The Duqm project in Oman was completed earlier this year. As far as size is concerned, this huge project is reminiscent of major port construction projects such as Maasvlakte 2 in the Netherlands, Gorgon in Australia, Khalifa Port in the UAE and Porto do Açu in Brazil. “On the Duqm Liquid Bulk Berth Project, Boskalis has set new standards in terms of both productivity and safety,” says project director Bart Pröpper. “Meeting all deadlines in a highly complex environment required maximum output from our equipment and effort from our staff. Breaking safety records at the same time made this project a huge achievement.”
In recent years, Boskalis has been involved in projects in Oman, including The Wave and Salam Yiti in the port city of Muscat. The present engineering, procurement & construct contract is part of the master plan of the Special Economic Zone Authority Duqm. This plan is aimed at port development in Oman, with the port of Muscat being adapted to accommodate cruise vessels and the port of Salalah focusing on container handling. The Duqm Liquid Bulk Berth Project involves the creation of an enormous port area that will house, among other things, a liquid bulk terminal and a refinery. “Our assignment included the construction of a large port basin and an entrance channel with a depth of 18 meters, as well as the construction of a kilometer-long quay wall and two 400-meter-long jetties,” Bart says. “What made this work unique is that we decided, at an early stage, to start by building a temporary heavy ring dike of sand, a so-called bund. By pumping and keeping out all water we created a large, eighteen-meter-deep polder. In this construction pit we were able to build the quay wall and the two jetties,” he explains.
Construction of ring dike
Operations began after an intensive design phase and extensive soil surveys. The trailing suction hopper dredgers Queen of the Netherlands and Prins der Nederlanden pumped in millions of cubic meters of sand through a floating pipeline for the construction of the ring dike. The sand was brought in from a borrow area about twenty nautical miles offshore. The hoppers sailed three times a day from the borrow area to the connection point, where they pumped tens of thousands of cubic meters of sand through a floating pipe to the location. At the same time the hopper dredger Crestway was carrying out maintenance dredging work in the existing access channel and port basin. “We took the prevailing environmental requirements relating to turbidity into account during this operation,” says Bart. “We considered the needs of local fishermen in our operations and we put procedures in place to ensure that we didn’t disturb the colony of whales living in the area by having our mammal observers on the hopper dredgers.”
New cutter suction dredger Helios
The new mega-cutter Helios played a major role on the project. With a total installed power of almost 24,000 kW, a pumping capacity of 15,600 kW and a maximum cutter power of 7,000 kW, the Helios is one of the most powerful cutter suction dredgers in the industry. The 152-meter-long vessel was developed to operate in extremely hard ground. “The Helios started the first phase of dredging for the entrance channel to the new port area and began excavating the outer section of the port basin,” explains Bart. “During this first phase, we also came across a layer consisting of a tough mixture of rock and clay-like material that was difficult to dredge with the existing cutterheads. To tackle it better, our team of specialists designed new cutter heads that were built specifically for the Duqm project in a record time of five months.” Using those cutter heads, the Helios removed the majority of the 20 million cubic meters of rock and clay-like soil in the second phase of the project.
Large-scale excavation and earthmoving
The dry excavation of the pit and the large-scale earthmoving were carried out under the supervision of colleagues from Boskalis Nederland involving over 80 units of dry earthmoving equipment. “The excavated soil was beneficially reused and taken to a location in the vicinity of the project site to build new port areas in the future,” says Bart. “For the maintenance work on cranes, excavators, bulldozers and trucks, a large workshop was set up by colleagues who know all that equipment like the back of their hand. By the time the excavation work was finished, 9.3 million cubic meters of soil was removed. It was a colossal project in every respect.”
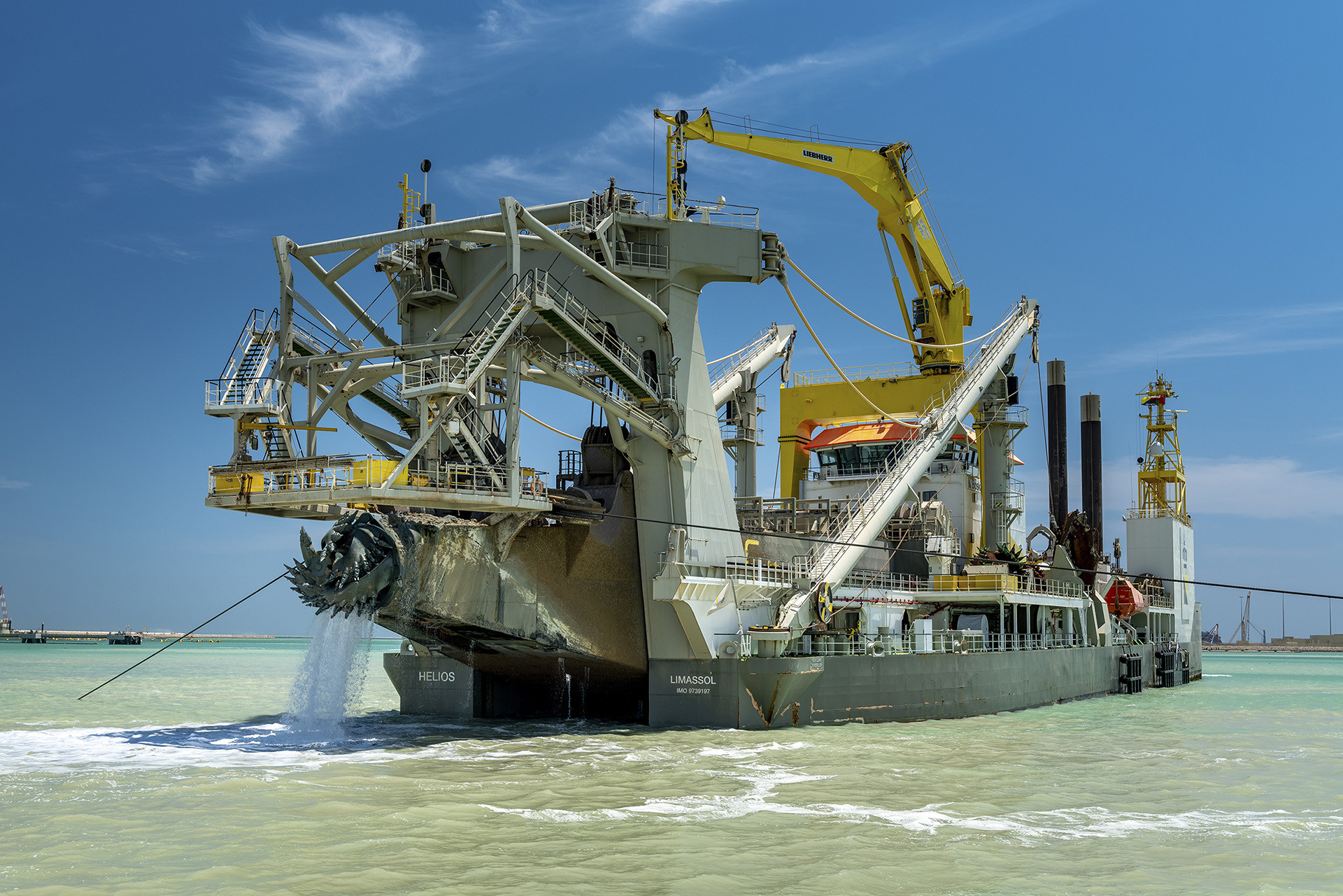
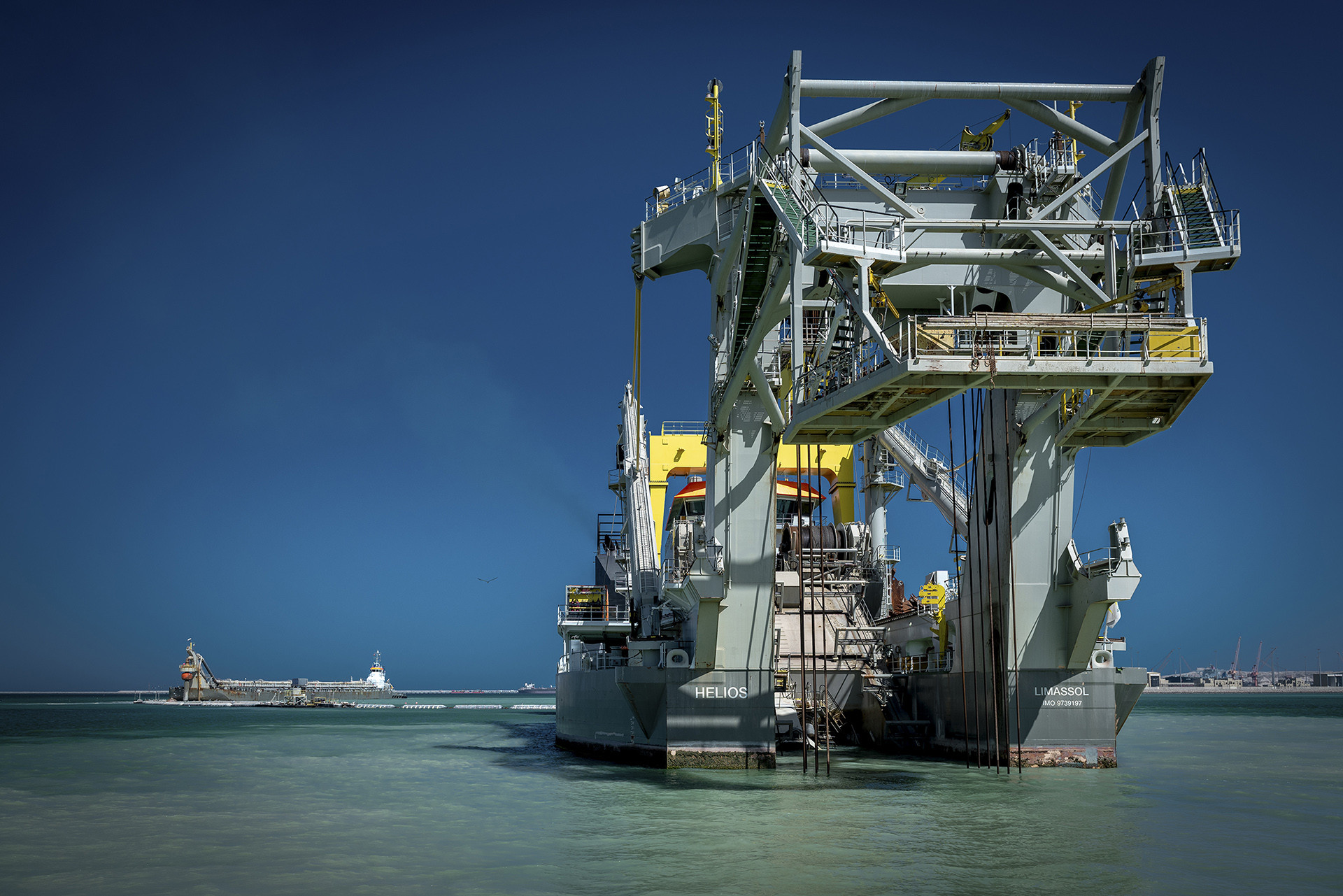
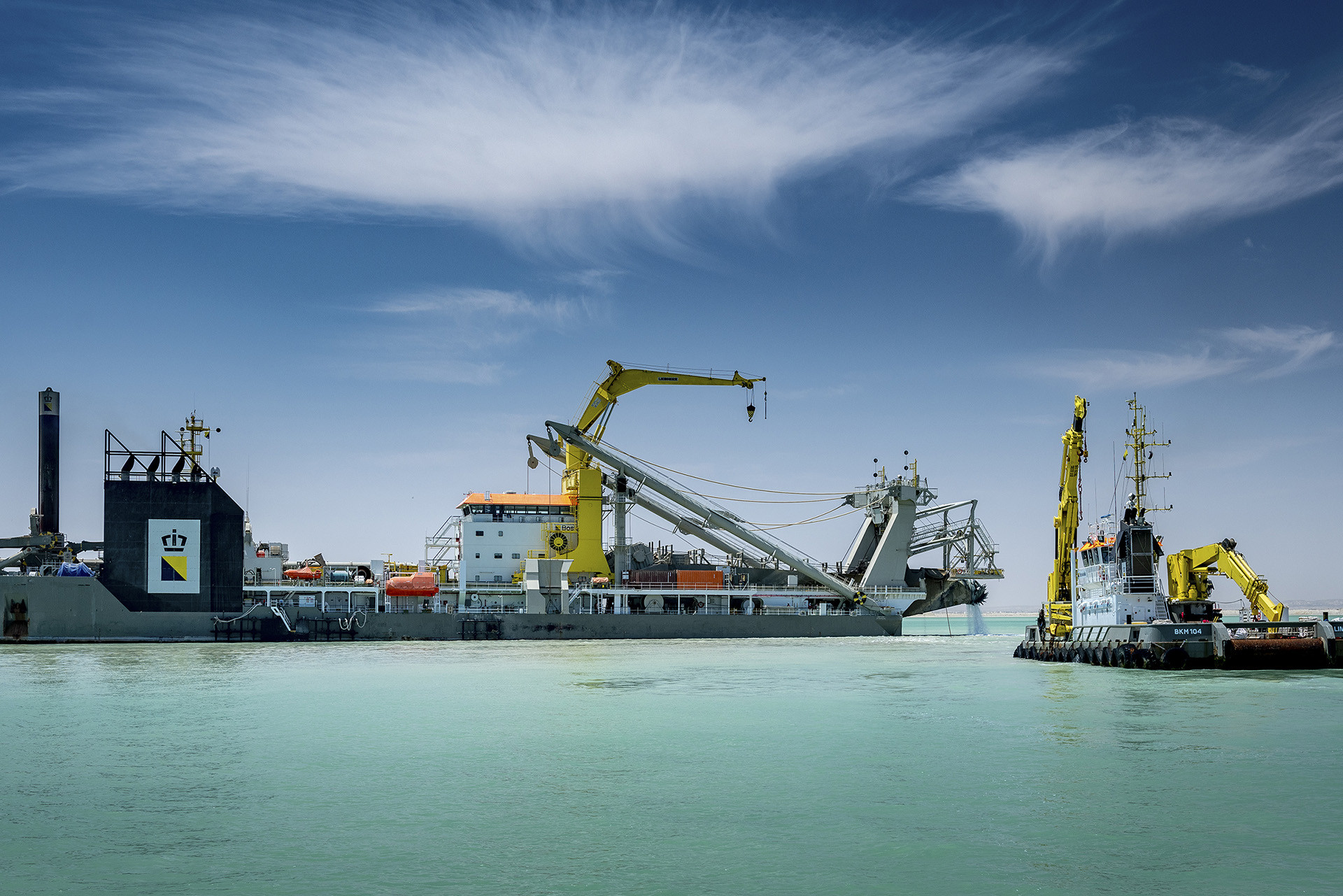
BY THE TIME THE EXCAVATION WORK WAS FINISHED, 9.3 MILLION CUBIC METERS OF SOIL WAS REMOVED. IT WAS A COLOSSAL PROJECT IN EVERY RESPECT.
Boskalis Nederland was also involved in the construction of a rock slope, which was covered with geotextile and rock. Some of the rock came from an existing breakwater, which forms one edge of the port area. The rock was removed from the inside of the breakwater before the sand was put in.
Compaction of reclaimed land
The colleagues from Boskalis subsidiary Cofra also had an important job to do. “To comply with the stringent demands for the compaction of reclaimed land, Cofra set up a special testing area to study the best possible approach to compaction,” says Bart. “They brought in heavy plant, including large dynamic compaction machines, to compact the land in the reclaimed areas. In the deeper sections of the landfill area we had to use the vibro flotation instead of the dynamic compaction method. Here too, Cofra played an important role by bringing in expertise on site to manage our subcontractors that executed the vibro compaction activities.”
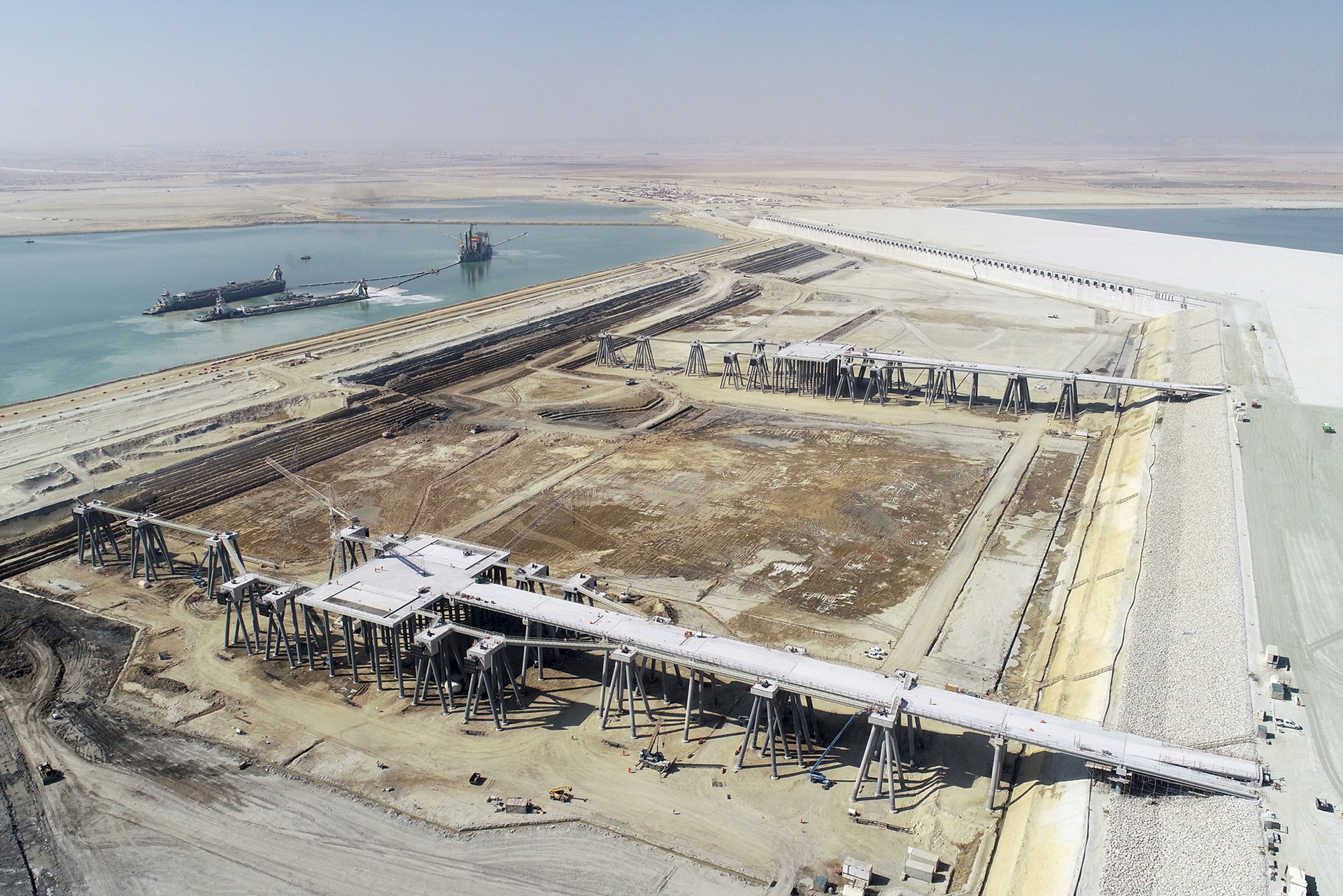
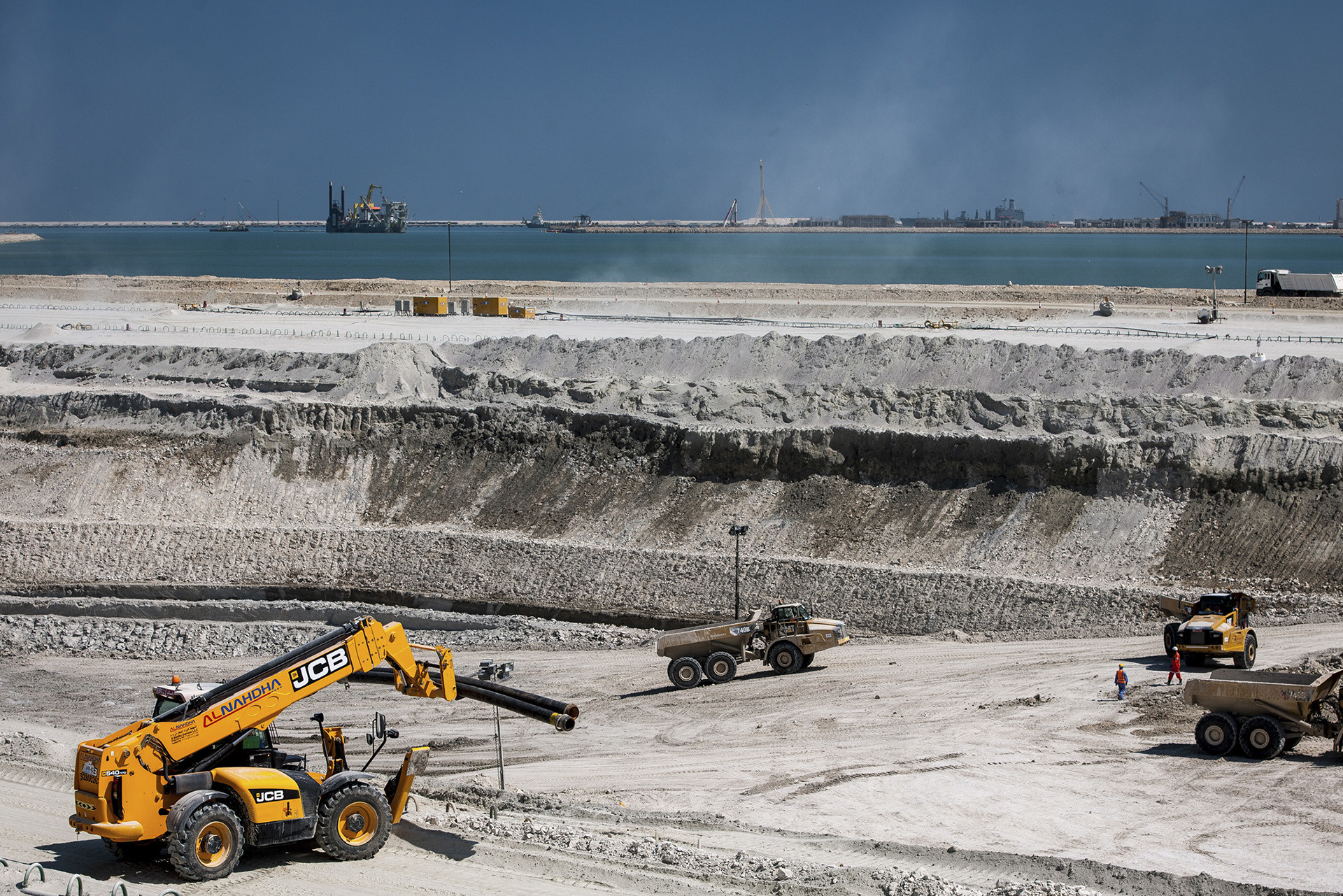
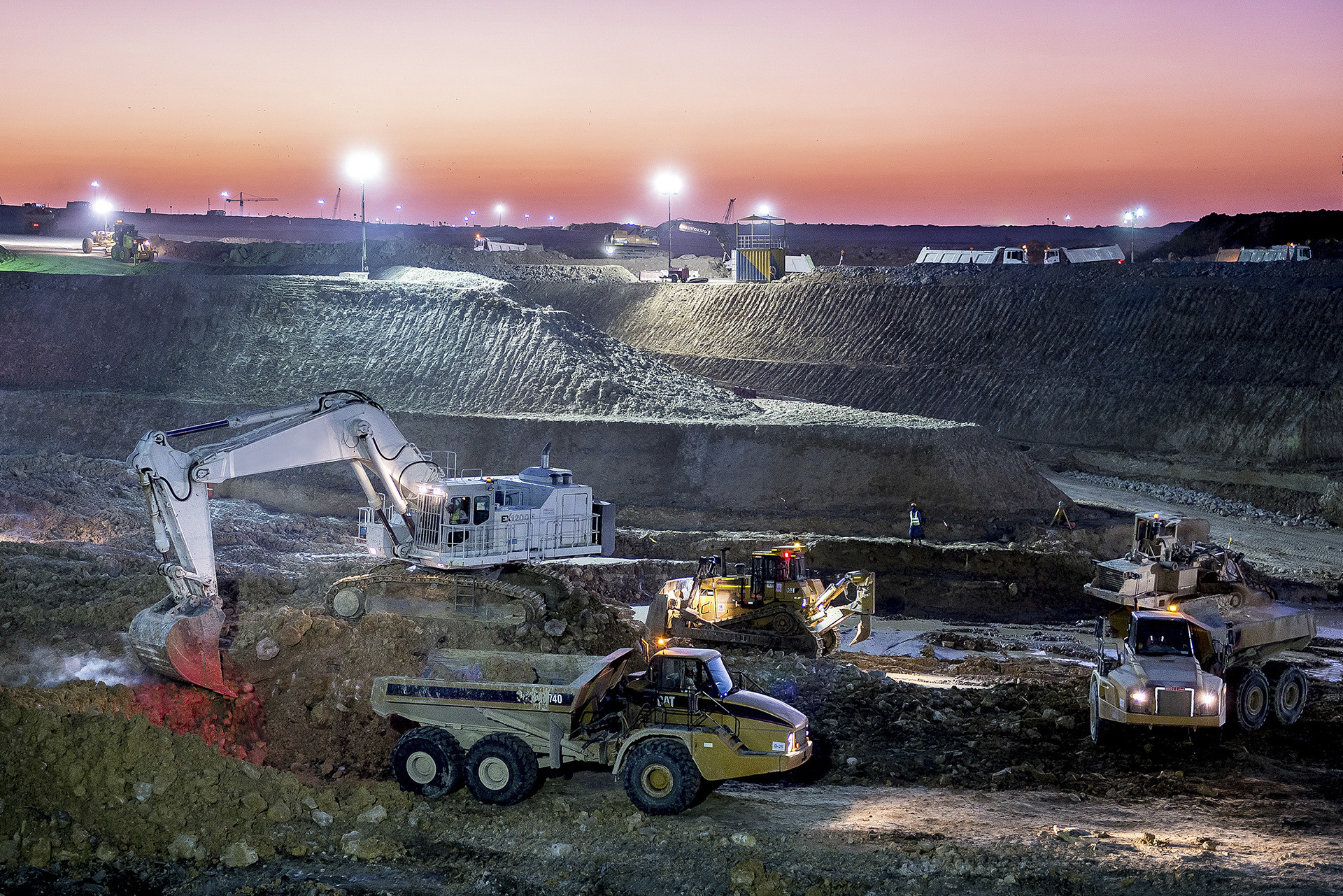
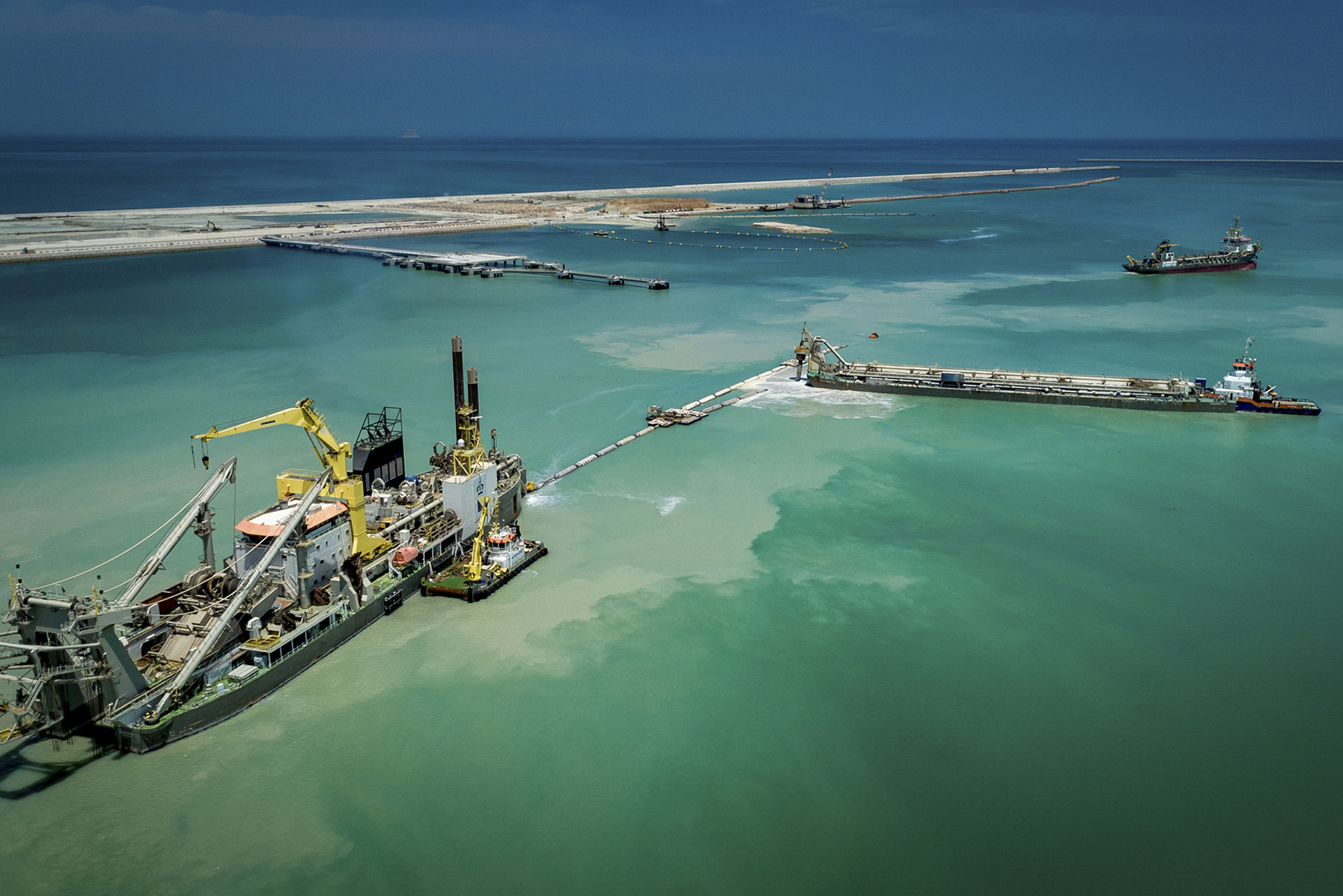
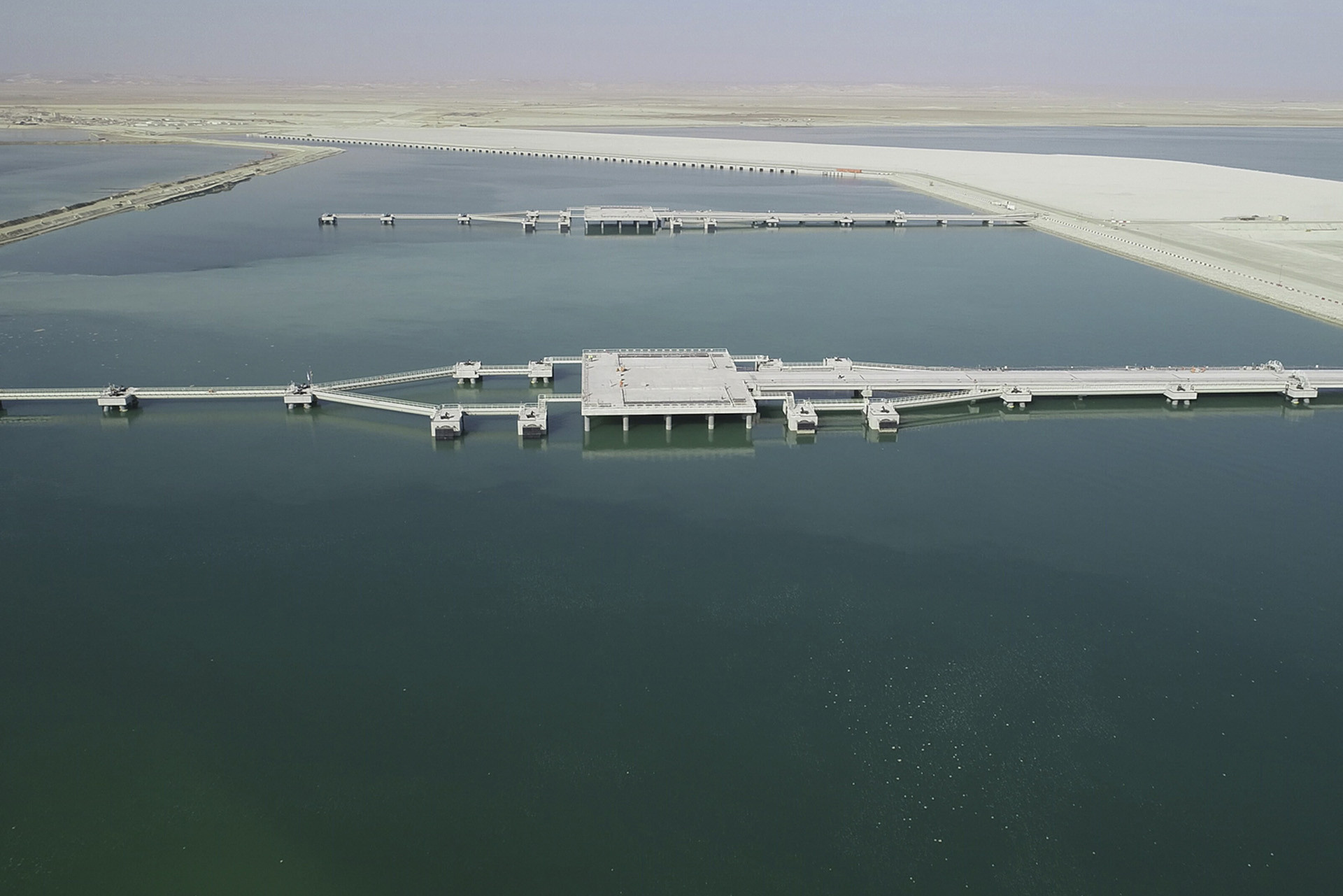
Training
As the work progressed about 1,500 people from 25 different countries were working on the project every day, including the staff from partner Six Construct. “In addition to our colleagues from numerous disciplines at Boskalis there were a lot of local employees as well,” says Bart. “More than 10% of the workforce was from Oman, and there were many operators from Pakistan and India.” In order to train the inexperienced local drivers and operators to the required standard, a simulator was installed and local trainers and interpreters were called in. Besides a large number of dry earthmoving equipment, 25 new trucks were brought from the Netherlands to Duqm. The drivers were first tested on the simulator and, with the help of the SHE-Q colleagues, trained by the superintendents to work efficiently and safely.
Safe working environment
“We have really gone the extra mile on this project to ensure a safe working environment for all our project staff and vessel crews. It was a major challenge for our designers, engineers and supervisors to make sure that the bund complied with the strict requirements for strength and dewatering,” explains Bart. “Working in such a huge building pit surrounded by water created potential risks for our staff and project and involved all sorts of safety considerations. We had a range of monitoring systems in place for the bund to ensure that it wouldn’t slip, leak or break unnoticed. You always have to keep in mind that something can go wrong and as we know from other dike failures this can take place quite quickly. We have spent a lot of time on good rescue equipment, including ladders and rafts to get out of the pit safely in just a few minutes. In addition, the development of evacuation plans and regular drills measuring the time to get all staff out of the pit contributed to ensuring this safe working environment. Our safety awareness program NINA played a crucial role here. NINA courses and toolbox meetings were organized from the outset, and the use of Safety Hazard Observation Cards was taken very seriously. And I am proud to say that our strong focus on safety has paid off. At the end of the project we celebrated the fantastic landmark achievement of more than six and a half million man-hours without a single lost-time incident. That is a direct result of the efforts and dedication of all project members and of our joint commitment to create a safe working environment.”
WE CELEBRATED THE FANTASTIC LANDMARK ACHIEVEMENT OF MORE THAN SIX AND A HALF MILLION MAN-HOURS WITHOUT A SINGLE LOST-TIME INCIDENT.
Quay wall and jetties
In the polder, partner Six Construct constructed the enormous quay wall. The more than 5,000 large concrete blocks that were required for this operation were produced in the specifically prepared casting and laydown area on site. At the same time, impressive steel structures for the two 400-meter-long jetties were built in the middle of the polder. This involved installing 330 large steel piles that were then connected to each other with steel beams and in situ poured concrete platforms and abutments.
Flooding the polder
Many contractors and architects of monumental buildings can proudly show their work to their friends, children or grandchildren. With Boskalis’ hydraulic engineering projects, the situation is usually different: dredging work and maritime infrastructure are often hidden from view below the water. The project in Duqm is no exception. Following the completion of the construction works, the polder was flooded using large siphons. As the water in the polder rose, most of the quay wall and the giant steel structures of the jetties slowly disappeared from view. The bund was removed by dry earthmoving equipment and by the small cutter suction dredger Ceres. The mega cutter Helios removed the remaining rocky material underneath the constructed sand bunds.
Extension
As an extension of the contract an area of 1,800 by 350 meters was reclaimed along the breakwater. Again the sand was brought in from sand borrow areas, this time by the mega trailing suction hopper dredger Fairway. The area was compacted and the banks were covered by rock for protection. These activities were carried out in parallel with the last section of maintenance dredging and in combination with the water injection dredger Terra Plana for the final delivery of the project. “From a technical and logistical point of view, we have achieved something very special here,” Bart concludes. “Perfect coordination between all different Boskalis and subcontractor disciplines was required to execute all the different tasks, without literally tripping over one another. Making sure all the different work disciplines were able to excel and at the same time stayed in tune with each other was the main challenge on this job. Thanks to our fantastic teamwork we can all be very proud that we produced a first class symphony in time and to the full satisfaction of the client.”