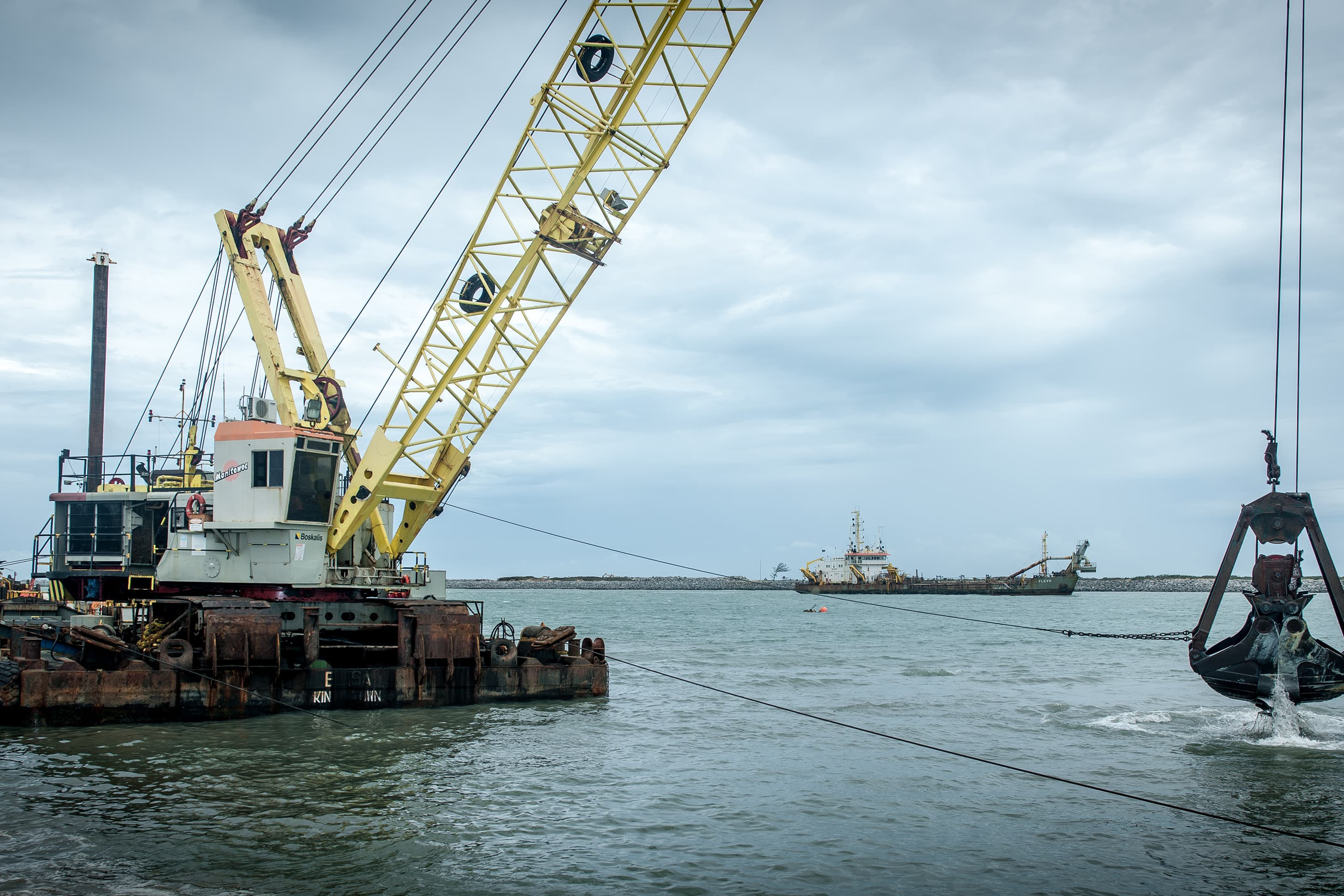