Seamless coordination, precision timing and teamwork were vital when Boskalis transported and installed DolWin Beta, the world’s largest High Voltage Direct Current (HVDC) converter platform, in the German Bight of the North Sea.
The DolWin2 project encompasses a huge range of tasks: transportation, rock placement, towage, survey services, anchoring, installation and ballasting. The broad deployment of many different disciplines from our company made this assignment into a prime example of teamwork. It shows our expertise in providing the client with a one-stop shop for highly complex offshore projects. Dirkjan van den Boom, Regional Manager Northwest Europe for Boskalis Subsea Contracting, explains.
Could you outline the different stages of the project?
“The first contract Boskalis handled was through Smit Lamnalco and Dockwise, which transported the platform from Dubai to Haugesund, Norway. This transport took around 40 days. The platform was undergoing further outfitting and commissioning at Aibel AS in Haugesund.”
this contract involved a very long preparation time and extensive engineering work before it started. But the biggest challenge was coordinating all the vessels and getting them in time, at the right spot.
“Meanwhile, Boskalis was contracted for the pre- and post-installation of the scour protection and ballasting after the platform’s installation. We carried out the pre-laid scour protection deploying the fallpipe vessel Rockpiper late in the summer of 2014. Prior to this Boskalis was asked to perform the cardinal buoy installation, marking the site for other marine traffic. Although the German Bight is a fairly rough part of the North Sea, the weather was fair during both campaigns and both were completed on time and within budget. A few months after this operation we got a variation order for the platform tow-out and installation, where the platform was towed from Haugesund to its final location, 45 kilometers off the coast of North Germany. This part of the operation was carried out by our three, 200-ton bollard pull Fairmount vessels. The ocean going tugs went to Norway at the end of July to tow the platform to its destination. Meanwhile the Boskalis Union Sovereign anchor handling tug installed the anchor pattern where the platform was moored during the installation. Another Fairmount tug assisted to ensure it was installed in exactly the right position. Towage took about four days. The four tugs were used to position the platform safely above the set down location. It was slowly submerged onto the gravel bed that we installed there last summer.”
What did Boskalis do next?
Dirkjan: “Overall, after completion of the water ballasting to get the platform in position and the release of the tug boats, we continued with the solid ballasting. The fallpipe vessel Rockpiper had been outfitted with a purpose-built ballast spread, which was designed and built in-house. Some 52,000 tons of rock was eventually used to ensure the platform can cope during heavy North Sea storms. The rock was dry during transportation and then mixed with water on the Rockpiper. This mixture of water and rock was pumped into the platform pontoon and column tanks hydraulically. During the ballasting works the so-called diving support vessel Protea executed the concrete matress installation around the bellmouths of the platform. This to ensure a smooth transition for the cables into the bellmouth and maintaining the maximum protection against scouring. Once the platform was ballasted, the fallpipe vessel Seahorse, which has been fitted out with a fallpipe installation on the side of the vessel, installed the scour protection around the legs to protect the structure.”
It shows our expertise in providing the client with a one-stop shop for highly complex projects.
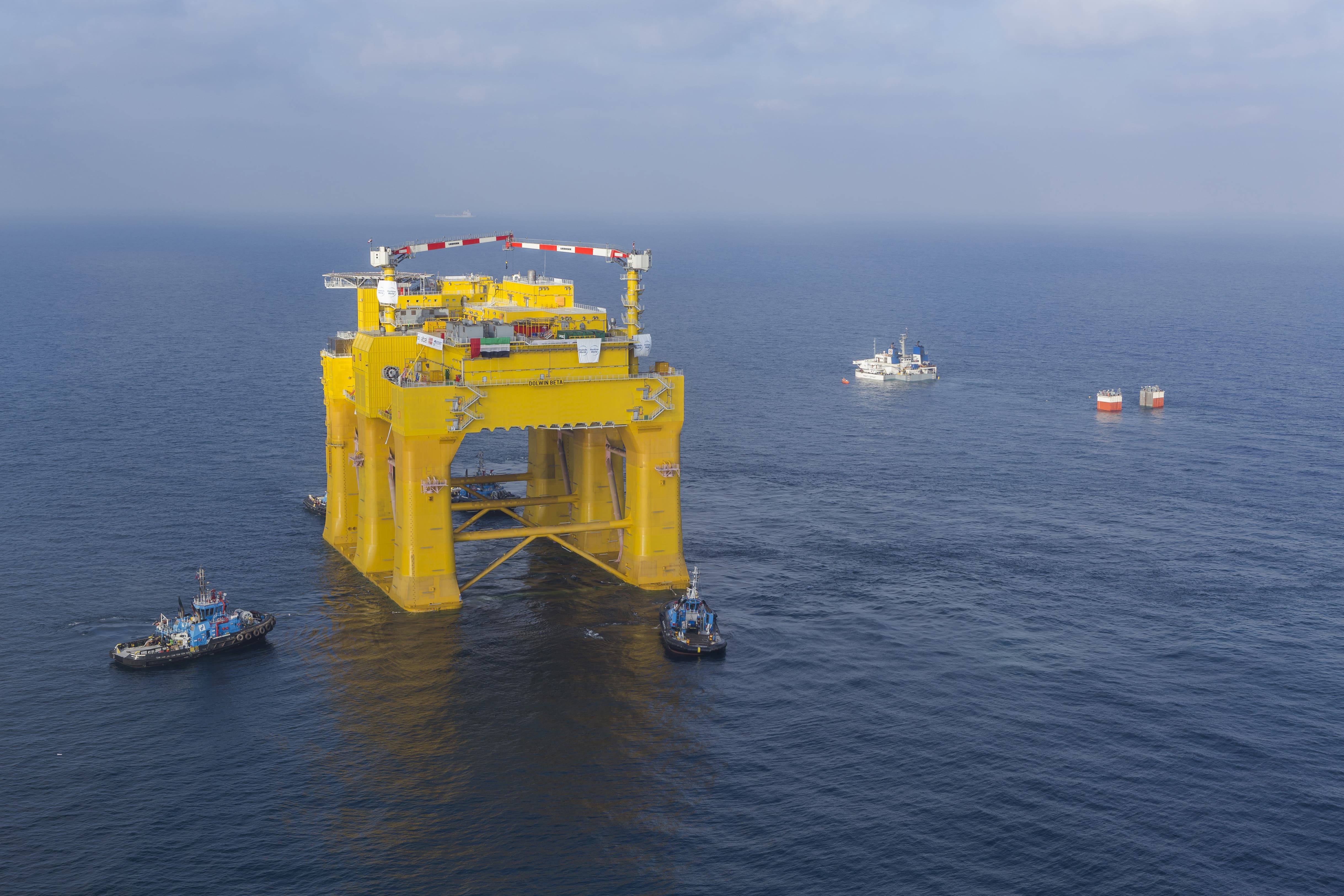
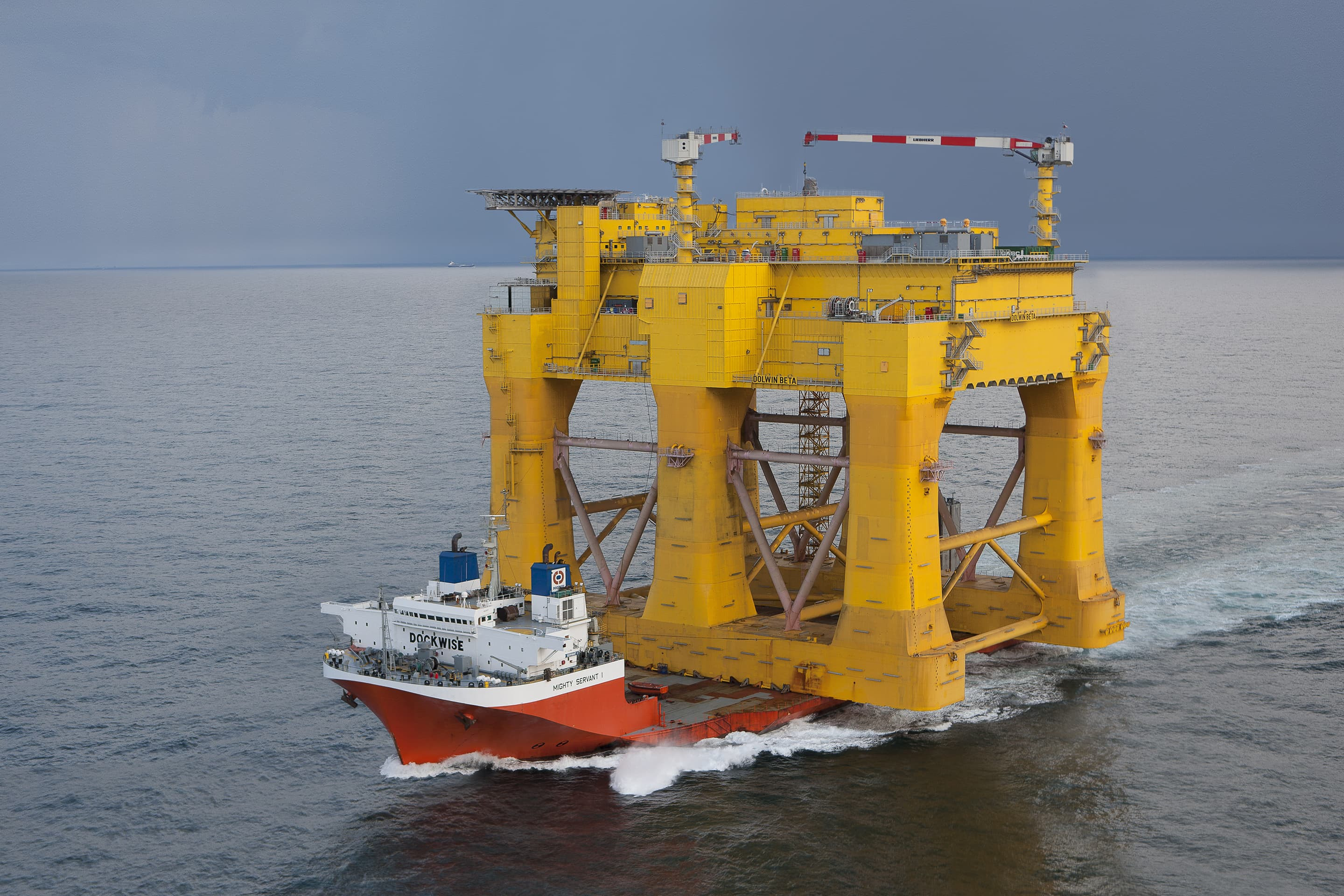
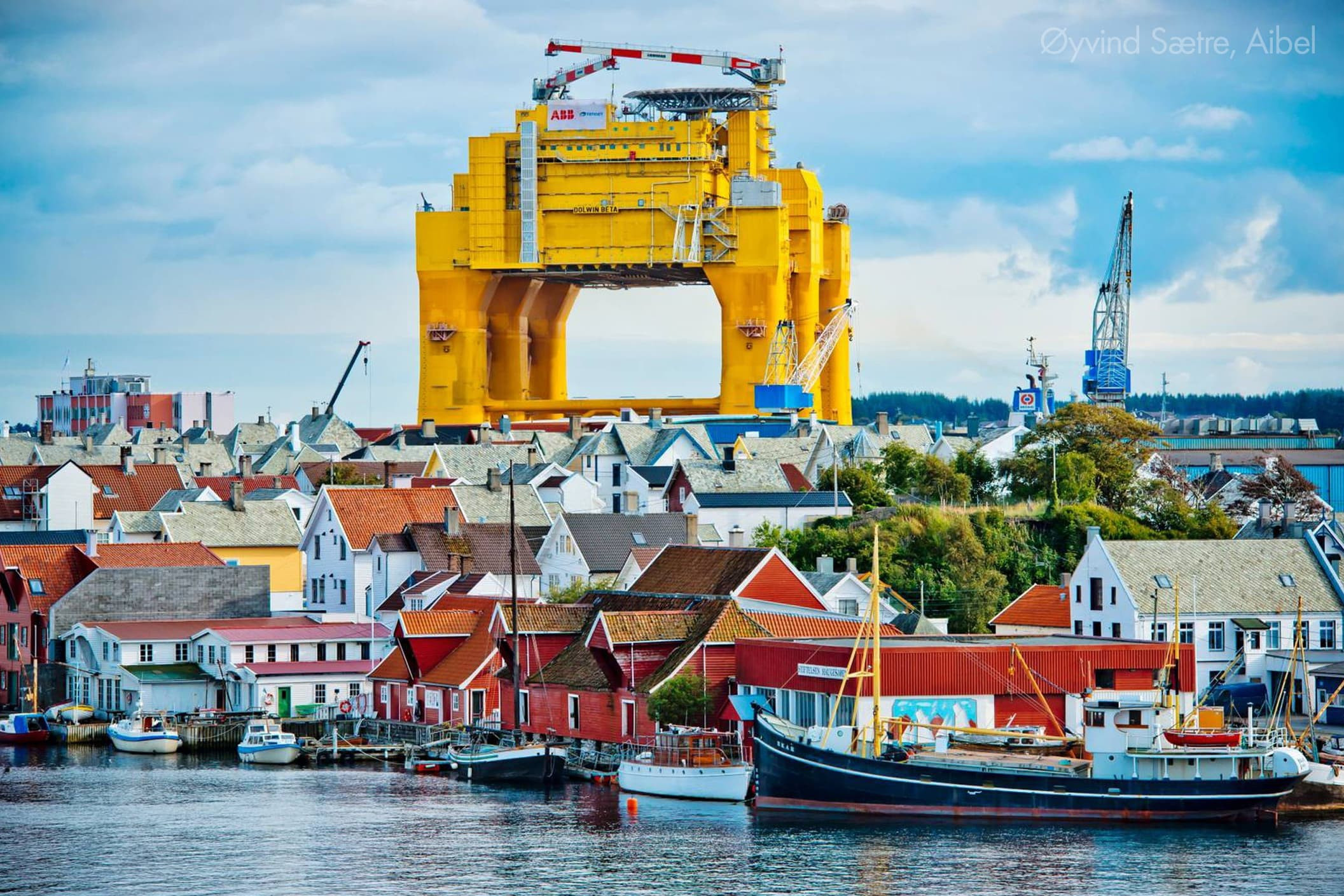
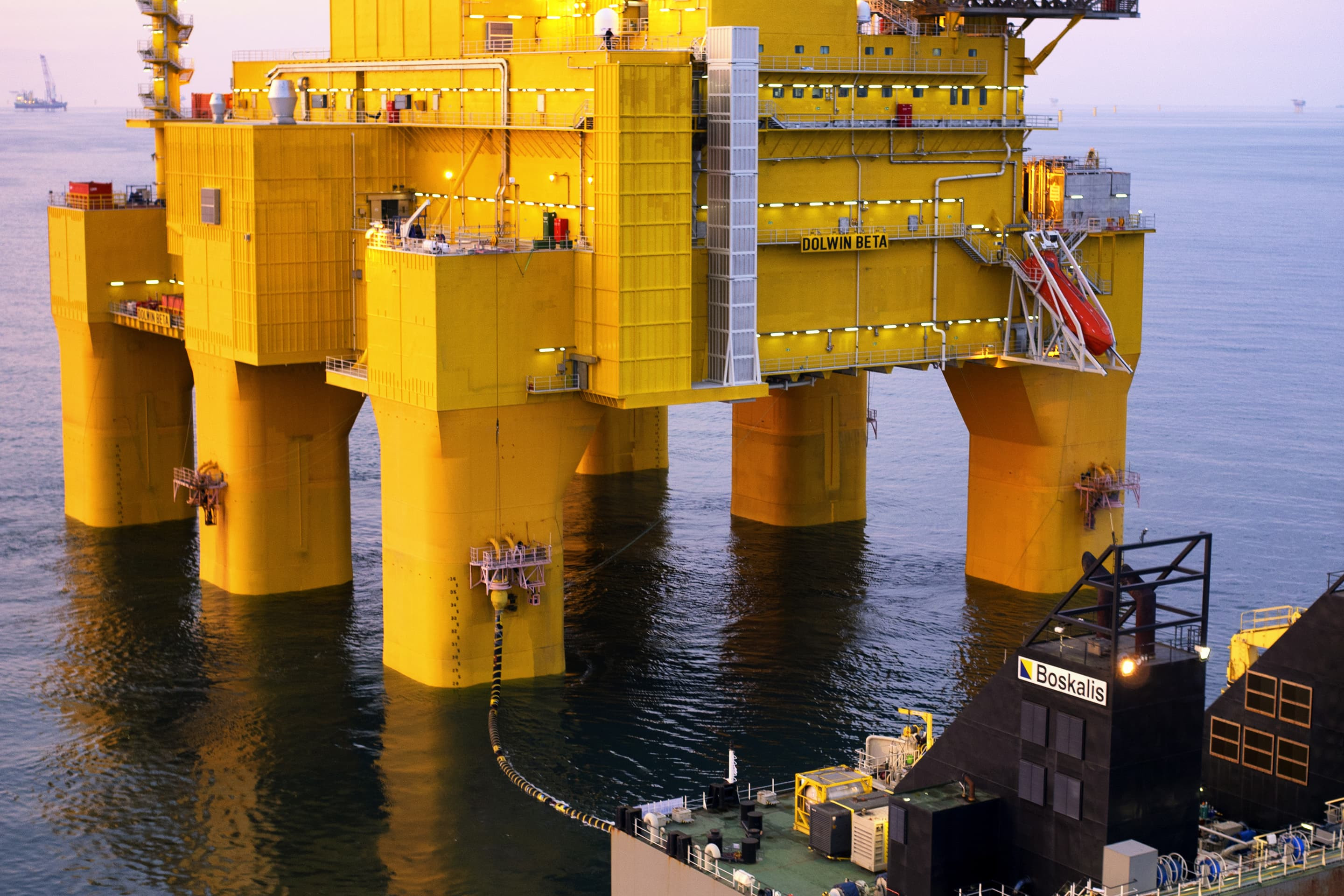
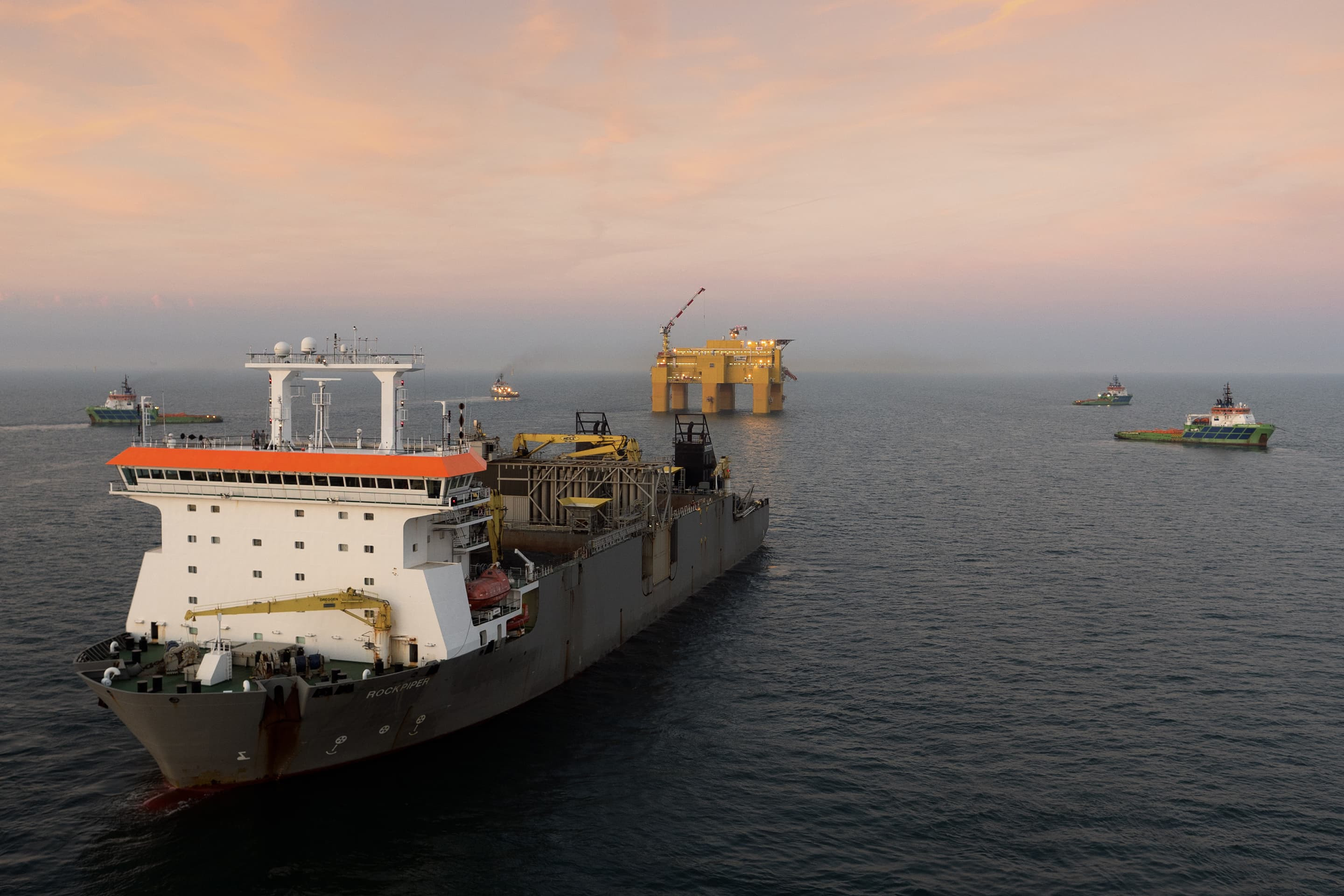
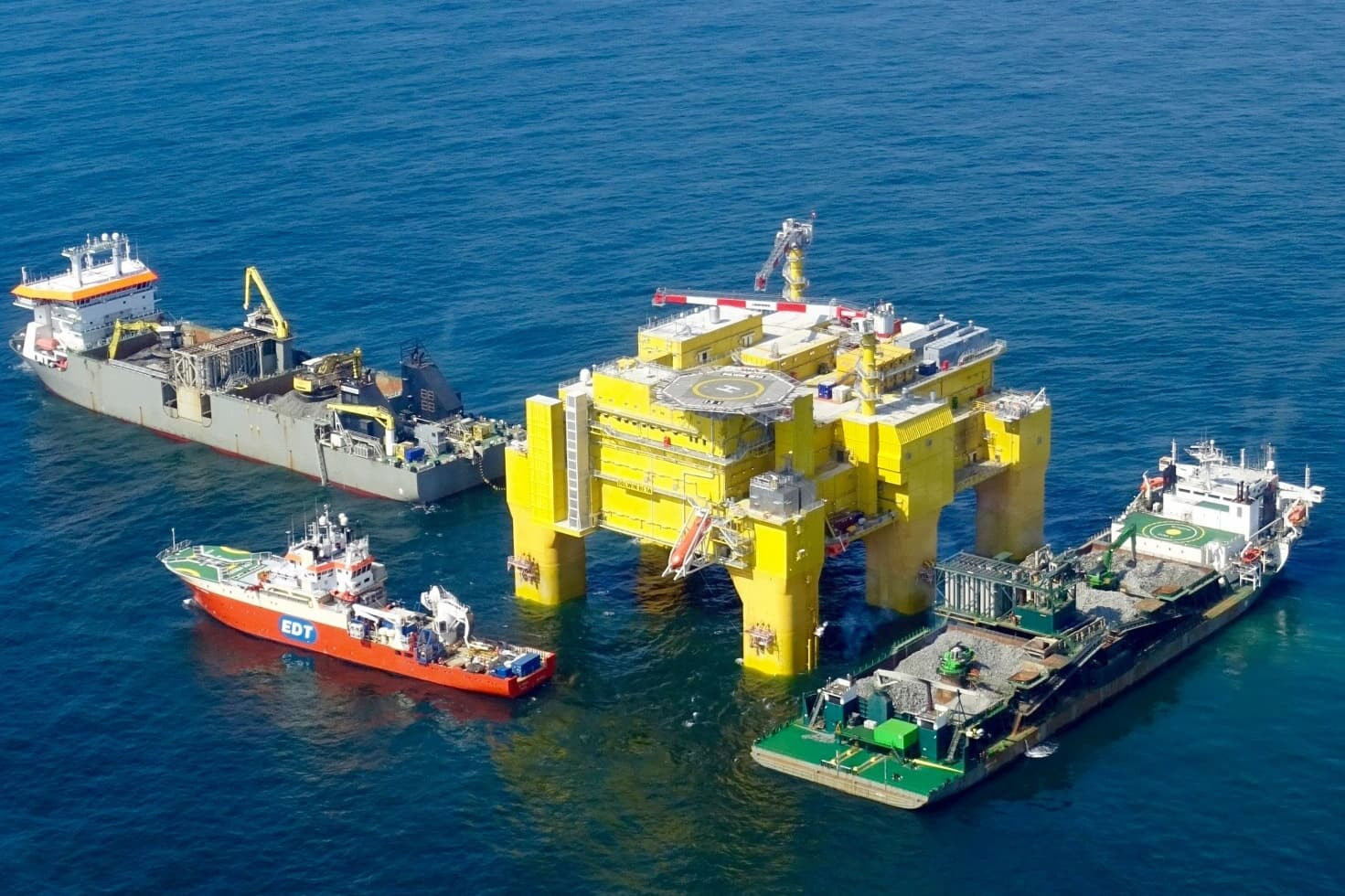
As well as the sheer size of the platform, what were the major challenges of this project?
Dirkjan: “Certainly, this contract involved a very long preparation time and extensive engineering work before it started. But the biggest challenge was coordinating all the vessels and getting them in time, at the right spot. Seven vessels were involved at the peak of the operation and it really was precision timing. The project team had to make sure the vessels weren’t waiting for one another and all of the vessels were in different locations. Coordinating everything was a huge undertaking for the project team. However, the client was extremely happy with how everything went and we are delighted to have lived up to their high expectations.”
Boskalis has a growing presence in the renewables sector. What do you think this project highlights about the company’s ability to handle these complex jobs?
Dirkjan: “DolWin2 demonstrates the broad scope of services we can provide. We are a one-stop shop contractor. The synergies within Boskalis are a big advantage for our customers. We can offer them the complete package.”