Malampaya — when timing is everything and an integrated solution is key
Seabed preparation is ongoing at the Malampaya gas field off the island of Palawan in the Philippines. This is an extremely complex project including dredging and rock placement to Transport & Installation of an offshore platform. Bas van Bemmelen, Boskalis Offshore Subsea Contracting Business Unit Manager and Pieter van Hekken, Boskalis Regional Manager, outline how Boskalis is drawing on all of its competencies.
What makes Malampaya a particularly challenging project?
Bas explains: “This is an extremely complex project with many different activities. Timing and proper planning are crucial and a vital part of the budget. The different smaller, complex activities determine the critical path and so the planning engineer is a lynchpin. This gives us the opportunity to demonstrate how Boskalis can deliver innovative and reliable solutions with a strong focus on safety and the environment.”
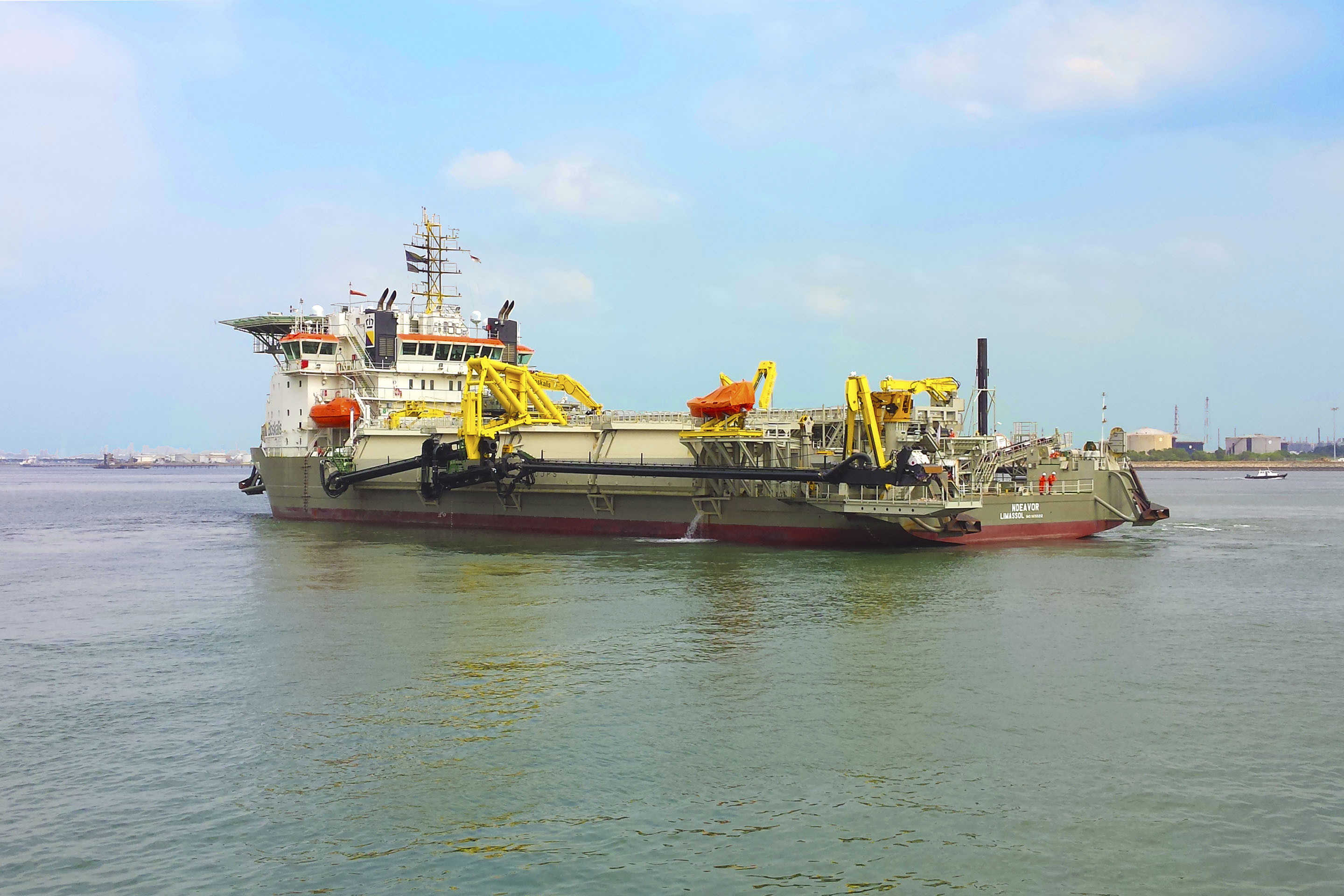
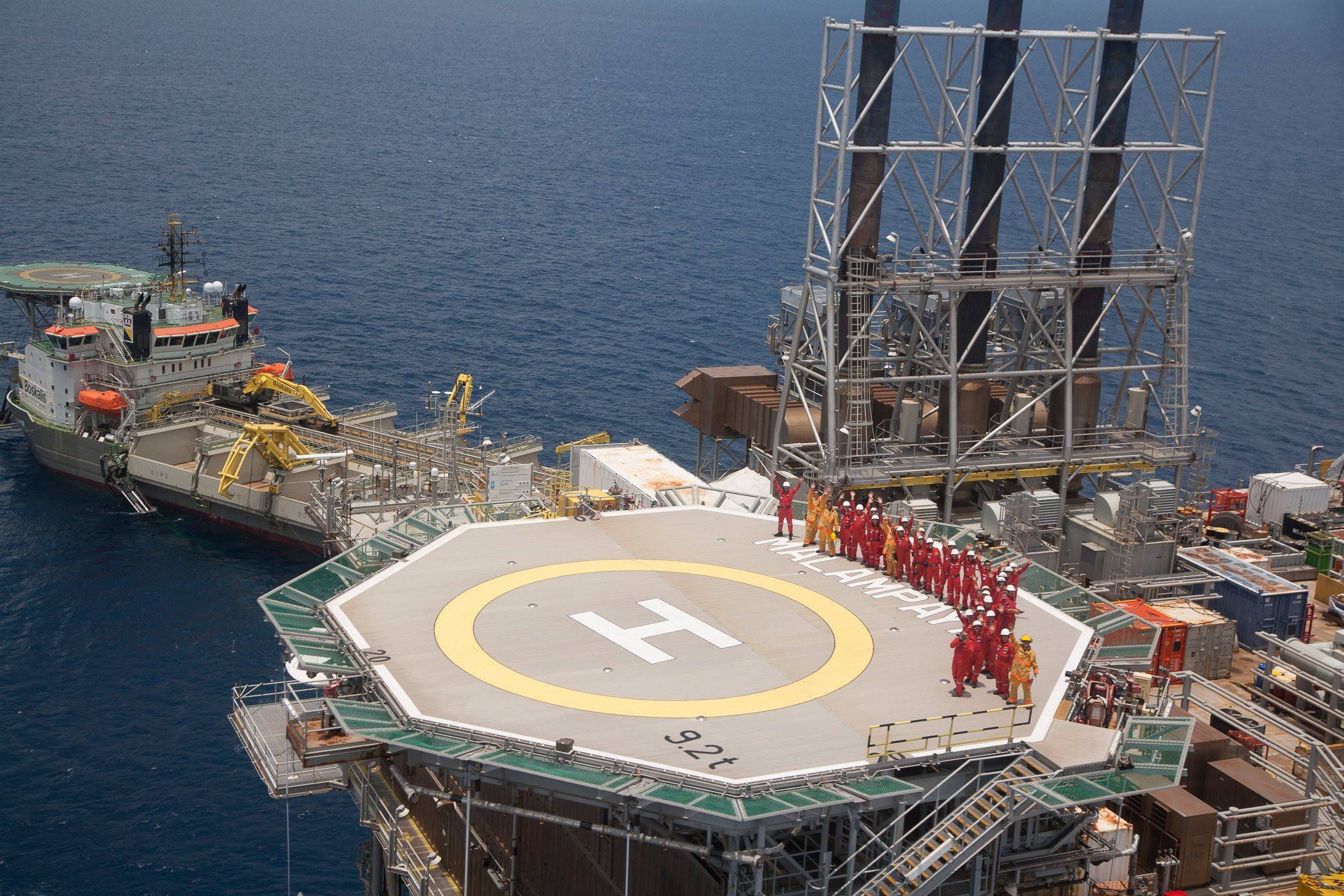
Would you say that one of the main advantages of choosing Boskalis is that the Group provides an integrated approach for these extremely complex jobs?
Bas: “Undoubtedly, our integrated approach has many benefits for our client because they don’t have to deal with interface issues. They work with one team with all the expertise and the equipment needed. Usually the seabed work would be completed and then we would hand over to the client and then the client in turn, hands over to a second contractor for the rock installation. But now we can offer a combined, integrated solution incorporating so many activities - dredging, rock installation, transportation and platform installation.”
Timing is always important of course, but in this particular case is it even more so?
Pieter: “When the Depletion Compression Platform (DCP) is hooked up to the platform, Shell has to take the existing platform offline, so the whole procedure has been planned years in advance. The Boskalis Offshore team is working to a tight deadline. Seabed preparation is well underway and the Transport & Installation phase is due to take place in the first quarter of 2015.”
And safety is always a high priority?
Bas: “100%! Shell’s trust in Boskalis Offshore is highlighted by the fact that it has been happy to accept Boskalis’ own safety program — NINA. We are very pleased that Shell acknowledges that this fulfills its own high safety standards.”
Could you give the readers an idea about how the work program is being organized?
Pieter: “We officially begin with the seabed work for the installation of the DCP, which involves digging down to a depth where the ground is strong enough. However, months of planning and preparations have preceded this. We have also been busy procuring the rock needed.”
“The rock procurement alone is a substantial challenge within the tight deadline. Around 50,000 — 70,000 tons of rock is being procured from local quarries, as well as some 10,000 tons of iron ore for the ballasting of the DCP. Boskalis’ Rock Department is also providing assistance to test if the rock meets the exact specifications.”
“After the initial preparatory work, Boskalis Offshore will take the DCP to the location, position it and install it using three to four 100/200 ton Anchor Handling Tugs. To stabilize the platform extremely dense iron ore gravel ballast is put into all four footings as soon as the installation has been completed. Then finally, a permanent bridge linking the gas production platform to the new compressor platform will be installed.”
In terms of equipment, one multi-functional vessel was built with this project specifically in mind?
Pieter explains: “That is right. The Ndeavor is a truly multi-purpose vessel and plays a key role in this project. We first looked at conventional solutions for Malampaya, in the first instance dredging and rock installation using the usual vessels. We could have used a fallpipe vessel to install rock for the platform’s four foundations and additional tugs to position the platform alongside the existing platform. Then yet another ship would have to come to fill the platform footings with iron ore to stabilize it on the seabed. All in all it meant that we would need to mobilize quite a few vessels from around the world for a few short operations.
That’s when we decided to add dredging capability to the DP2 vessel the Ndeavor. We turned the ship into a kind of Swiss Army knife, equipping her with proven technology. In addition to a modular dredging system, a modular ballasting system and a side dumping facility we also installed a 50-meter fallpipe. She can transport 4,500 tons of rock at the same time. Below deck there is also every kind of measuring equipment for underwater precision work. The ship will play a key role in the dredging, rock installation and positioning of the platform by the Boskalis tugs, as well as in connecting the ballast hoses at a depth of 50 meters using our remote-controlled equipment and injecting the iron ore into the footings. The project will conclude with the presentation of the 200-ton connection bridge to the installation team on board of the two platforms.”
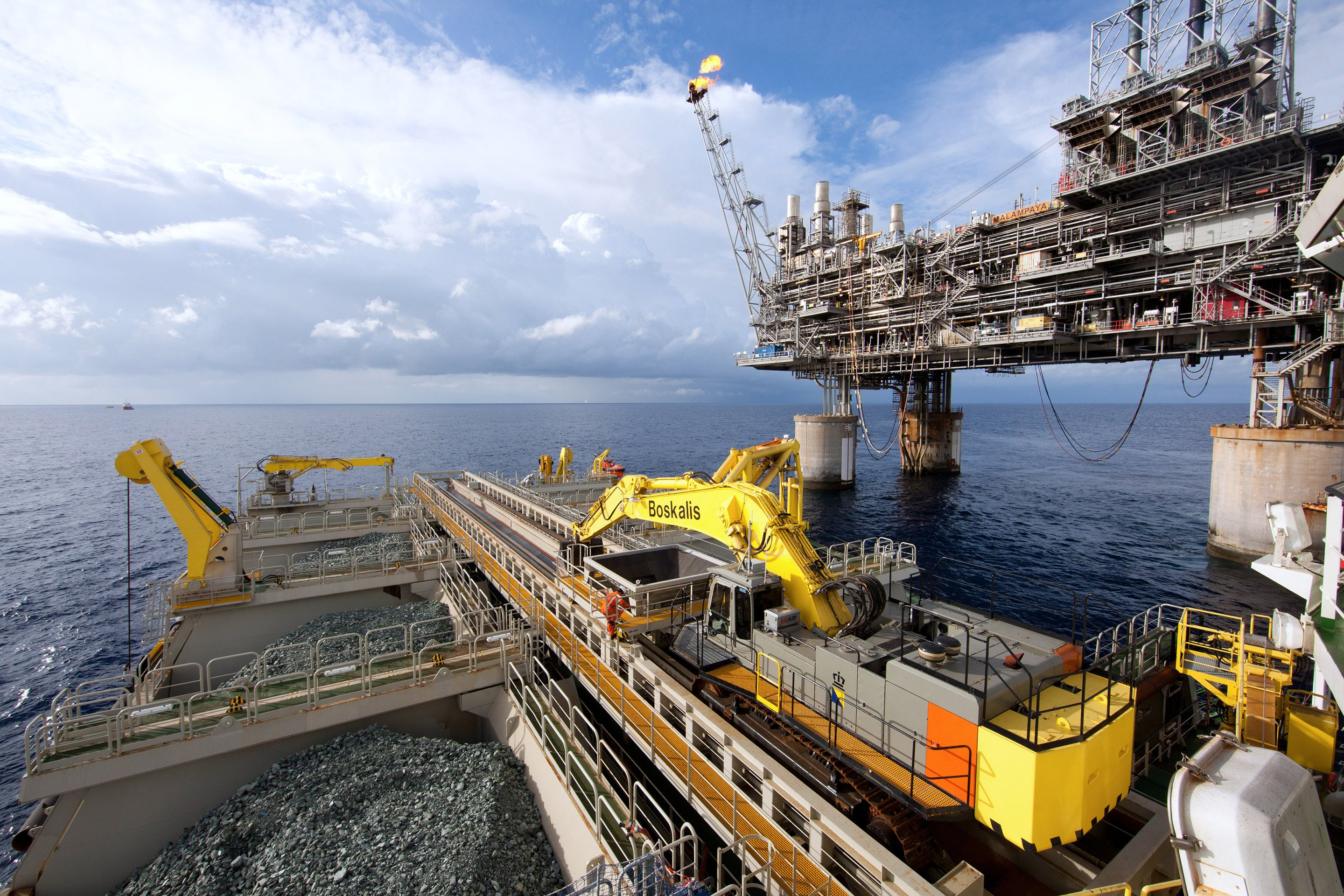
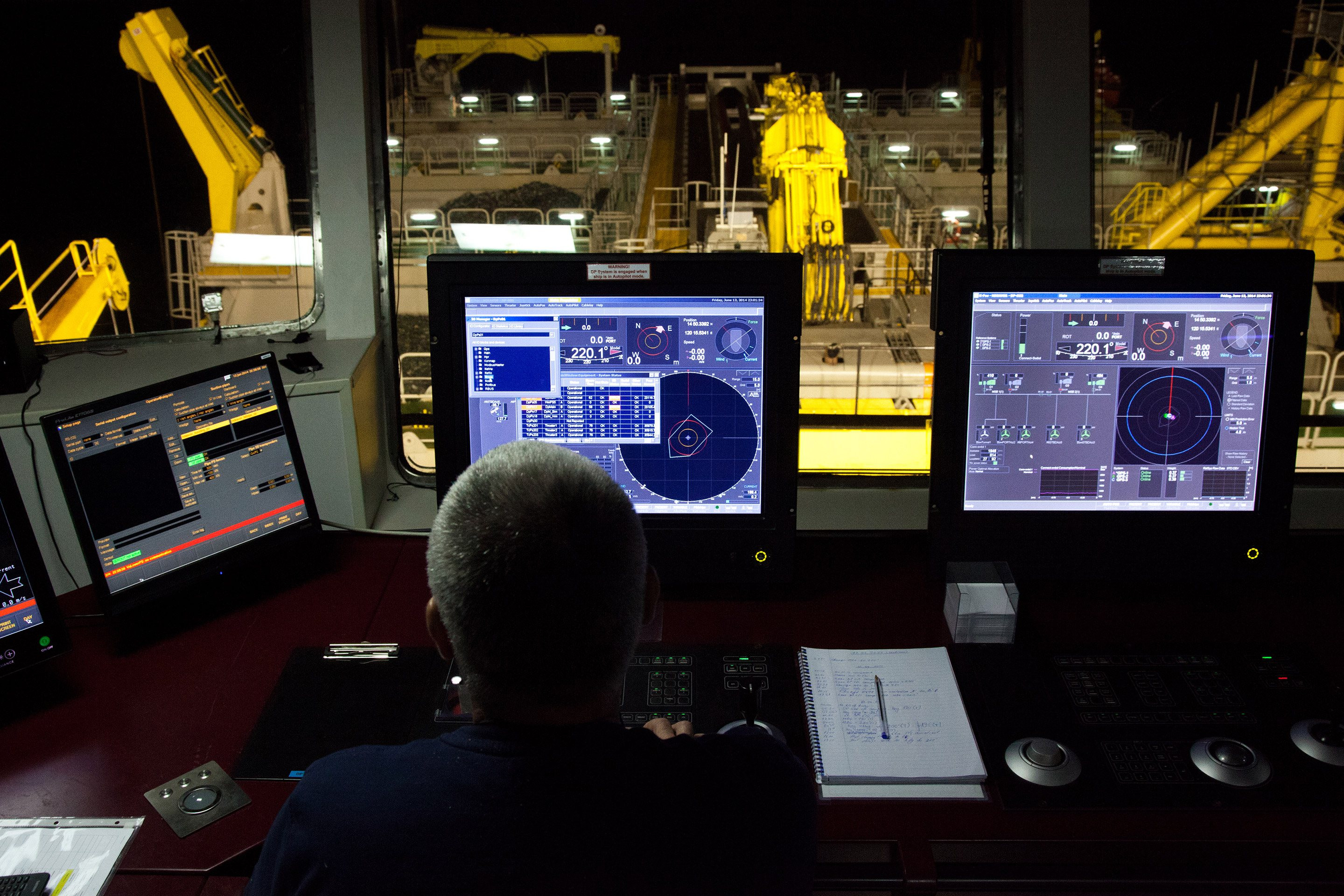
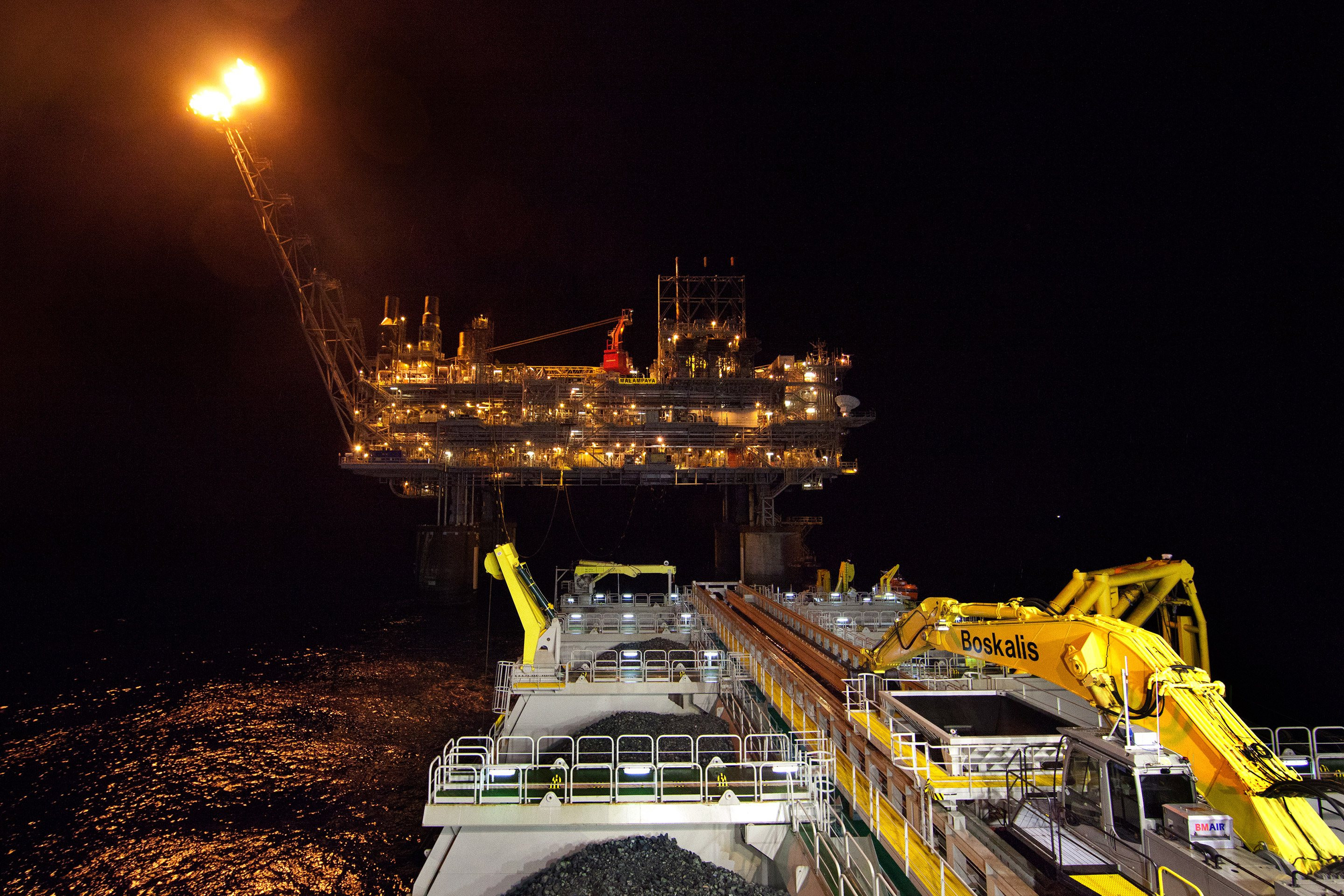
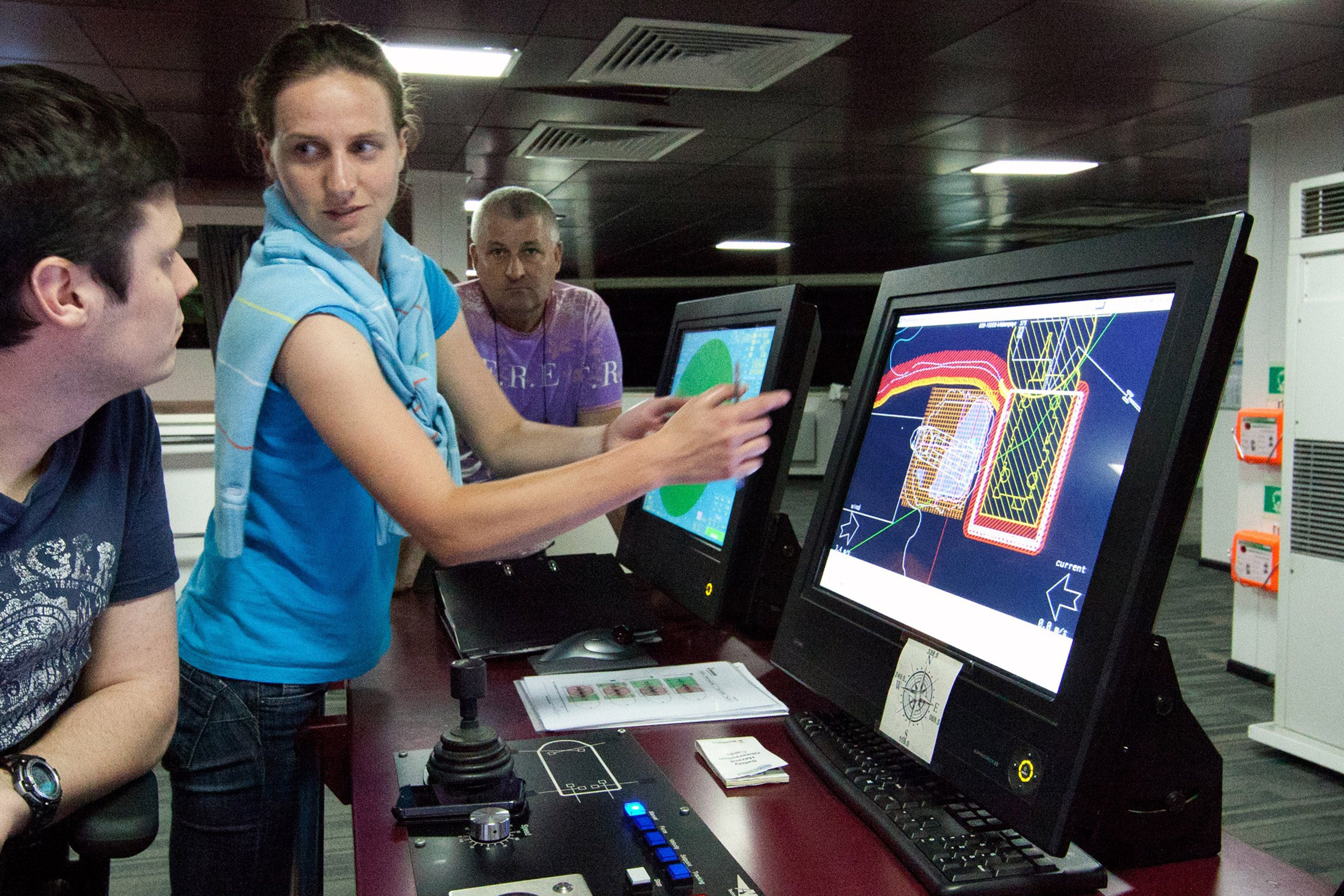
What makes you particularly proud when it comes to the Malampaya project?
Bas: “This project combines all our expertise and is only possible thanks to the intensive collaboration between our colleagues in the construction department, R&D, survey, the crew of the Ndeavor and various units within Boskalis Offshore. Having a base next door to Shell also plays a very important role in the success of this project. There is a lot of interaction and fine-tuning between the project teams, our relationship works very well.”