One of the largest natural gas projects ever, Gorgon is the ultimate example of creating something from nothing!
In 2009, Boskalis was awarded a contract on the Chevron-operated Gorgon Project, which is one of the largest and most complex contracts to be undertaken in our company’s history. Boskalis’ scope of work included the design and construction of some of the port facilities at Barrow Island. Our team talks about Boskalis’ involvement in this fascinating project.
In addition to Barrow Island being located 60 kilometers off the coast of Western Australia, it is also an internationally significant nature reserve. It is difficult to imagine a more challenging project — could you try and give our readers an idea about what Boskalis faced when work first commenced?
Raymond Yeung, Project Director, explains: “The challenges were numerous, not just in terms of technology and logistics but also with regard to safety and the environment. Due to the isolated location of Barrow Island a huge logistical effort was required. Getting the people, equipment and the rocks needed for the coastal protection into the right place was quite challenging. The transportation of the rock alone was a significant effort. About 475,000 tons of rock had to be transported all the way from Perth for the coastal protection structures. We used five large seagoing tugs that sailed back and forth with 10,000 and 12,000 ton barges. That’s the equivalent of a 3,000 km voyage.”
Our scope of work wouldn’t have come together without teamwork.
“Accommodation and transportation of our workforce was also quite a challenge. One of the most remarkable aspects of our scope on the Gorgon Project was that everything took place at sea — working and living. This meant that all of our staff — at the height of the project, more than 500 people – were housed on the accommodation vessel Finnmarken.”
Undoubtedly, talking to anyone from Boskalis working on this project — whether they were involved in catering, medical assistance, engineering or civil works — there is one thing they all mention — the importance of teamwork.
Niels Asjee, Deputy Project Manager Marine, says: “The disciplines involved were specialized on their own, but the synergies we managed to establish as a team proved to be a real necessity to safely develop our works on the project.”
Alex Ledingham, Marine Superintendent, M&R comments: “Our scope of work wouldn’t have come together without teamwork. There was a great culture on site. Many challenges have been overcome by the workers which create stronger bonds and greater prospects for future projects.”
Dirk Goudswaard, Master, BKM 102: “I am most proud of the way we worked as a team. We created our own buddy system with experienced people guiding the newcomers in order to keep them safe.”
Zoe Burton, Environment & Quality Superintendent, adds: “In the environment and quarantine team, we relied heavily on teamwork, not only from our own team members but each and every member of the project team. Everyone on the project understood the importance of quarantine and has embraced that.”
And given this isolated and difficult location, safety of course was always at the forefront of all the operations?
Raymond Yeung continues: “Yes, all of our employees had to be ferried to and from work by ship and that meant vessel-to-vessel transfers. Given that embarkation and transferring between vessels carries well-known risks, much attention was paid to this during the preparation phase.“
“A number of smaller boats used for crew changes underwent technical modifications to make transfers as safe as possible and so that they complied with our STOP program. This remained a recurring item at the toolbox meetings and safety sessions before every shift included this topic in their discussions.”
“Our STOP program paid off: around 500,000 safe transfers were made during the course of the project. It is worth noting that over 4 million man-hours were completed without a lost time injury. The Project awarded Boskalis a ‘Certificate of Appreciation’ in recognition of this achievement.”
The weather also had quite an impact?
Raymond Yeung comments: “Yes, frequent cyclones in the region were a complicating factor. We maintained constant contact with the Australian meteorological institutes. Sometimes the weather conditions forced us to halt activities.
When this happened, all the vessels and other equipment were demobilized to a sheltered location at Dampier, around 80 nautical miles east of the project. Our colleagues at SMIT coordinated this major operation. They were the cyclone mooring masters in Dampier and made sure that all the equipment was well anchored. Sometimes it lasted a few days, sometimes more than two weeks and almost a month in one case.”
Given the environmentally sensitive nature of this project, what did Boskalis do to mitigate the impact of its work?
Niels Asjee explains: “A priority on this project was the protection of animal and plant life. Barrow Island is a Class A nature reserve and home to animals and plants that you don’t find anywhere else, not even on the Australian mainland. Therefore to protect these species, it was vital the Project’s quarantine procedures were strictly adhered to.”
The work was carried out under an extensive set of environmental requirements, ranging from the use of biodegradable hydraulic oil and waste separation to stringent quarantine requirements. Boskalis trained its own multidisciplinary inspection team, including biologists, to carry out these inspections. Anyone traveling to the island by air or sea was subject to strict checks to prevent non-native plant and animal species from being introduced to the island. For example, all vessels had their hulls thoroughly cleaned, in many cases in dry dock. Every last piece of dry equipment was brought to a specially designated, demarcated area where it was taken apart and checked for the presence of any seeds, substances and small creatures.
Hans Mooij, Works Manager Dredging/Deputy Project Manager Civil adds: “One of the biggest challenges and one of our great successes was the minimal amount of fauna interactions. The success was reliant on the relentless support from the crews and reclamation team, providing spotters and stopping works to ensure the marine mammals’ safety.”
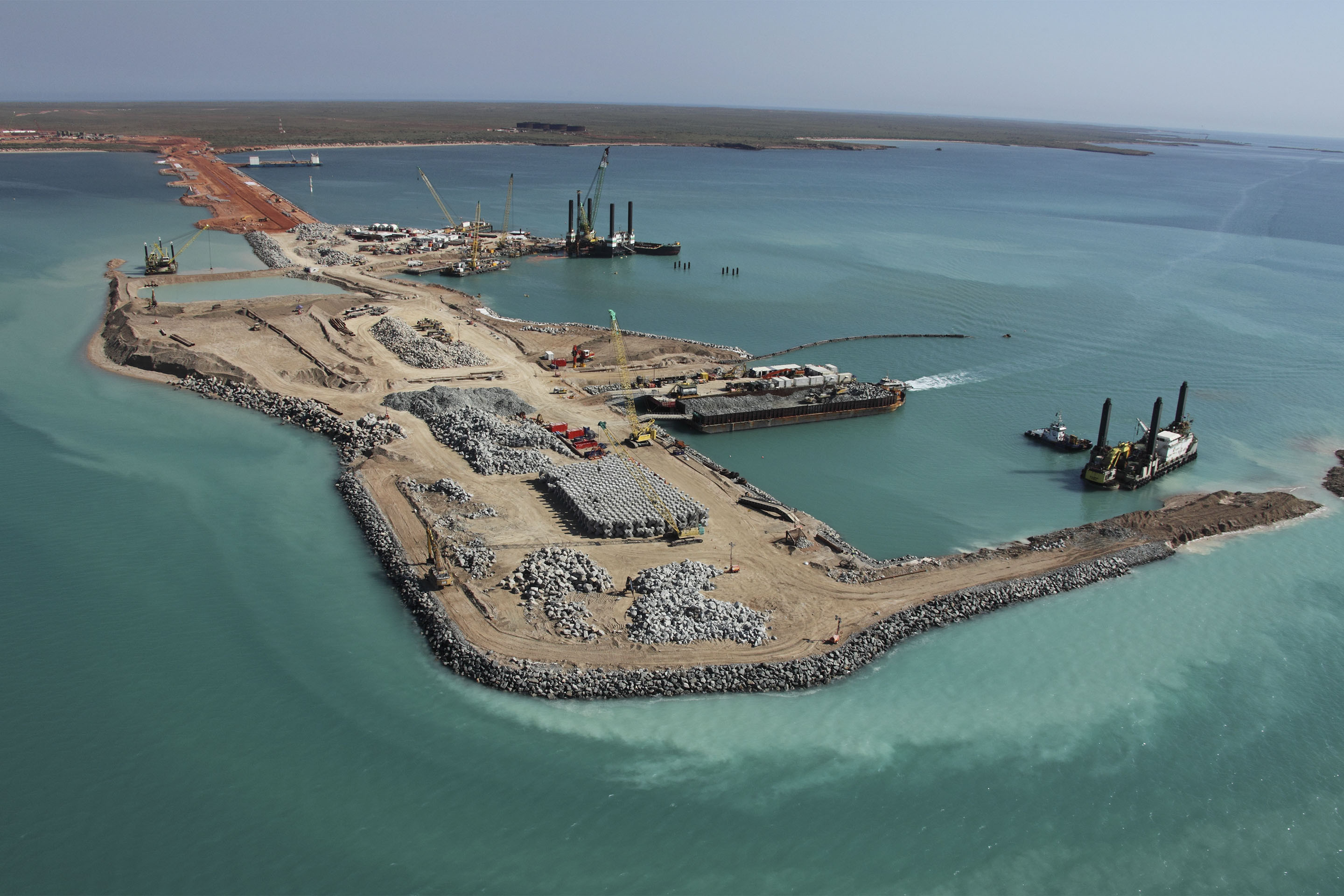
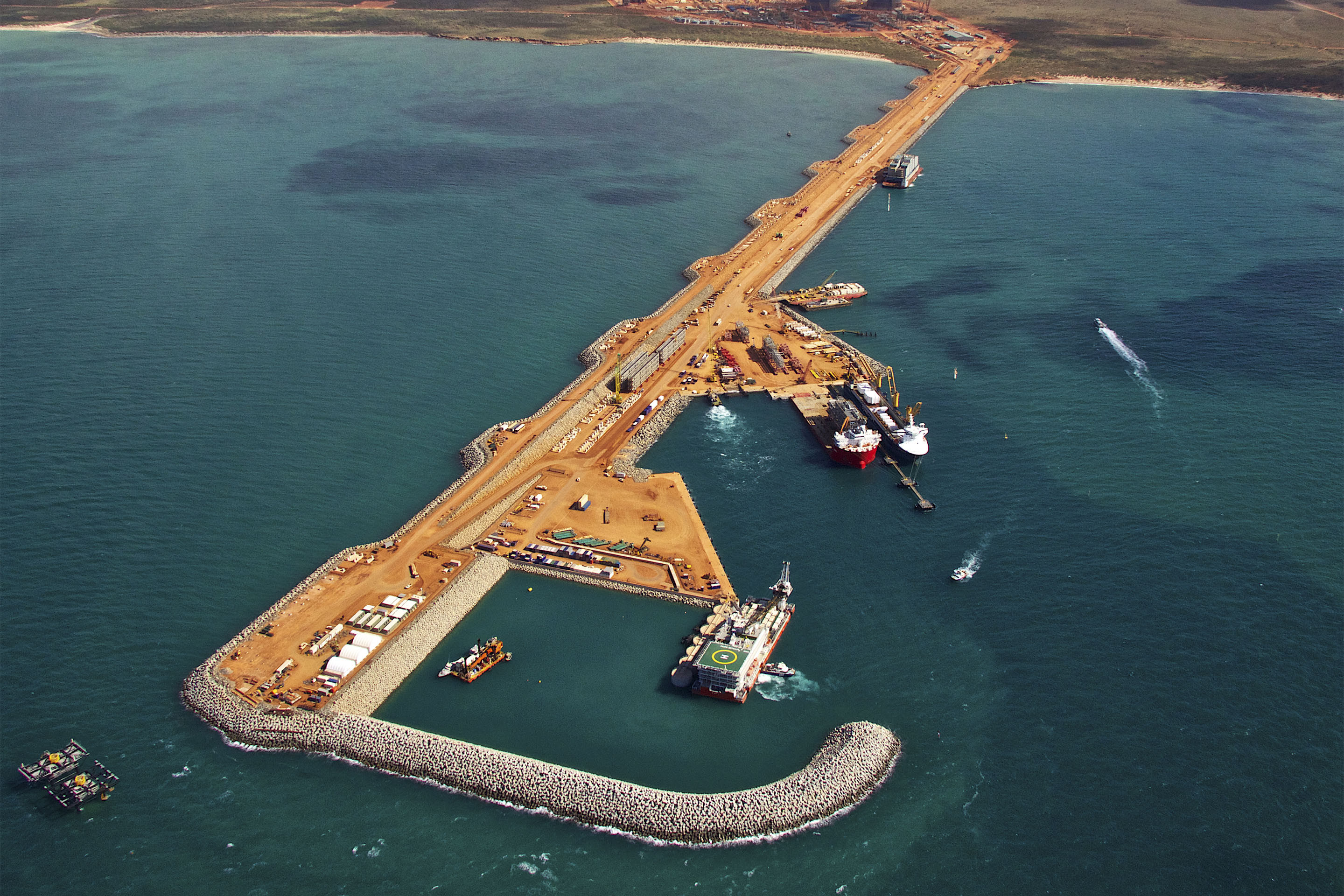

And the Project recognized these efforts with an award?
“Yes, we were very proud when we were presented with the ‘Environmental Excellence Award’ in recognition of our observations of animal life, compliance with the terms of the Environmental Management Plan, employee awareness and the implementation of mitigating measures,” says Raymond.
When looking back on such an impressive achievement, how would you say the team’s horizons have changed Raymond?
“Well we always knew this project was special but it is not until you see the end result that you realize just what we have done. There was absolutely nothing here and now there is a facility that will be a powerful player in the world’s supply of natural gas. The many teams and nationalities contributing to the project came together and despite the obstacles they had to overcome, they stayed positive and we did it!”
Please look at our corporate website for more information on this project.